By Ron Shinn
Digital programs to make processing machinery easier to operate — and in most cases significantly reducing the need for human operators — are hot selling points.
They are arriving just in the nick of time.
The latest example comes from KraussMaffei, which has expanded its smartMachine digital portfolio with smartOperation, a feature that enables operators without deep technical knowledge to run the machine with just a green and a red button.
This latest function joins KraussMaffei’s APCplus and dataXplorer programs. The company said its molding machines equipped with these functions can analyze the process and automatically make adjustments in real time to optimize the process. The results are greater process stability, reduced downtime and increased production efficiency.
Digitization of plastics processing equipment has been driven by several factors, especially labor shortages and the need to be more competitive. Being more competitive means being more efficient on the plant floor.
Manufacturers everywhere are having trouble finding and retaining skilled machine operators. Reducing the need for operators with technical knowledge — once the backbone of processing operations — is a worthwhile goal.
Can processors eliminate human operators? My first answer is “no,” but my second answer is “maybe.” Every time I visit a plant that has a lights-out operation, I marvel at its efficiency and in many cases the simplicity of the operation.
I am coming to the realization that lights-out, or at least lights-dimmed processing, is easier to achieve than ever. It takes manufacturing leaders having the right mindset to purchase the optimal machinery and automation products and then design work cells to fully utilize the capabilities of the equipment.
Gary Fortier, then director of U.S. molding operations at Wisconsin injection molder Evco Plastics, told me during a 2019 plant visit that the company looks at every new project as a potential lights-out operation and fully plots out the entire process. “We think about what we have to do from a design standpoint upfront so we can run lights-out. We need to incorporate that at the beginning.”
KraussMaffei is not the only machinery manufacturer making significant improvements in its digital products. Here is a sampling.
Engel has a suite of products named iQ Weight Control, iQ Flow Control and TIG, its own Manufacturing Execution System. Together, Engel said its digital products facilitate part design, mold sampling, production and service and maintenance of injection molding machines.
Arburg’s digital products and services are part of the arburgXworld (aXw) portal. They include the Gestica control system for adaptive process control and regulation. The aXw Control ReferencePilot sets parameters directly in the current cycle and detects and compensates for process fluctuations.
Arburg also has optimization and processing support programs called 4.set-up, 4.start-stop, 4.production and 4.monitoring.
Wittmann labels its process execution products HiQ Melt, HiQ Flow, HiQ Cushion, HiQ Metering and HiQ-Packing. HiQ Flow, for example, compensates for temperature and batch fluctuations. During the injection phase, it determines the viscosity value and the machine calculates how to compensate, if needed, to keep the part weight consistent.
Milacron introduced M-Powered eight years ago. It is a portfolio of observational, analytical and support services that monitors molding machine performance and alerts the operator to current issues and potential issues that might arise in the future.
Gee-whiz technical functions also are available for processes other than injection molding. At the K Show in 2022, Windmöller & Hölscher (W&H) demonstrated a remarkable new HMI-based assistant for its blown film machines that guides operators through complex start-up and product changeover procedures. The program is called Easy2 Change and grew out of efforts to reduce resin waste.
First, W&H technicians built a program to speed up and foolproof the system, based on completing steps and meeting specific parameters in the correct order. Then, they developed a new air-ring and bubble-inspection system that makes it easy for the operator to see on the control panel when the bubble shape and frostline are correct. This was previously a manual procedure.
I expect we are just now at the beginning of the digitization of processing equipment. There are going to be plenty more advances as we become more comfortable using artificial intelligence.
But all the research and development machinery manufacturers put into their products does not count for much if processors go about their business in the same old ways.
A very successful processor told me recently that his company is probably using one-tenth of the capabilities of its injection molding machines. There are two ways to interpret that comment — either the company should be buying less expensive machines, or it is not trying hard enough to improve efficiency and increase profits.
Ron Shinn, editor
Ron Shinn | Editor
Editor Ron Shinn is a co-founder of Plastics Machinery & Manufacturing and has been covering the plastics industry for more than 35 years. He leads the editorial team, directs coverage and sets the editorial calendar. He also writes features, including the Talking Points column and On the Factory Floor, and covers recycling and sustainability for PMM and Plastics Recycling.
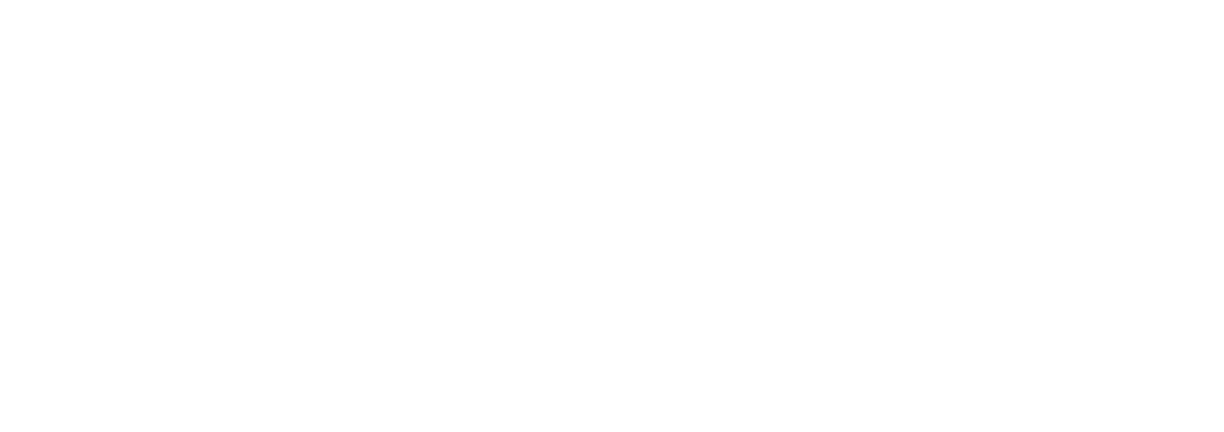