By Ron Shinn
I have to admit that 10 years ago, I was quite skeptical when Arburg GmbH unveiled its Freeformer 3D printing system.
This was one of the leading injection molding machine manufacturers in the world moving into a nascent technology at the time dominated by small startups. Sales of industrial 3D printing machines in the plastics industry were very low and there were no obvious signs that was going to change anytime soon.
Why didn’t Arburg spend its new product development money on bigger, faster, better injection molding machines instead of this diversion into an unknown market?
Today you could say that the 100-year-old Arburg recognized a new opportunity well ahead of other legacy machinery makers.
I admit it: I was wrong to be skeptical.
Arburg, based in Lossburg, Germany, in the Black Forest, is now the clear leader among injection molding machinery makers that offer 3D printing systems. KraussMaffei Group debuted two 3D printers with much fanfare at K2022 last October. Michael Ruf, then CEO of KraussMaffei Group, told me that he believed additive manufacturing (AM) equipment would play a big role in his company’s future.
That could be true, but Arburg has a 10-year head start. It sells the Arburg Plastic Freeforming (APF) system in three different sizes and 3D printers from innovatiQ for processing liquid silicones and filaments. InnovatiQ, originally known as German RepRap, was purchased in 2020 by the two families who own Arburg.
It would be interesting to know how Arburg decided to jump into the AM market. The third-generation owners — Juliane Hehl, Renate Keinath and Michael Hehl — certainly brought a younger outlook to the company when they took over in 2005.
It also could be that they believed that plastics processors should make 3D printed parts alongside their traditional process instead of watching those opportunities go out the door to non-plastics companies.
Arburg’s APF has a lot of appeal to plastics processors. It is from a stable company they know, it uses plastic pellets they are familiar with, controls are intuitive and the machinery manufacturer has developed a full array of AM support services.
We write periodically about how AM is moving closer to long-run plastic part production, once considered the exclusive domain of traditional injection molding and extrusion. Our cover story this month takes another look at the trend and finds that the industry is not yet to the point of scrapping injection molding machines and buying 3D printers, but more and more plastics processors could find opportunities for AM alongside their traditional process.
Senior Staff Reporter Karen Hanna quotes Tali Rosman (Page 4), an AM expert who advises early-stage companies on strategy, product roadmap and corporate development, saying the evolution of 3D printing is a potential threat to injection molders — if they don’t identify how to use it to complement what they’re already doing.
Another 3D printing expert, Brent Stucker, said a hybrid approach already is becoming commonplace.
“We’ve come a long way. I would say, for people who make physical products, it’s very rare if they don’t use additive manufacturing, or 3D printing somewhere in their ecosystem, either to prototype something, or actually as a production operation,” said Stucker, who in May started his own firm, 3DX Consulting.
AIM3D, a printer maker based in Germany, is working to scale up to produce 30,000 automotive parts as part of a collaboration with German companies ZF Friedrichshafen AG and Schaeffler Technologies AG, in Herzogenaurach.
Are we at a turning point where most plastics processors will rely on AM? The stories in this month’s issue will help you decide. But if a company can make 30,000 parts economically with 3D printing, can 100,000 parts be a reachable goal?
We have definitely come a long way since Arburg introduced its first industrial 3D system.
I recall visiting a plastics processor a few years ago and expressing surprise when I saw a 3D printing machine in the front office next to a photocopier. The owner of the company said the only person using the machine was his 16-year-old son who came in on weekends to play with it.
If the North American plastics industry has not yet reached that turning point, we are certainly getting closer to it. There are now hundreds of 3D printer manufacturers offering different build technologies, maximum part sizes, part quality and cost points. There is something for just about everyone to consider.
Ron Shinn, editor
Ron Shinn | Editor
Editor Ron Shinn is a co-founder of Plastics Machinery & Manufacturing and has been covering the plastics industry for more than 35 years. He leads the editorial team, directs coverage and sets the editorial calendar. He also writes features, including the Talking Points column and On the Factory Floor, and covers recycling and sustainability for PMM and Plastics Recycling.
Related
High-tech skills come at high price
So, you need a new ERP. Now what?
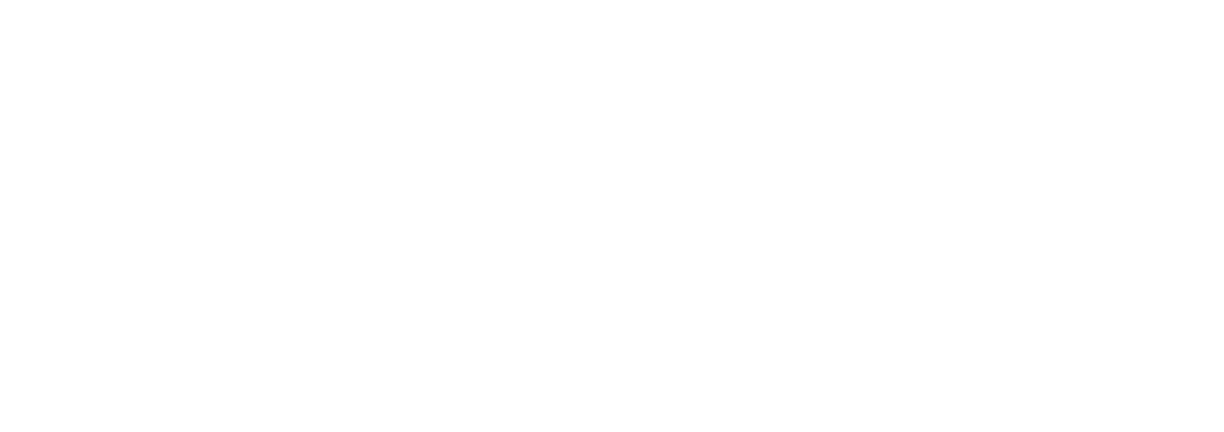