What’s new? Software upgrades to the system reflected in the release of Version 8.0. They include the addition of Precision Shot, which uses a pressure sensor in the machine nozzle to detect precisely when a check ring is seated and the polymer is compressed. Also, now as standard, the software includes a feature known as AVA, or Auto Viscosity Adjustment. Most current users of Imflux can access the upgrades with only a minor change to their existing software.
Benefits Efficiency, greater precision and better part quality. Precision Shot allows Imflux to provide a more repeatable volume of plastic to the mold, while AVA allows the system to compensate for fluctuations in melt viscosity in real time. With Imflux, users can gain insights into how to maximize throughput, quality and overall performance. The system allows processors to use lower pressures and clamping forces than would otherwise be possible.
Imflux, Hamilton, Ohio, 513-488-1017, www.imflux.com
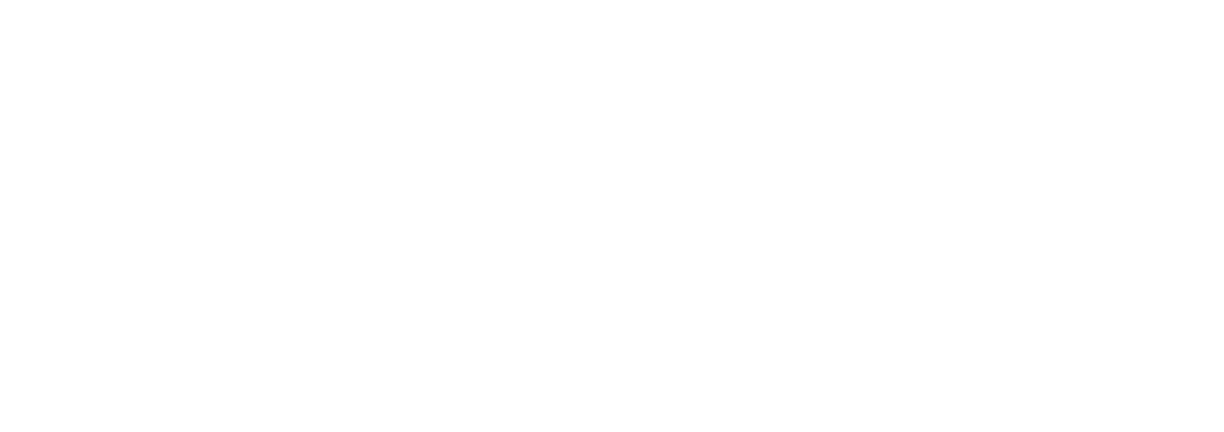