Its plastics manufacturing facility in Turtle Lake, Wis., is under the direction of GM Scott Schoenborn, who has its 300 employees on a purposeful path to implement scientific molding so that parts inspection will no longer be needed. The factory produces up to 1 million cell phone cases per month.
“Two years from now, my goal is to stop inspecting the parts,” Schoenborn said on a recent Plastics Machinery Magazine tour of the site, where presses combined with automation are pumping out parts for medical, industrial, security and electronics applications.
But it’s a journey to get there, with 73 injection presses with clamping forces ranging from 28 tons to 1,000 tons. Flexibility is key to maintaining production, especially when some of the contracts are seasonal. With the goal of repeatable, consistent parts manufacturing, Schoenborn and his team are evaluating the design of the tool, component and manufacturing process, as well as analyzing mold flow and resins.
“We are migrating more and more to scientific molding,” he said. “The reason I’m saying ‘migrating’ is that we are designing and building new tools that support scientific molding, but we have a very good customer base that is legacy. They deserve our support and they need our support, but those tools weren’t necessarily designed and manufactured to support a robust process.”
Starting with the process engineering manager who is an expert in scientific molding, Schoenborn capitalizes on his people and what they know, emphasizing that it takes a community approach.
“It’s built on interviewing people, knowing that the proper way to build this plant is around scientific molding to have that customer confidence that every time you’re making a proper part. We interview people that know what they’re talking about. When the process engineering manager started hiring his process technicians, they didn’t necessarily know scientific molding. We interviewed for, ‘Are you able to learn, comprehend and apply?’ Then we send our technicians to RJG training. All of them have [basic] Level 1 [training]. One of the process technicians has Level 2. You can see the growth and improvements.”
Machinery and equipment amalgamation
Key to scientific molding is the choice of machinery and equipment. Across the factory floor in Turtle Lake, a mix of injection molding machinery brands produces the parts that make their way throughout the world, including to Sanmina’s other plants.
“We are not brand-driven,” Schoenborn said. “We are proper-equipment-configuration-driven to meet the customers’ requirements. If that means it is an Arburg press, then that is what we will buy. If it means it is a Sumitomo, then that is what we will buy. Again, the equipment goes back to scientific molding. The equipment has to be capable of producing the proper outputs for the tool, resin, all to work properly, to meet the customers’ specifications.”
But the ultimate machinery and equipment purchasing decisions are made by a democratic process.
“Even when we make a simple press selection, the operations manager drives that in coordination with the engineering department. We all work hand-in-hand. What do we have for capacity? Is this the proper equipment for all different disciplines? We do not want one discipline making the machinery selection. This filters out to all the other departments; if you do not make the right decision, it’s going to have an impact,” he said.
Materials-handling equipment comes from suppliers such as Dri-Air and Conair. To create more space on the production floor, much of it is located on a mezzanine.
Schoenborn highlighted innovation throughout the facility, most of it created within this very factory.
Take, for example, the mobile clean room that is performing to Class 100,000 standards. It is not yet officially certified. On the day of PMM’s visit, Sanmina was producing cell phone cases, which do not need to be produced in a clean room. But Schoenborn and company built the cell for flexibility.
“I wanted to prove with this molding cell that we have the discipline; we have the technology and the capability to do it very cost-effectively,” he said. “I could take the plant and turn it in to a Class 100,000 clean room, $25 million later. It didn’t cost me a whole lot because I have maintenance guys here, automation guys here, that are included in my overhead. The customer likes it. You’re running that product for them; they are happy. You want to run another customer’s product, what’s the worst that can happen? You’re going to have it cleaner than they need it. If the market changes and you don’t need that anymore, disassemble it, put it in the warehouse, you can reassemble it later for another customer.”
In the first press, the robot loads a label that is held in the mold by static. “In the automation of the robot and all the automation around it, we incorporated a way to hold them in with static instead of vacuum because, if you use vacuum, it will leave a mark,” Schoenborn explained. That in-mold label then is molded to clear PC, which forms the substrate. The substrate is removed from the mold, cooled properly and then moved to the second press, which molds a clear TPE outer perimeter.
“We did not have to invest in a two-shot press,” he said. “We had to buy the robot, but we already had the presses. Even if I did buy two conventional [presses], it probably would be a little less than an equivalent two-shot molding machine. From my standpoint, that is a good investment. Yes, I have to buy the robot, but all the rest of it, the clean room and the automation, was built internally. I’ve got two simple, conventional tools. One does the substrate, the other does the overmolding. You can build both of those tools more cheaply than you can a two-shot.”
In another case, the Turtle Lake site made life easier for a sister plant that was building a three-part front bezel used in a data-storage device. The sister plant was mechanically fastening the three parts, a time-consuming process that risked scratching the finish.
Turtle Lake’s engineers used sequential valve gating in the tool to prevent cosmetic blemishes. The end result was a 30 percent reduction in manufacturing costs; a $25,000 savings on tools and a 25 percent reduction in the assembly time of the finished part.
Home-grown testing
Schoenborn and his team devise testing systems in-house that take care of problems their clients might encounter. A medical client, for example, needs a product that is used by doctors performing neck surgeries. Due to the risk of paralysis if a nerve is hit, the surgeons needed a device that emits a sound to alert them if they are getting close to the nerve. The sound grows louder as the surgeon gets closer. As part of its stringent quality-control program, Sanmina needed to ensure that the speakers in the assembly worked properly.
Sanmina created a device that applies a specific voltage to the assembly and then uses four high-precision laser sensors to determine if the speaker cones are vibrating in the proper direction and at the correct distance, Schoenborn said.
“We are innovative,” he said. “We like to help customers with problems.”
Sanmina officials faced another challenge when they took on the manufacturing of light pipes — tubes that can be used in electronics, as well as other parts, to transmit light. Sanmina needed to eliminate variability in the pipes’ performance and ensure that the pipes allowed the transmission of the appropriate wavelengths and light intensity. To do so, the company developed a tester that measures light intensity input and output and precise light color.
“With this tester, we can establish lower tolerance limits on light transmission, as well as tolerances on color,” Schoenborn said. “This had previously been undefined. Through the use of designed experiments, we are establishing the process parameters that most influence the final light output and color. With this knowledge, we can provide consistent, acceptable product to the customer.”
Angie DeRosa, managing editor
Contact:
Sanmina Corp. Plastics Division
Turtle Lake, Wis., 715-986-4407
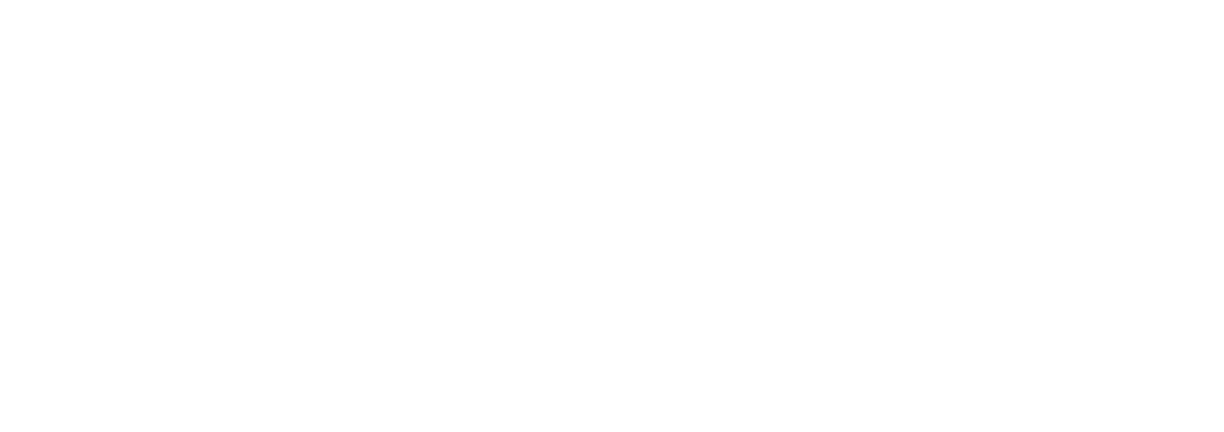