New Davis-Standard roll stand improves automation and process control
By Bruce Geiselman
Davis-Standard’s new XP Express-AGT roll stand offers more automation and enhanced process control for sheet with nominal thicknesses ranging from 8 mils to 60 mils.
AGT stands for “active gravity touch.”
The roll stand’s inverted J-stack, multi-roll design offers processors technical and bottom-line advantages, the company said. The design allows for improved die-nip management and handling, efficient web cooling and conditioning, precision control of the roll drive and high-performance web-path options, according to the company. In addition, the XP Express-AGT improves the handling of resins with low melt strength by using the angles of the die and roll to prevent sagging between the die slot and the nip. This expands the ability for processing thin-gauge sheet.
“The XP Express-AGT is our most versatile and operator-friendly roll stand model yet,” said Steve DeAngelis, VP of sheet and foam. “It builds upon the sustained success of our existing product line to offer more automation and roll control along with smarter ergonomics and a space-saving footprint. This design is also engineered for both sheet and cast extrusion to give processors flexibility to support more applications, especially in rigid and flexible packaging.”
The XP Express-AGT is available in widths from 3 feet to 6.6 feet and can handle processing rates up to 5,500 pounds per hour. Davis-Standard offers three AGT roll stand options to meet different needs for widths and processing rates. Each option has a fully automated multi-roll gap nip, individual roll-speed and temperature control, enhanced heat transfer and adaptable pull-roll design.
Its four-point Y-axis and traverse X-axis control makes adjustments easier and more intuitive for the operator, the company said.
The roll stand delivers uniform cooling on both sides of the sheet or film, double polishing capabilities, reduced web stress and consistent web orientation and thickness control, resulting in high-quality, flat sheets with desired clarity, the company said.
Bruce Geiselman, senior staff reporter
Contact
Davis-Standard LLC, Pawcatuck, Conn., 860-407-6177, www.davis-standard.com
Bruce Geiselman | Senior Staff Reporter
Senior Staff Reporter Bruce Geiselman covers extrusion, blow molding, additive manufacturing, automation and end markets including automotive and packaging. He also writes features, including In Other Words and Problem Solved, for Plastics Machinery & Manufacturing, Plastics Recycling and The Journal of Blow Molding. He has extensive experience in daily and magazine journalism.
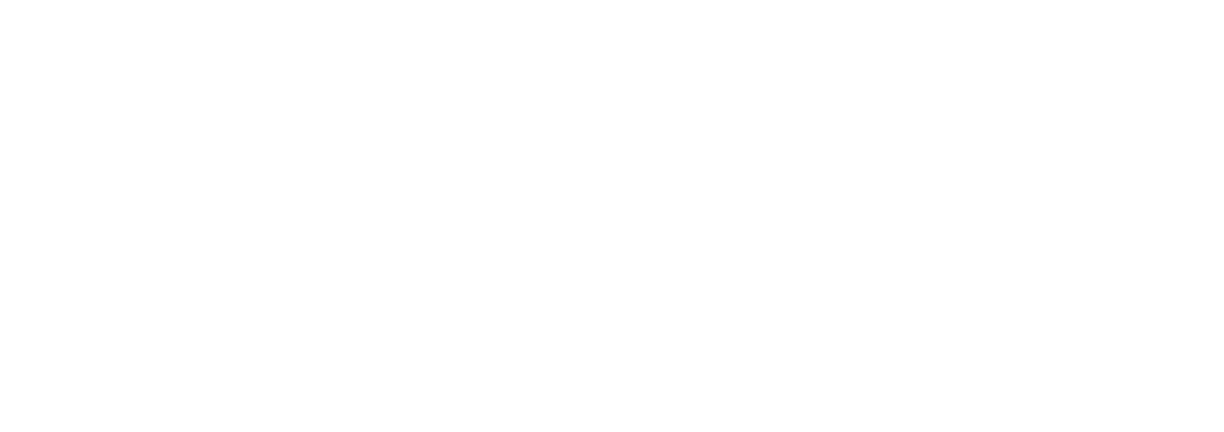