polyXtrue The polyXtrue 3-D simulation software from Plastic Flow helps users design or optimize monoextrusion or coextrusion dies. The software allows users to specify material properties and processing conditions, then run simulations to see what modifications are necessary to achieve their desired final product.
What’s new? Version 4.2. This latest update introduces a range of improvements, including a completely rewritten software module for the level-set method for simulation of plastic flow in multi-layer coextrusion dies. User experience also has been improved with a variety of updates to the interface, such as the ability to move a company's material database to a shared network drive, ensuring that all users are working with the same version of material files. A newly introduced command bar has shortcut buttons for common or useful features.
Benefits Greater accuracy. The company said the new version now can give almost the same layer structure in the final product when using either of the coextrusion simulation techniques the software employs — the level-set method or the mesh partitioning technique. The newest version also introduces an expanded material database, more than doubling the number of materials it’s able to analyze. This expanded capability also includes structural analysis parameters required for an accurate prediction of shrinkage, and parameters have been added for many previously existing materials in the database.
Plastic Flow LLC, Hancock, Mich., 906-483-0691, www.plasticflow.com
David Tillett | Associate Editor
Associate Editor David Tillett writes and edits for Plastics Machinery & Manufacturing, Plastics Recycling and The Journal of Blow Molding. He covers new products, industry news, patents and consumer and business equipment. He has more than 20 years of experience in daily newspaper, online and magazine journalism.
Guill now offers pultrusion dies
Reifenhäuser opens Bangkok office
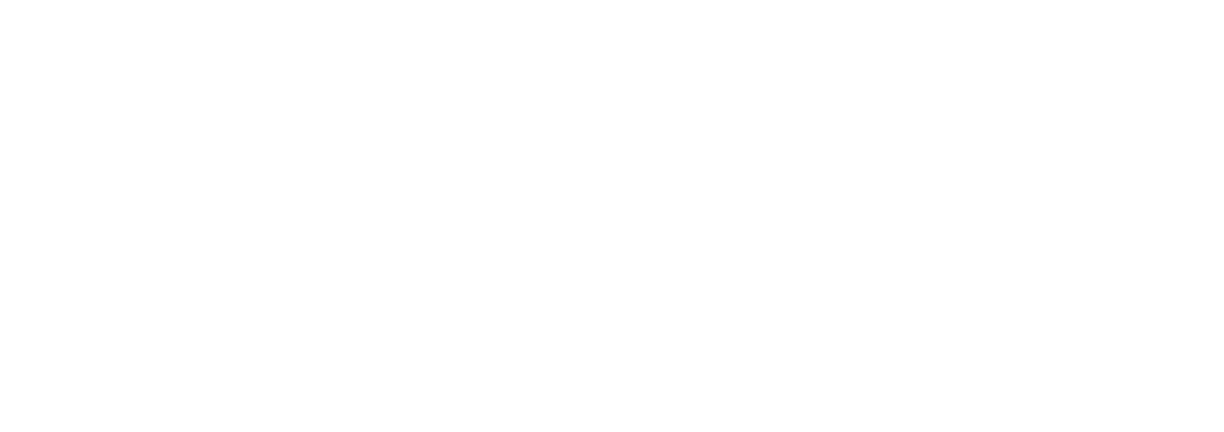