It has been an interesting process for Jarden Plastic Solutions, which four years ago recognized an opportunity offered by a new blow molding technology from Italian machinery maker Sacmi Group — compression blow forming (CBF). Jarden is now on the cusp of beginning commercial production of thin-wall pill bottles using the CBF process for one of the pharmaceutical industry’s biggest manufacturers and believes the new technology could eventually double its current plastics business.
By the end of this year, Jarden will have nine CBF machines running in four plants. Production time on all nine machines is pretty much already sold out, according to Todd Zillmer, director of design, engineering and development for Jarden. Further expansion is anticipated. Jarden would not name the pharmaceutical company.
“The project started in a restaurant parking lot with a pharmaceutical company senior engineer after a business meeting in King of Prussia, Pennsylvania,” Zillmer said.
“They were already a Jarden customer and needed a launch partner for this project,” he said. “The next day I contacted Sacmi in the U.S., but it quickly evolved into a relationship with Sacmi headquarters in Imola, Italy, because of the potential size of our project.”
In the four years since that parking-lot meeting, Jarden, the pharmaceutical company and Sacmi have been joined by Dow Chemical Co. and Milliken & Co., a chemicals company that developed the special passive barrier properties for the resin. Milliken’s additive package, called UltraGuard, is incorporated in HDPE as a masterbatch.
Todd Zillmer, director of design, engineering and developmentPMM“Milliken’s UltraGuard with the special mix of HDPE we are currently using, combined with the CBF process, that is the magic,” said Zillmer. “The combination makes it hum.”
As word of Jarden’s first CBF project has spread, Zillmer said other Top 20 pharmaceutical companies have been calling to ask what Jarden can do for them.
Jarden demonstrated its 20-station CBF process during a recent Plastics Machinery Magazine visit to its Greer, S.C., plant. Sacmi’s patented CBF machine combines compression molding and blow molding into a single process. A single machine turns the resin into a finished bottle.
The Sacmi machine produces about 160 bottles per minute but is capable of 200-plus bottles per minute, depending on the design.
“CBF is a plastic forming operation unlike any other,” said Justin Saleski, Jarden’s business development program manager responsible for the CBF project. “It has one continuous extrusion process that offers a level of consistency you don’t get in other plastics forming processes, either injection blow (IBM) or extrusion blow molding (EBM).
“With the compression stage, you end up with a preform that has a much more consistent wall thickness,” Saleski said. “Put in this level of part-to-part consistency with uniform wall thickness, the right materials to provide barrier properties, and your only limit is the structure of the bottle itself.”
Jarden is developing several different standard and custom-sized pill bottles for customers.
The CBF process is well-suited for pharmaceutical bottles because it results in:
• consistent wall thickness, which enables lightweighting;
• cycle-time reductions of as much as 30 percent;
• less than 1 percent scrap;
• lower energy costs due to the use of lower temperatures;
• and less shear stress on the preform in the compression step.
The advantages of using less resin, reducing scrap and saving energy make the cost of CBF bottles competitive with traditional blow molded bottles.
In the meeting in which the pharmaceutical company awarded Jarden its pill bottle business, Zillmer recalled a VP from the company saying, “It’s hard to believe we are awarding our bottle business to a company that has never blown a bottle.”
The injection molding plant-floor teams have had to learn the new CBF process. “No one in the plant had blow molding or compression molding experience,” plant manager Joe Ervin said.
“We sent some people to Italy and, when the Sacmi teams were here for the commissioning and later validation of the machine, we learned a lot from them,” he said. The Sacmi maintenance team will be invited back when it is time for major maintenance, Ervin said.
Saleski said the CBF machine poses a challenge only in the initial setup. “Once it is set up, you don’t need to touch anything,” he said. “When the first gob of plastic is extruded in the first stage, 100 percent of it becomes a product.
“One of the final steps has eight inspection cameras, so by the time you get the first bottle through the system, you know it is dimensionally correct and there has been very little start-up waste.”
Saleski said it takes approximately half of one operator’s time to run the CBF machine. “Most of that is building boxes,” he said.
A Niigon Direct Co-Inject pressPMMJarden has invested a significant amount of time and resources in the material science and process development related to the project. All that effort has resulted in a patented manufacturing process to ensure Jarden’s customers receive bottles that exceed their strict requirements.
Zillmer and Saleski both said they think it is easier for an injection molding company to launch a CBF operation than for a traditional blow molder to do CBF.
“It is much easier for a company that is not a previous blow molder with a big investment in blow molding equipment to get into the CBF platform,” Saleski said. “It is also easier to teach an injection molding engineer how to compression blow form than going the other way. It was a great fit for us.”
Jarden currently has six CBF machines, with two more being built. One other machine, with a new design, will be displayed at the K show in October, then shipped to Jarden. One is in the plant in Greer that PMM visited, while four of the first nine are slated for installation in a new plant in Puerto Rico, three for Jarden’s Springfield, Mo., plant and one for Christchurch, England.
The nine machines will make Jarden the largest single holder of Sacmi CBF machines in the world.
In addition to their onboard quality-assurance systems, the CBF machines come equipped with Piovan auxiliary equipment. The conditioned air for the post molding conveyor they use is supplied by a chiller from Industrial Frigo.
JARDEN'S INJECTION MOLDING
The Greer plant has 29 injection molding machines spread between a Class 8 clean room and a white room. The clean-room products are mostly related to eye care, including packaging blisters, cases and covers for contact lenses and several closures for saline solution. Medication dosage cups used in hospitals are also produced in the clean room.
The white room follows the same procedures as the clean room but does not have an air-exchange system to control particulate count. Parts molded here include several products for leading lip balm manufacturers, housings for a global lawn-care manufacturer and closures for a wide variety of liquid dispensing containers.
Approximately 70 percent of the Greer plant’s production involves medical products.
The presses have 80 tons to 385 tons of clamping force. Companywide, Jarden has more than 200 molding machines; 75 percent are from Netstal. The same percentage holds true for the Greer plant.
“We have had a strong relationship with Netstal for 30-plus years dating back to our origin as Unimark Plastics,” Zillmer said. “We have just about every one of the machines Netstal makes in each of our plants — SynErgy, Evos and Elion. Some have been running the same product for two decades.”
The long relationship with Netstal means that Jarden does not often test new injection molding presses. The exception came two years ago, when Jarden was looking for alternatives to using stack molds, which are complicated and can be problematic to run.
The answer was Athena Automation Ltd. in Vaughan, Ontario, which has since changed its name to Niigon Machines Ltd. The relationship started with a conversation between Jarden President Mike Zaagman and Athena founder Robert Schad.
Jarden worked closely with Niigon and a key tooling partner to develop what is now a Jarden trademark, Direct Co-Inject (DCI). The DCI press can run two molds at the same time and provides a tremendous amount of flexibility in part geometry, materials, colors and post-molding operations. Jarden has plans to have nearly 10 DCI presses running in four of its plants this year.
“Two years ago, before we bought a press from them, we took one of our 96-cavity molds to Athena and challenged them to run it hard for eight hours to test their machine’s repeatability,” Saleski said. “We ended up liking the results and committed to their platform of new machines.”
Zillmer said the partnership with Netstal helps Jarden serve its customers.
“Although I am a huge proponent of Netstal, I was open to the idea of Athena as a new partner as we continue to innovate and provide solutions to our key customers driven by technology. There is something to be said for a machine designed in today’s world versus something designed 20 or 30 years ago,” Zillmer said.
The Greer plant’s two Niigon presses were delivered last year and make about 300 million parts per year in each mold. Each has 350 tons of clamping force. They sit side by side in the white room and produce components needed for a four-piece assembly. The four molds consist of two with 96 cavities and two with 64 cavities. One machine makes two of the components with an 11-second cycle time and the second machine makes the other two components with a 7-second cycle time.
“The customer gets the benefit of higher cavitation,” Zillmer said. “These are the first two Direct Co-Inject machines running production anywhere on Earth!”
He said the Niigon presses can use hydraulic or servo ejection via a custom-built center section. The four molds run completely independently of each other, and, in this case, run both PP and PE.
Jarden has standardized much of its auxiliary and other equipment. It has blenders from Maguire, dryers from Wittmann and high-speed robots from Yushin.
“We did some side-by-side testing of other high-speed robots, and Yushin was the best,” Ervin said. “We have used them for a long time and upgraded them along the way. We use Yushin’s HSA ultra-high-speed take-out system, and they are fantastic, day in and day out, running 5-second cycle times.”
While some products run for long periods of time, other production runs can be as short as eight to 10 hours, Ervin said. The plant makes one to four mold changes per day.
The plant has two separate materials-handling systems, one for the clean room and one for the white room. Its materials-handling components are mostly from Conair. Resin is delivered by tanker trucks and stored in seven silos. Each press has its own loader and pulls resin from the silos as needed, Ervin said.
Many presses have custom-built, circular bagging systems that can accommodate six bags. Each bag holds about 6,000 parts. Parts must be cooled before they are dropped into the bags.
Conveyors and box-handling equipment are custom-built for Jarden by Harvard Factory Automation Inc., which has been a strategic partner for nearly 10 years.
The clean-room operation includes a good deal of press-side automation. For example, a lens case and cover are molded in a 24-by-24 stack mold on a 385-ton Netstal press. The cases are molded inline and are fed into the automation via a vibrating bowl built for Jarden by United Toolers of Illinois (UTI). The left and right caps are fed into the system via UTI bowls where they then are assembled by a Haumiller continuous motion machine.
There is an on-site materials-testing lab, along with an impressive metrology lab to support validation activities, as well as day-to-day tasks, to ensure Jarden’s customers receive world-class products.
All the utilities, as well as the resin, enter the clean room from an underground tunnel.
The plant uses a manufacturing execution system (MES) from Mattec. Large, wall-mounted screens show the status of all machines in the plant. The system pages a technician when a molding machine or auxiliary equipment needs attention. “It helps maximize our uptime,” Ervin said.
The MES includes a screen at each press where an operator enters downtime and scrap for the machine.
The Greer plant has 140 employees and runs 24/7. Worldwide, Jarden has about 800 employees.
Ervin said the turnover rate at the Greer plant is a single-digit percentage. “Technical skills are getting more difficult to find, but the Southeast still attracts a lot of people who want to work,” Ervin said. The plant uses RJG Inc. for some training and has several RJG-certified Master Molders on staff. Other employees use Paulson Training programs and take plastics- related courses at the local community college.
The current facility is close to capacity in terms of physical space, but the company plans to add molding capacity in an adjacent building currently used for assembly operations and warehousing.
Jarden has invested significant capital over the past 24 months to add clean-room molding halls in its Reedsville, Pa., and Christchurch plants, as well as the brand-new plant in Puerto Rico. The majority of this growth supports both the CBF and DCI technologies.
Ron Shinn, editor
CBF PROCESS AT A GLANCE
1. Resin is blended and melted through a continuous extrusion process.
2. Melted resin is extruded downward and cut into “gobs” of plastic.
3. The gobs of plastic are deposited into a compression cavity.
4. The compression cavity moves upward to compress against a compression core, forming the neck features and bottle preform.
5. The compression cavity drops away and a clamshell blow cavity closes around the preform.
6. The bottle is blown to its final shape and allowed to cool. Users have the option to specify stretching the preform before blowing.
7. The neck rings open like a clamshell, and a fork transfers the molded bottle from the main turret to a leak-detection station where every bottle is immediately pressurized to ensure that there are no leaks and that the bottle is fully formed.
8. The bottles are put on an exit conveyer where they continue to cool before passing through a six-camera inspection station. The vision system inspects the overall dimensions of the bottle and the bottle seal surface for imperfections, and identifies any black specks or contamination. Any rejects are culled out in a reject chute.
9. The bottles pass through a metal detector before being conveyed outside the clean room to be boxed in an automated boxing system.
Ron Shinn | Editor
Editor Ron Shinn is a co-founder of Plastics Machinery & Manufacturing and has been covering the plastics industry for more than 35 years. He leads the editorial team, directs coverage and sets the editorial calendar. He also writes features, including the Talking Points column and On the Factory Floor, and covers recycling and sustainability for PMM and Plastics Recycling.
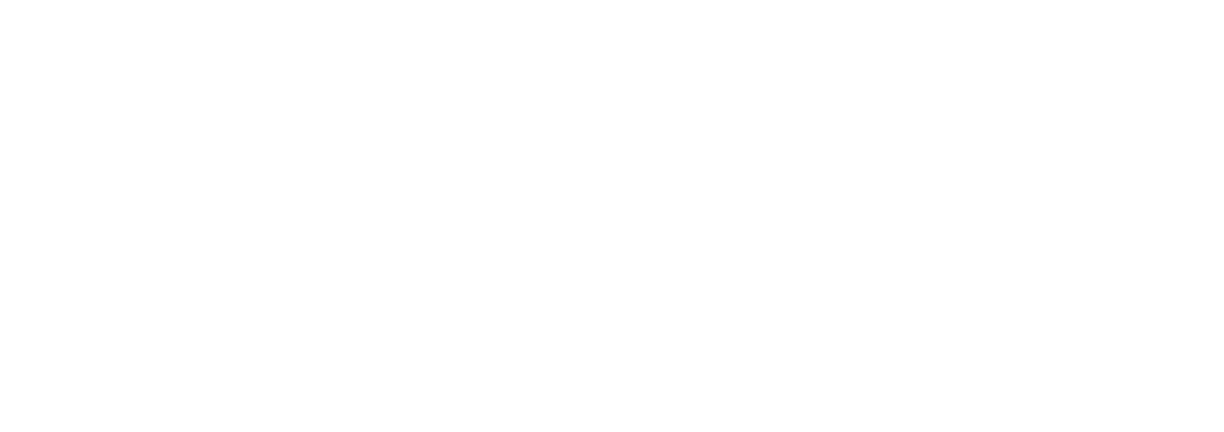