CPM’s High Output Sidefeeder improves efficiency of feeding low-bulk-density fillers
High Output Sidefeeder The CPM Group’s newest side feeder allows processors to boost the amount of low-bulk-density fillers and materials introduced into extruders. The system is available with screw diameters from 25mm to 120mm. The CPM Group’s U.S. affiliate is Century Extrusion.
What’s new? A new feeder design that applies a vacuum on a microporous filter that removes air from the powder before it is fed into the extruder. The filter prevents any blockage of the vacuum unit by powder or particles, and the filter can be manually backflushed with compressed air. To achieve maximum efficiency, the vacuum level is adjusted according to the bulk density of the material.
Benefits Improved feeding efficiency for low-bulk-density materials including talc, magnesium and silica. If a processor using a traditional feeder can introduce 10 percent to 15 percent low-bulk-density filler in a particular operation, the new High Output Sidefeeder could result in up to a 50 percent loading, said one company official who addressed the new technology at NPE.
Century Extrusion, Traverse City, Mich., 231-947-6400, www.cpmextrusiongroup.com
Bruce Geiselman | Senior Staff Reporter
Senior Staff Reporter Bruce Geiselman covers extrusion, blow molding, additive manufacturing, automation and end markets including automotive and packaging. He also writes features, including In Other Words and Problem Solved, for Plastics Machinery & Manufacturing, Plastics Recycling and The Journal of Blow Molding. He has extensive experience in daily and magazine journalism.
Guill now offers pultrusion dies
Reifenhäuser opens Bangkok office
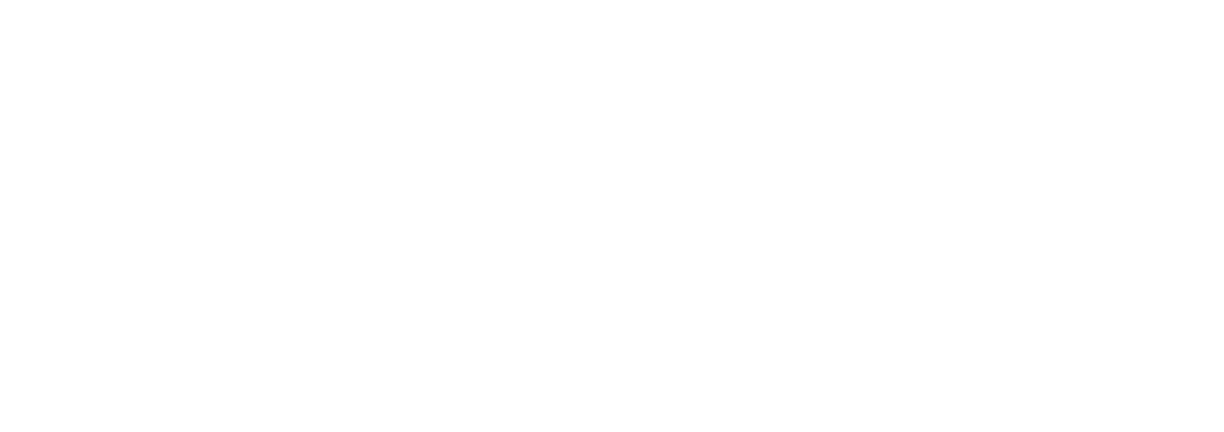