HyCAP4 Husky has launched the next generation of its HyCAP platform for molding beverage closures. The fully integrated injection molding system is especially suited for high-volume manufacturing of lightweight, one-piece closures.
What's new? New capabilities for machine and mold integration, intelligent features and simplified controls. Husky's Polaris HMI has a 19-inch color display and a more intuitive layout for easier navigation. New features include an inline metal separator and an injection nozzle filter to capture contaminants. Energy savings are made through improvements such as electrification of the clamp motion, servo-variable pumping technology and a regenerative clamp stroke. A new part-eject assist feature provides consistent free fall of closures at fast cycles. Sensor-driven mold alignment and use of Husky's patented intelligent Mold ID technology have been added.
Benefits Simplified controls, economical operation and energy consumption that is 40 percent lower than the previous version. The controls provide quicker access to data and process parameters, faster process set-up and improved repeatability. Capturing contaminants helps minimize unplanned downtime. Improvements in part ejection makes faster cycle times possible. Also, mold wear is reduced by the use of sensors.
Hall 13/A61, Husky Injection Molding Systems Ltd., Bolton, Ontario, 905-951-5000, www.husky.ca
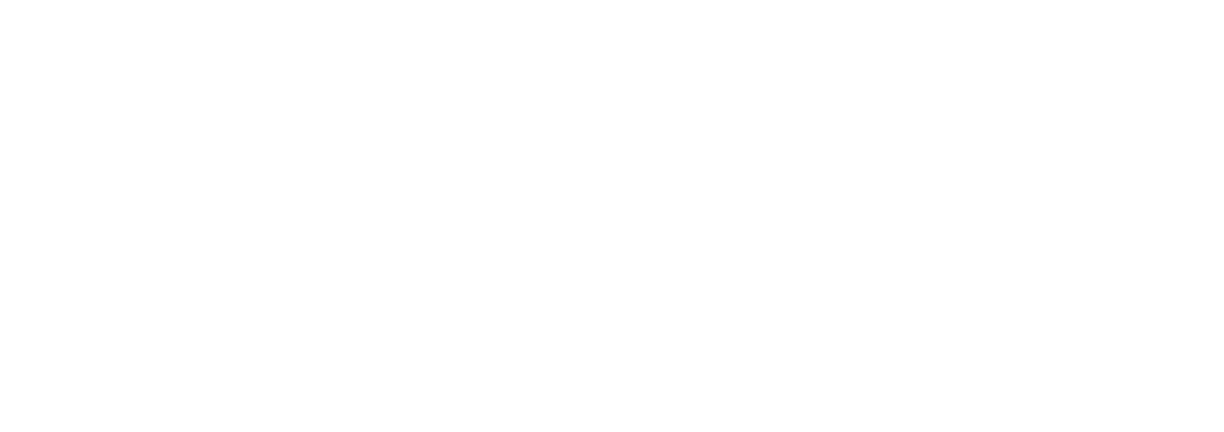