Plasticizing cylinder. It is common for extruders to employ external heating pads to aid in melting plastic pellets within the plasticizing cylinder. As the process continues and, depending on the sensitivity of the resin being used, the heat produced by the pads may not be needed in some zones of the plasticizing cylinder. In fact, the temperature may build above a desired set temperature in some zones, requiring the heat to be dissipated, commonly via radiation and convection, as well as the use of ventilation fans. However, air is a poor heat carrier, and these methods are inefficient.
Alternate approaches include plasticizing cylinders with a square cross-section, heated by heating cartridges inserted at the sides, with cooling water run through bores in the cylinder; cylinders with spiral-shaped recesses, sealed to the outside by form-fitting heating shells that allow for the flow of a liquid cooling medium; and a single tube wound through a wear insert arranged in the screw housing, which can circulate either heating or cooling liquid.
A patent application filed by inmex GmbH of Sankt Augustin, Germany, describes a novel approach to regulating temperatures in a plasticizing cylinder.
In some variations described in the application, at least two recesses run the length of the exterior of the plasticizing cylinder, forming a double spiral, with one recess housing a heating element and the other a cooling element.
Other variations have multiple zones that border each other along the length of the plasticizing cylinder, each zone containing both a heating element and a cooling element, with each zone capable of being controlled independently in a closed loop.
The recesses are of a depth that allows the heating element or the tube carrying a cooling medium to be in contact on three sides with the plasticizing cylinder. One or multiple insulation sleeves may be employed to help regulate the temperature.
According to the patent application, the method proposed is an improvement over air cooling, and improves the energy efficiency of heat management by both the heating and cooling elements.
This plasticizing cylinder would be equally useful for single- or double-screw extruders, as well as degassing extruders. The patent says that while cooling is not required for injection molding, it could be useful in some cases.
“For example, and assuming the user operates the injection molding machine with material A at a cylinder temperature of 300 [degrees Celsius], the user can desire to process material B at 200 [degrees Celsius]. … The plasticizing cylinder can be cooled while the mold is being changed over for the subsequent application, which saves time here.”
Patent application 20210078230; published March 18.
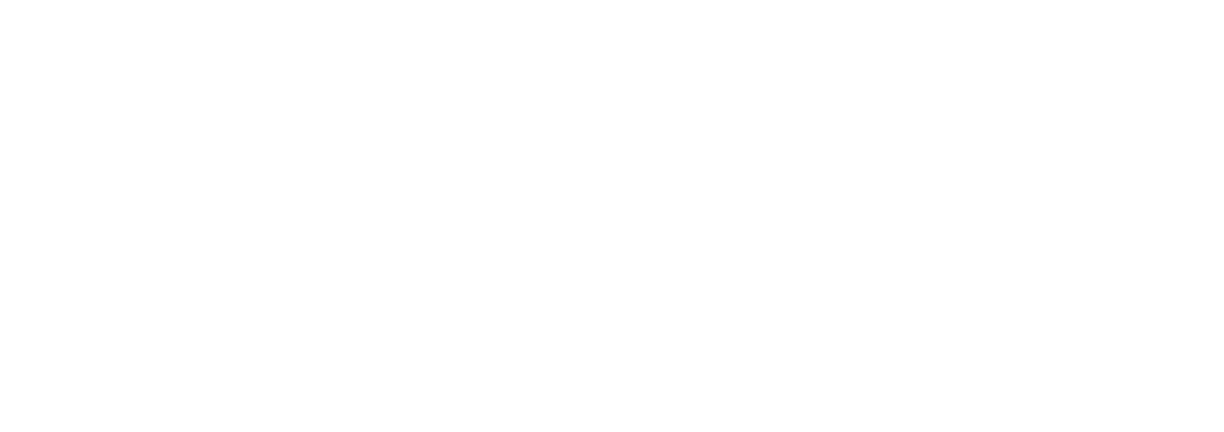