Plastics manufacturers had a message for Emerson as the company set off to define the next generation of its Branson-brand technologies: Using a welder shouldn't require a degree in ultrasonics.
A three-year project to make welders easier to use — as well as more precise and versatile — now is nearing the finish line, with Emerson about to launch the first model in a new series. The company plans to release other new technologies in the next year or two.
Overall, the company has sought to develop welders that offer better force control, increased force range, greater repeatability and improved ergonomics, said Tarick Walton, global product manager of ultrasonics for assembly technologies. He found an analogy in an unlikely source: the popcorn button on a microwave. If only welding could be so straightforward.
"We really had to go back to the physics of ultrasonics," he said in an interview touting the benchtop Branson GSX-E1 welder, which will debut late next month as the inaugural model in the Elite Precision welder series.
The first model in a planned GSX platform of benchtop welders, the GSX-E1 will include advanced features that will be standard in the Elite Precision series.
With a smaller actuator and power supply than similar Branson models, the Branson GSX-E has been designed to provide a gentle touch when used in applications involving sensitive parts.
"The GSX-E1 will have a broad force range that is essential for very delicate parts within the medical and electronics industry," Walton said.
As parts continue to get smaller and thinner, processors must be ever-more mindful of their workpieces' fragility. "If a part is overwelded, it negatively affects the functionality of that part," Walton said. "It can be broken more easily."
He said Emerson, which worked with about 400 processors in preparing its new technologies, has "leapfrogged" existing technologies by restraining its welder's forces to offer a just-powerful-enough option.
The Branson GSX-E1 will provide users with flexiblity, with top forces that Walton said exceed 1,500 newtons and minimum forces he calls the industry's lowest.
Exact specifications for the Branson GSX-E1, which was still undergoing testing, will be available next month.
Besides producing quality welds, Walton predicts the Branson GSX-E1 will be able to achieve faster cycle times and greater throughputs.
Unlike welders driven by pneumatics, which can experience slight variances in positioning over time, the Elite Precision series welders will have an advanced electro-mechanical actuation system, so all units will be able to replicate perfectly the same motion every time they perform a task. According to Walton, they will be capable of better than 99 percent repeatable accuracy.
Welders in the series also will boast a quick-change system that reduces the time of job changeouts from more than an hour to less than 5 minutes. For faster setups, they also will have a smart stack — an easy-to-use preconfigured acoustic tool consisting primarily of a converter and QR-code reader with tolerances that can be set to a specific, repeatable amplitude.
To make the Elite Precision series more user-friendly than existing technologies, Emerson also is launching new software. For example, a multimode module will be standard. It will allow users to combine multiple weld modes, such as weld-by-time and weld-by-energy during a single mode; this approach will provide a more dynamic way to weld complex parts.
The software upgrades also include better traceability for medical parts projects.
Karen Hanna, copy editor
Contact:
Branson Ultrasonics Corp. Danbury, Conn., 800-732-9262,
Karen Hanna | Senior Staff Reporter
Senior Staff Reporter Karen Hanna covers injection molding, molds and tooling, processors, workforce and other topics, and writes features including In Other Words and Problem Solved for Plastics Machinery & Manufacturing, Plastics Recycling and The Journal of Blow Molding. She has more than 15 years of experience in daily and magazine journalism.
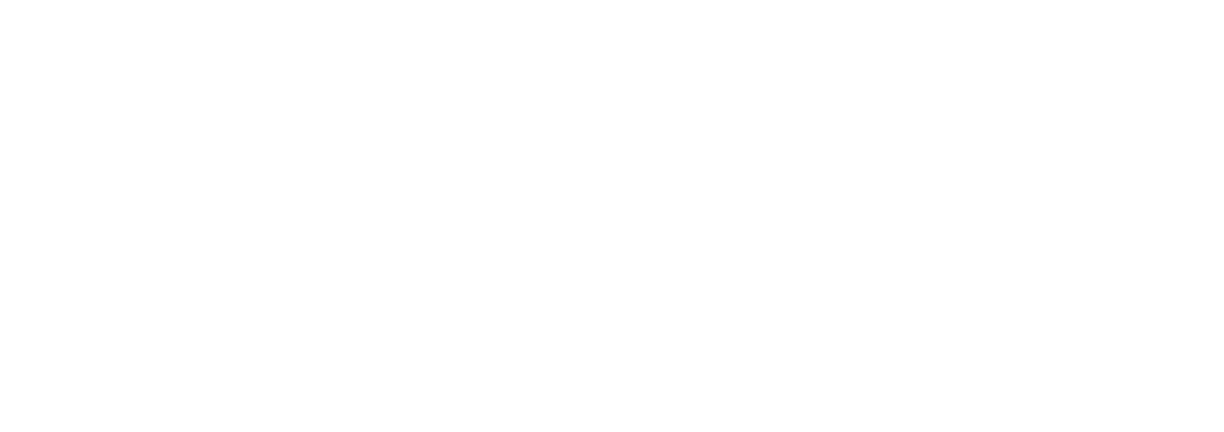