Can you operate your plant lights-out?
Robots are creating their own at Fanuc, but in the world of plastics processing, the process that is best suited for lights-out manufacturing is injection molding, because of its high volumes, repeatability and suitability for automation. More-labor-intensive processes, such as thermoforming or rotomolding, would encounter bigger challenges in going lights-out.
At the injection molding factories that I have visited, two key themes emerge in the push for productivity: Companies are working on building fully automated cells and standardizing primary machinery and peripheral equipment. It just so happens that the journey to lights-out production requires these same building blocks. This foundation is buttressed by technology, notably the advances in Industry 4.0, remote monitoring and predictive maintenance.
At Makuta Technics in Shelbyville, Ind., which has operated lights-out for 22 years, 22 injection molding cells operate 24/7, making millions of parts every month. The parts are tiny — up to six fit on the face of a penny. These components have various medical, pharmaceutical, microfluidics, electronics/office automation and automotive uses.
Precision and shot-to-shot accuracy are paramount. Two of the factory’s newest cells were built for two-shot medical micromolding. The cells employ Sumitomo all-electric molding machines, designed with dual injection units and a high-speed, very accurate rotating plate. The two-shot medical microvalve comprises a PP body from the first shot and a soft, TPE overmolded tip produced in the second shot.
According to Makuta, when the mold opens, one arm of a Star Automation robot removes four overmolded parts — the robot’s other arm removes the runners. The right arm discards the runners, and the left arm holds the molded parts in a queue until a six-axis Fanuc robot takes them for final inspection.
Makuta also uses Yushin robots. Chris Parrillo, national sales manager with Yushin, said that its robots can email or text message error alerts. “A robot can take a molding machine and itself out of automatic mode and shut everything down,” he said. Yushin’s robots can be equipped with visual inspection systems that detect such problems as excess flash on parting lines or short shots, by comparing the programmed data of a good part to the part being handled.
The machinery and equipment create the parts and must run seamlessly, but that is not the most important piece of the puzzle, company President Stu Kaplan said. “Everybody thinks they can go buy the toys and do this,” he said. “What most people miss is that the culture has to be established. Everything has to be done the same way, every shot.”
Despite the perception that automation can completely replace humans, investment in people has been key for Makuta, whose human workers, known as Makutians, inspect parts every two hours when they are at the factory. Overnight, everyone can be alerted to issues by telephone.
Andrew Rajkovich is the owner of Ponderosa Plastics Equipment, a Layton, Utah, independent manufacturers’ rep for a range of equipment for the plastics industry. He is seeing a trend toward lights-out because it allows companies to address worker shortages and gives them the flexibility to redeploy personnel.
“Instead of someone counting parts all day, we can put a robot with cavity separation with a cycle count built into the program, and that frees up the manpower for another job. A lot more people want to run overnight and just roll over and look at their phone to make sure they’re still making good parts. We do a lot of long-term projects to get customers to that point.
The owner of a third company, an injection molder that makes gears, reported that the demands of the parts inspection process have prevented it from going lights-out. “We have not been able to measure our molded gears with vision systems, thus requiring mechanical inspection,” the owner said. “Staffed shifts measure gears every two to three hours to ensure capability. We can mold lights-out but then risk having issues with large quantities of gears.”
The key for this company would be the ability to correlate process parameters to gear quality and eliminate inspection, or to include inspection systems in each molding cell that is operated by collaborative or six-axis robots, he said.
“We believe in the future that lights-out manufacturing will be mandatory, especially on second and third shifts, due to the inability to staff off-shifts with technical people,” the owner said.
Is your factory evolving toward lights-out? We would like to hear from you at [email protected]
Angie DeRosa, managing editor
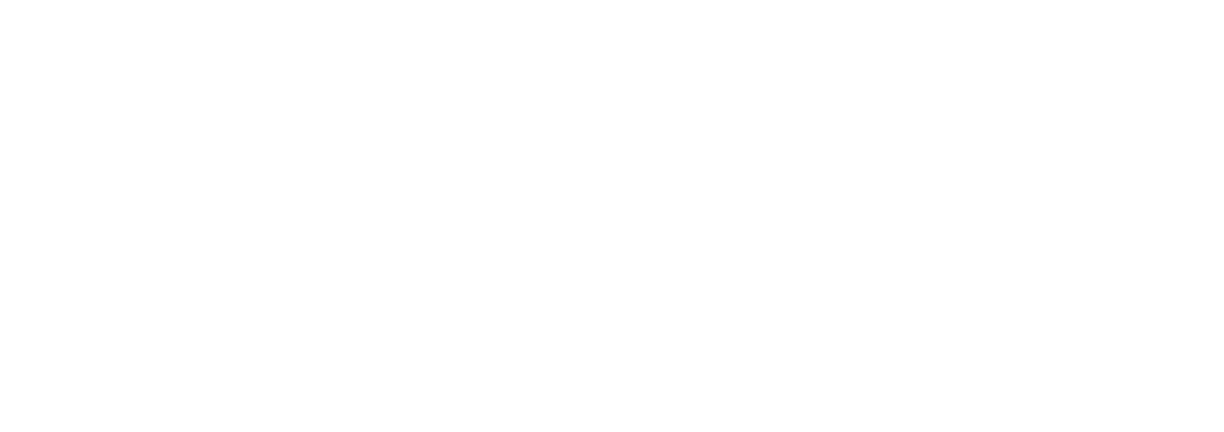