ROTALOC INTERNATIONAL
Rotaloc specializes in metal inserts and custom fastening devices for plastics and composites. It supplies fasteners and related components for the rotational molding industry, as well as for injection molding, thermoforming and composite molding. Standard products include a range of fasteners such as hex, square and round inserts, fittings, bulkhead assemblies and large anchors. Many of Rotaloc’s fasteners are designed to be molded into the plastic part.
“Our fasteners aren’t generic,” Rotaloc founder Steve Harris said. “We specialize in providing a range of products that integrate into plastics and composites applications having unique requirements. We design fasteners for the materials our customers use and the forces that the parts will be subjected to. We understand how plastics and metal products must integrate to achieve desired results.”
Harris noted that Rotaloc uses a combination of fabrication techniques, some proprietary, to produce fasteners that not only meet performance requirements but are cost-competitive for users. “Many customers looking for fasteners end up taking what’s available on the market,” he said. “We design fasteners that are specific to the needs of plastics and plastics structures.”
Rotaloc uses a variety of processes and routinely produces components ranging in size from about 0.5 inch to 4 inches, as well as parts that are much smaller or larger. Common metals used include aluminum, brass, stainless and other steels and occasionally titanium.
Rotaloc is expanding its ability to make custom products to provide practical and economical solutions to challenging applications. One fastener the company recently developed using its plastics expertise and fabrication techniques is its Geosert in-mold inserts for rotomolded parts that fit into tight spaces where it would be difficult or impossible to use large conventional flanged or hexagonal attachments. Available in aluminum, brass, stainless steel or mild steel, the hexagonal, threaded inserts have twice the torque strength and three times the pull-out strength of conventional fasteners, Harris said.
TRI-STAR INDUSTRIES
Tri-Star makes threaded metal inserts for plastics that can be molded in, pressed in or installed using ultrasonic vibration or heat. The company often fills custom orders, sales engineer Aaron Edelson said. “Customers send in specs for special applications,” he said, which include metal substitution. For example, plastics processors are increasingly requesting aluminum in place of brass. Aluminum is lightweight and strong, and some grades have no lead, which is necessary for end products in certain markets affected by various hazardous substance regulations.
Among the capabilities that aid in the development and supply of custom fasteners at Tri-Star are multi-spindle and Swiss-style CNC machines. The CNC machines have multiple axes (usually seven to 13) and are good at fabricating small parts with tight tolerances in low-volume runs. Examples Edelson cited included inner-diameter tolerances as low as 0.0001 inch on fasteners for molded-in parts. He said that, with the machines, the company efficiently produces as few as 1,000 prototype fasteners, compared with runs in the hundreds of thousands on conventional CNC machines.
Tri-Star’s custom business also improves its position as a Tier 3 supplier. Tier 1 and 2 vendors solicit quotes for fasteners they need to assemble components for OEMs. Tri-Star is looking to cut its lead times in half by investing in its lean manufacturing capabilities.
Pat Toensmeier, correspondent
Contact:
Rotaloc International LLC,
Littleton, Colo., 303-948-5434, www.rotaloc.com
Tri-Star Industries Inc.,
Berlin, Conn., 860-828-7570, https://tristar-inserts.com
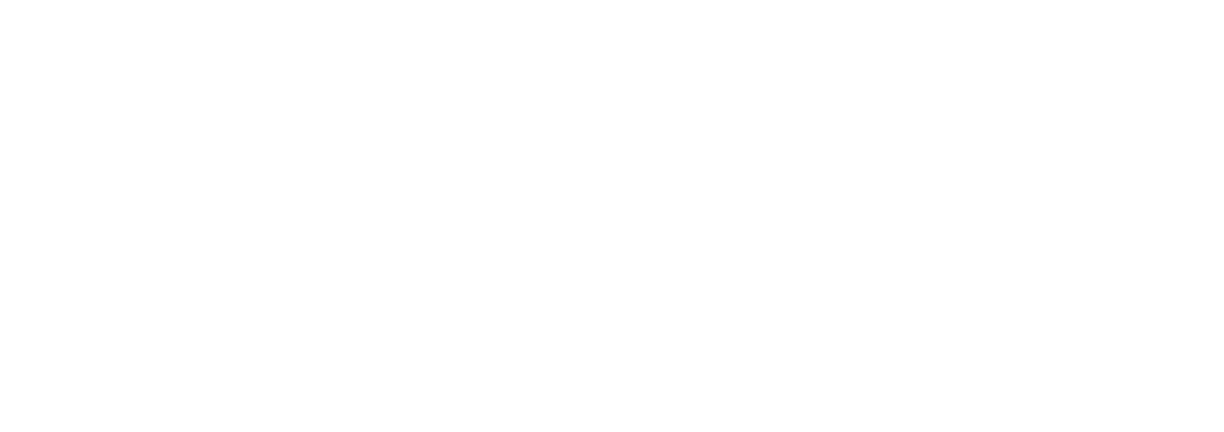