
"If you are a molecule, what do you feel? You don't know the machine controls, you just feel the temperature, pressure, flow and cooling," said Don Paulson, chairman of Paulson Training Programs. Looking at injection molding from this perspective enables molders to use the basic properties of plastics to answer the "Why" of molding problems and correct them. Paulson, a pioneer of scientific molding, calls it "molding from the plastic's point of view."Paulson discussed his career with PMM correspondent Lisa Jo Lupo.
JUST THE FACTS:
WHO IS HE: Don Paulson, chairman of Paulson Training Programs Inc.HEADQUARTERS: Chester, Conn.FOUNDED: 1978EMPLOYEES: 15, plus consultantsYEARS IN THE INDUSTRY: 57
How did you get into the plastics industry?
Paulson: I graduated from the University of Minnesota in 1955 with an engineering degree. I'd had nothing in my curriculum about plastics, but in one of the labs there was a compression press in which shot glasses were being made out of polystyrene beads. For me, it was fascinating that you could take something like this — beads, something I wasn't even familiar with — and make parts. That really was the genesis of my becoming interested.After graduation, I went into the Navy and was on a destroyer for three years, then got an assignment to teach engineering in the Illinois University ROTC program. It was there I decided to devote my career to plastics. When I got out of the Navy, I got a job at Dow Chemical because they had a nine-month training program just for plastics. I stayed at Dow for two years, then took a job at General Motors setting up training for its General Motors Institute (GMI) work-study program for junior and senior engineering students. When you teach engineering students, they've taken all their math and physics, so they'll ask very difficult questions, like "Why?" But in molding, there almost was no "why." If there was a part defect, you twisted knobs until you solved the problem.
This is what led you to take a scientific approach? What does it mean to treat injection molding as a science?Paulson: Yes. To try to answer the students' questions, I went back and started looking at why plastics do what they do. I decided I had to know what happened inside my lab's molding machine and inside the mold. One day, the engineering vice president came by and I was explaining how complicated injection molding is — that there are 17 variables on the molding machine. He responded, "I've never seen a process with more than four basic variables. Look for the four." That really set me thinking. I went back to the physical laws. What are the physical laws that apply to plastic? In the simplest form, plastics are heated, they're made to flow, they're put under pressure in molds and they are cooled: four steps.Over a period of several years, I was able to measure those four variables in the machine and in the mold and compare the molded part properties to both the machine conditions and the plastic conditions that resulted in those properties. The machine conditions were all over the place. But if you looked at melt temperature alone, there was an excellent correlation with part properties — if you looked at fill rate or cavity pressure or cooling alone, same thing. All the part properties that I could measure were determined by one or more of those four variables. I had just defined scientific molding.
You then co-founded Control Process Inc. with Rod Groleau, where you developed closed-loop, injection molding process control and plant-monitoring systems. Tell us about that.Paulson: At GMI there was a fifth-year project, in which students do extensive research. Rod was my student and did his on the four variables. He tied it all together and showed that, yes, you really can know why molded parts vary, and it's not the machine that does it, it's the plastic behavior when it's being molded. After he graduated and went on to get his master's, we got together again and said this information is so good, let's start a company. That was Control Process Inc. — CPI.
One of our customers was Polaroid. They couldn't mold the lenses for their cameras properly. So instead of trying to use the machine to control cavity pressure, we used the pressure in the mold to control the machine. Now you get perfect lenses. Several companies had similar problems, so our business at Control Process was precision molding. Monitoring, which is an outgrowth of CPI, lets the manager see at his desk what each machine is doing, how well it is performing.
Why did you decide to sell CPI and found Paulson Training?Paulson: We were both tired of it. The exciting part for us was the invention and the excitement about learning new things. Once it gets to be a business, it gets boring; that's the way it is, I think, with inventor-type people. But the application of what I learned about making injection molding a science has been a fascination for me. It's fun to teach people; it's fun to see the eyes light up when they say, "Oh, that's why." At Paulson Training, we've had numerous times that people would write us letters saying, "You've changed my life."
How does this make people see injection molding in a new way?Paulson: The new way is looking at molding not from the machine point of view, but from the molded part point of view. If you have a problem, it's not caused by the machine — not directly — it's caused by the behavior of the parts being made: the pressure, the temperature, the flow or the cooling. So, don't forget the machine, but realize the machine's only function is to produce for you the proper four basic variables. Your function as a molder is to set the controls so you get those four plastic variables. When you don't know what's wrong, that's where the technology of molding comes in. With virtually any problem, if you understand what is wrong with one or more of the four variables and you understand the machine, you know what machine control to go to. There's more to molding than just the science, but you need to look at the process from the plastic's point of view.
What is the most important problem the injection molding industry faces today?Paulson: There is an insufficient number of skilled personnel. And there should be, because traditionally they came from years and decades of on-the-floor experience, but no highly evolved technology continues to depend on experience. Old timers explain molding as, "Well, when I had this problem, I twisted this knob; when I had that problem, I twisted that knob."That's what experience does, but you can't train people that way. There's been a lack of good education, so there is a lack of personnel who understand molding is a science and therefore cannot effectively use the modern molding machine's capabilities. But we are in a phase now to turn injection molding from an art to a science.
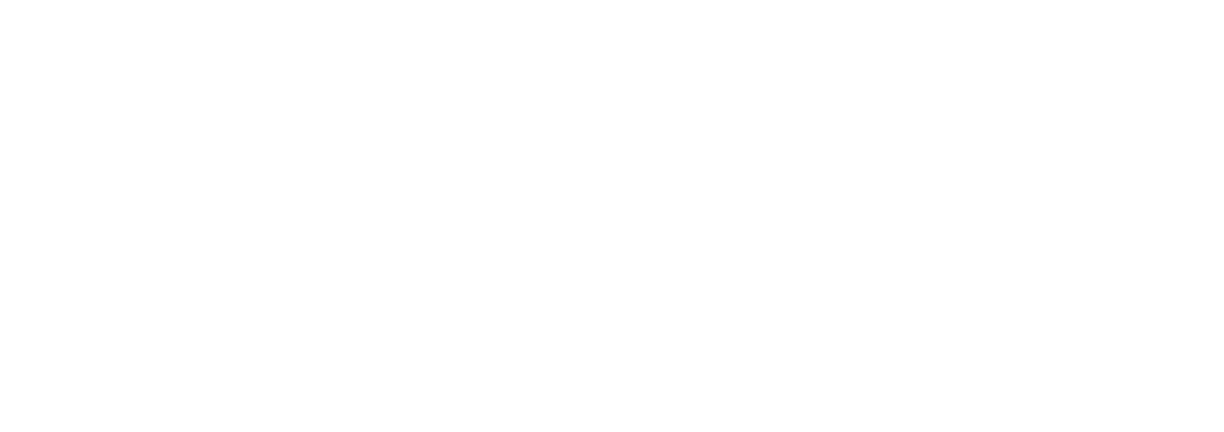