Injection molding machine suppliers launched new technologies at Fakuma in October in Friedrichshafen, Germany.
WITTMANN BATTENFELD
Wittmann Battenfeld has released a new model in the 2-year-old EcoPower Xpress series with the lowest clamping force yet.
The all-electric EcoPower Xpress 160 has 180 tons of clamping force. Wittmann Battenfeld said the high-speed, high-performance machine is especially suited for packaging applications involving high-volume, thin-wall products.
The new press was shown for the first time at Fakuma. The EcoPower Xpress series now includes five machines with clamping forces topping out at 560 tons.
EcoPower Xpress machines have Wittmann’s Unilog B8 control system, with integrated assistance systems. Press status can be monitored via smartphone.
Water-cooled servo motors drive the main movements of the press, including closing/opening, screw rotation and screw infeed. A servo- electric motor drives the mold height adjustment system of the clamping unit. A hydraulic system with servo drives powers secondary movements, including ejector, nozzle stroke/nozzle contact and core pulls.
The clamping unit is a three-platen and four-tie-bar system with a five-point toggle lever. The drive system consists of a servo motor and rack-and-pinion gears. The rigid moving platen travels on a moving carriage on the machine frame with linear guides and rotating roller bearings that do not contact the tie bars.
Distance between tie bars is 22.4 inches by 20.4 inches. Maximum daylight is 43.3 inches.
The five-point toggle lever system has an encapsulated central lubrication system that is maintenance-free. It is clean-room compatible.
The linear guides of the clamping unit and fast-response measurement of power input fluctuations in the drive motor provide a highly sensitive mold-protection system, the company said.
Standard is Wittmann Battenfeld’s kinetic energy recovery system, which converts kinetic energy released in deceleration into electric energy that is then used by the press.
A faster-response servo-electric ejector with a servo motor, combined with an encapsulated rack-and-pinion drive, is optional.
A four-tie-bar strain measurement and monitoring device with monitoring software is another option.
ARBURG
Arburg showed its Arburg Turnkey Control Module (ATCM) for the first time at Fakuma. This is a supervisory control and data acquisition (SCADA) system for monitoring and controlling processes in a complex injection molding production cell.
The company said ATCM merges component- specific data across the individual steps of the process for analysis and 100 percent part traceability.
The ATCM uses OPC-UA interfaces to collect information from the injection molding process, camera inspection and other quality-control devices and assigns it to the relevant component by a QR code. Anyone can scan the QR code on the part and see process data.
If required, the ATCM can start non-cyclical production processes such as the removal of parts for quality-control purposes.
MILACRON AND IMFLUX
Milacron introduced the Imflux low-pressure molding technology on one of its injection presses and upgraded the M-Powered suite of products with a new Imflux module.
M-Powered products, Milacron’s Industry 4.0 technology, provide users information on their current and future operations and improve productivity, quality and uptime. Milacron has added real-time adaptive process controls to the M-Powered modules.
M-Powered products are subscription- based and include remote monitoring capability.
The Imflux molding technology, developed by Procter & Gamble Co. about five years ago, provides real-time adjustment for mold and material changes.
Imflux technology allows the mold to be filled at a lower, defined melt-pressure profile. This permits a variable filling rate that adapts automatically to the part geometry.
At Fakuma, Milacron integrated the Imflux process into an all-electric EVO 155 injection press with Imflux’s proprietary process-control software and pressure sensors inside the mold and nozzle. Milacron is the first machinery maker to integrate Imflux, which eliminates the need for a separate Imflux control screen.
Real-time adjustments coupled with the other M-Powered analytical tools are designed to improve productivity through adaptive process control. Imflux minimizes variations in processing and leverages the data it collects to make the molding process as effective as possible. P&G is in talks with other injection molding machinery suppliers to integrate its Imflux technology.
Ron Shinn, editor
Contact:
Arburg Inc., Rocky Hill, Conn., 860-667-6500, www.arburg.com
Imflux Inc., Hamilton, Ohio, 513-488-1017, www.imflux.com
Milacron LLC, Batavia, Ohio, 513-536-2000, www.milacron.com
Wittmann Battenfeld Inc., Torrington, Conn., 860-496-9603, www.wittmann-group.com
Ron Shinn | Editor
Editor Ron Shinn is a co-founder of Plastics Machinery & Manufacturing and has been covering the plastics industry for more than 35 years. He leads the editorial team, directs coverage and sets the editorial calendar. He also writes features, including the Talking Points column and On the Factory Floor, and covers recycling and sustainability for PMM and Plastics Recycling.
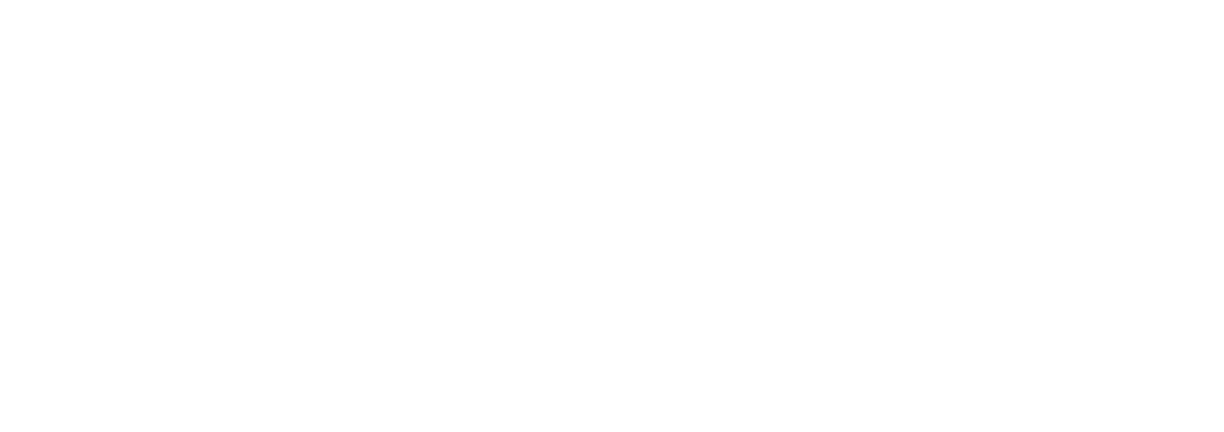