Based on the HyPET HPP5 injection molding system, which Husky introduced in 2013, the HyPET HPP5e also is reliable and easy to use, for faster cycle times, improved preform quality and lower operating costs, the company said.
Intelligent adaptive technology is the key to reducing energy consumption and operating costs, said Glenn Chessell, GM of PET and packaging systems for Husky’s rigid packaging business.
“Intelligent adaptive technology is a combination of learning software and hardware,” Chessell said. “This technology takes feedback from pressure and actuator sensors, and adjusts the pressure, if needed, to optimize production.”
“If the operator adjusts the settings on the machine, the intelligent technology adapts to those changes,” Chessell said. “It gets information from pressure transducers and sensors to make sure there is no negative effect on the performance of the system. The intelligent adaptive technology will drive the machine pressure down to the lowest amount needed to maintain the system’s highest performance.”
By continuously comparing data from the machine with ideal set points and adjusting the pressure, the technology modifies the operation of the machine for maximum efficiency.
“The purpose is to maximize energy savings, and one way to do that is by reducing pressure,” Chessell said. “
REDUCING PREFORM BOUNCE
Other modifications make the HyPET HPP5e more robust and reliable, Husky said. New conveyor technology largely prevents preforms from bouncing, improving part quality and streamlining operation.
“After the mold opens, a robot enters the molding area and removes the preforms with a multi-position take-off plate,” said Reinhart Drawetz, product manager for preform systems. “They are then transferred to the CoolPik unit, where the preforms continue to cool. The multi-position take-off plate cools the exterior of the preform, and the Coolpik unit cools the interior of the preform, maximizing cooling efficiencies and speed.”
After the preforms cool, the CoolPik unit ejects them onto the conveyor, which limits the amount of bounce and contact the preforms have with each other, as well as with surrounding areas of the conveyor, thereby preventing damage. “This improves preform quality,” Drawetz said. “It also improves system performance by containing the preforms inside the conveyor area.”
ENHANCED SOFTWARE
Enhanced mold-alignment software provides faster system setup and troubleshooting.
“The software was developed by Husky to simplify and ensure accurate mold alignment when the mold is installed into the machine,” Drawetz said. “It helps prolong mold life by reducing wear caused from poor alignment.”
As the machine is operating, the software continues to monitor alignment.
“If it goes out of specification, the software
will warn the operator that realignment needs to be done by sending a notice that appears on the system’s HMI screen,” Drawetz said.
Improved EtherCAT diagnostics make the system easier to navigate, more convenient to set up and faster to troubleshoot.
“The EtherCAT diagnostics software also allows our team to better connect to machines in remote locations in real-time,” Chessell said. “Internet connections are not always reliable worldwide, so if the internet connection to a machine in a remote location is down, we can walk customers through diagnostics using screen shots. The new capability allows customers to screen-capture the diagnostic images and then transfer them to Husky.”
Other HyPET HPP5e advancements include:
• new robot linear bearings that extend robot life;
• HMI screen upgrades that simplify use;
• changes to flow sensors that support more consistent cooling of mold and take-off plates;
• upgraded integrated circuit cards that provide more accurate temperature control and increase communication speed;
• and a new nozzle shut-off cylinder that isolates cylinder components from external heat sources to improve performance and increase component life.
Bruce Adams, senior staff reporter
Contact:
Husky Injection Molding Systems Ltd. Bolton, Ontario, 905-951-5000,
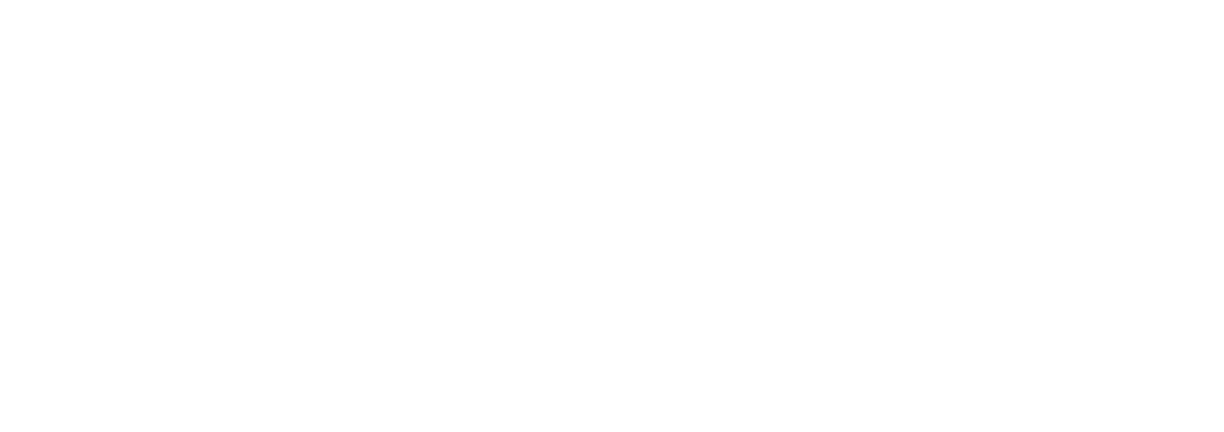