Harbec, a manufacturer of precision components for aerospace, medical and high-end industrial applications, has been generating its own electricity, heat and air conditioning for 19 years.
The company, which provides additive manufacturing, machining and injection molding services, in 2001 began its green-energy journey with the construction of a combined cooling, heat and power (CCHP) system. In subsequent years, company owner Bob Bechtold was so impressed with the results that he expanded the system to serve the entire facility and added two wind turbines. He now plans to install a solar array on an upcoming plant addition.
Related stories: Tracking energy use lets processors take charge; Pinpointing energy-guzzlers is key to saving money; Solar, battery storage bring savings to Iowa blow molder
He said that his green energy projects are based on sound business decisions and “end up becoming a very significant savings for us.”
Over the years, the company has saved hundreds of thousands of dollars.
The company originally saw the CCHPsystem as an affordable approach to air-conditioning. At the time, the plant had 20 to 30 injection molding machines turning out a variety of parts made with engineering resins. The company had difficulty keeping hygroscopic resin dry and was consuming large amounts of energy running as many as 25 desiccant dryers 24 hours per day.
“I was trying to find a way to air-condition our injection molding plant, mostly for the sake of our employees,” Bechtold said. “But, secondarily, because the type of molding that we do is with very high-tech engineering resins … we were having a terrible time keeping our materials dry enough.”
Running off natural gas, the CCHP system essentially provided free air-conditioning, Bechtold said. The gas powers a turbine for electricity generation and the exhaust heat is used in two ways. It can produce hot water for radiant floor heating throughout the plant, or it can be transported to an absorption chiller to chill water and air.
“The air-conditioning system takes heat energy that normally would be wasted and turns it into cold, and now we’re air-conditioning the facility,” Bechtold said.
This also lowers the humidity in the building, which has significantly reduced the need for desiccant dryers. Today, the factory is larger than it was in 2001, and, “if we’re running five desiccant dryers, it’s a lot,” Bechtold said. Using fewer dryers also reduces the heat that escapes from the dryers into the plant.
About five years ago, the company landed a grant from the New York State Energy Research and Development Authority to pay part of the $1.9 million cost of doubling the CCHP system’s thermal capacity.
Harbec, which had 10 microturbines, added eight new 65-kilowatt (kW) microturbines fueled with compressed natural gas (CNG). The new microturbines have a total rated capacity of 520 kW, bringing the system’s maximum potential rated capacity to 820 kW. The upgraded system brings heat and air-conditioning to an additional 14,000 square feet of the facility, including a machine shop and offices.
As part of the project, the company removed 10 old electric air-conditioning units and six CNG furnaces.
Harbec’s CCHP system uses about 80 percent of the energy it generates and wastes about 20 percent. That performance is better than that of many typical electric plants, which lose a lot of energy in the form of heat.
Installing the system wasn’t cheap, but it paid off, Bechtold said. The return on investment (ROI) for the original system was less than seven years.
He said he frequently hears from people who reject green-energy projects because they say the payback takes too long.
“I always feel sorry for them because they are only shorting themselves,” he said. “The fact is, they’re going to pay every bit of that money that they say they can’t pay, but they’re just going to give it to somebody else — the electric utility or the gas company.”
Harbec borrowed money to fund the energy projects, then repaid the loan from the savings on its utility bills.
In 2002, a little more than one year after the initial installation of the CCHP system, Harbec installed its first wind turbine, which could generate 250 kW of electricity.
“After it paid for itself in less than eight years, I still needed a ton more energy for running the plant,” Bechtold said. “I started immediately working on No. 2.”
The second wind turbine, installed toward the end of 2012, generates 850 kW, and payback was about six years, he said. The ROI was quicker in part because of the availability of grants, he said.
Harbec is replacing its original wind turbine with a rebuilt model. Bechtold said maintenance problems contributed to the turbine’s failure. He said he believes the original turbine would still be working today if it had been properly maintained. The loss of the turbine is costing the company about $300,000 in additional electrical consumption annually, he said.
He has been so happy with the CCHP and wind projects that he is now setting his sights on a solar system to generate 275 kW of electricity.
“We’re in the process literally of doing the pad work for another 30,000-square-foot addition, and we’re going to cover the roof of that with solar [panels],” Bechtold said. “There’s nothing like energy that comes from renewable [sources] and just keeps coming and coming and coming.”
In addition, Bechtold said he would like to find a way to use solar energy for heating. He has been exploring the technology but hasn’t found the right system yet.
Harbec gets 60 percent of its energy from the two wind turbines, and the CCHP system provides another 20 percent. Twenty percent of its energy needs come from an electric utility.
Even before launching its green-energy projects, Harbec reduced its power consumption by replacing hydraulic-electric injection molding machines with all-electric presses that require about half as much energy.
Additionally, since 2013, Harbec has been carbon neutral, Bechtold said. It buys green energy from the grid. To compensate for the CNG it uses in the plant and the diesel that powers employee vehicles, it buys carbon offsets.
The fact that Harbec is carbon-neutral allows customers who buy its parts to “take a bite” out of their own companies’ carbon footprints, Bechtold said.
Harbec also has adopted “water-neutral” practices, Bechtold said. Since 2015, it has avoided using potable water for manufacturing processes, limiting the use of potable water to drinking and handwashing. It built a 1 million-gallon retention pond outside the plant that is filled by rainwater, runoff and water collected from the buildings’ gutters for use in its manufacturing processes.
The company purchases water offsets as part of its water-neutral strategy, Bechtold said.
Founded by Bechtold in 1977, Harbec’s mission is to provide prototypes, tooling, machined components and quality injection molded parts in a sustainable manner with a social conscience, according to a company statement.
Bruce Geiselman, senior staff reporter
bgeiselman@plasticsmachinerymagazine.com
Harbec Inc., Ontario, N.Y., 888-521-4416, www.harbec.com
Bruce Geiselman | Senior Staff Reporter
Senior Staff Reporter Bruce Geiselman covers extrusion, blow molding, additive manufacturing, automation and end markets including automotive and packaging. He also writes features, including In Other Words and Problem Solved, for Plastics Machinery & Manufacturing, Plastics Recycling and The Journal of Blow Molding. He has extensive experience in daily and magazine journalism.
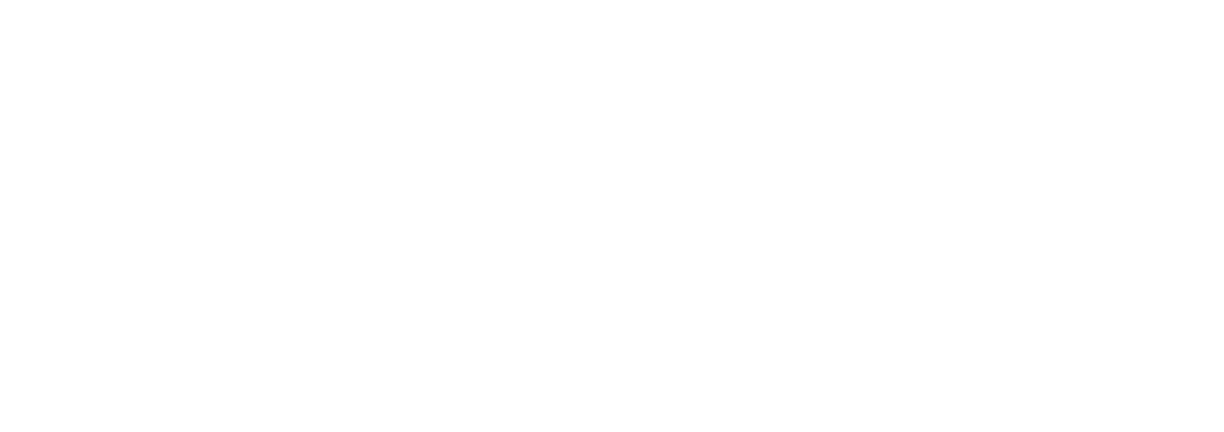