Proco Machinery launches palletizing system, revamps Robopik
By Bruce Geiselman
Proco Machinery, a Canadian manufacturer of automation systems, has launched its new collaborative robot palletizing system and its next-generation Robopik takeout system for blow molded bottles.
Both products were introduced at the NPE2024 trade show in Orlando in May.
The cobot palletizer can stack bottles up to 104 inches in height — about twice the height of standard cobot palletizers, said John McCormick, president of Proco Machinery.
“Most cobot palletizers will only pack up to 50 inches to 55 inches, but some of our customers require packing the full height,” McCormick said. “While it will still do the short stack, with an additional option, you can go up to 104 inches.”
The new palletizing system improves efficiency by also automating the palletizing of trays and tier sheets between the layers of bottles, McCormick said. That reduces the need for manual labor, which reduces manufacturing costs and boosts profitability.
The cobot palletizer’s design allows the system to be easily configured into a case packer, which permits seamless integration into existing production lines and minimizes disruptions and downtime. Combining palletizing and case packing processes into one system allows for maximization of warehouse space, McCormick said.
“It’s a very small footprint, which again is attractive to manufacturers that have a limited amount of space,” McCormick said.
The palletizer is available with cobots having a payload ranging from about 11 pounds to about 44 pounds. A cobot with a payload of about 33 pounds would be sufficient for most customers’ needs, McCormick said.
In addition, Proco launched sales of its next-generation Robopik takeout system, which uses a collaborative robot instead of the fixed automation systems found on earlier designs.
The Robopik is designed for unloading and deflashing bottles made on shuttle-type blow molding machines.
The integration of a cobot means the new Robopik system offers greater flexibility and adaptability, McCormick said. The collaborative robot delivers precision movement and advanced algorithms, enabling the new system to unload products faster and with higher accuracy compared to previous fixed automation systems. The increased efficiency results in higher productivity and lower labor costs.
The new Robopik system also includes built-in safety features including collision detection, emergency stop mechanisms and protective barriers. The enhanced safety features help users comply with regulations and reduce the risk of workplace accidents, according to the company.
The new takeout system has advanced connectivity features that allow for smart factory integration with other machines, sensors and software systems to optimize production workflows, collect real-time data for analysis and enable predictive maintenance, according to the company.
Proco Machinery Inc., Mississauga, Ontario, 905-602-6066, www.procomachinery.com
Bruce Geiselman | Senior Staff Reporter
Senior Staff Reporter Bruce Geiselman covers extrusion, blow molding, additive manufacturing, automation and end markets including automotive and packaging. He also writes features, including In Other Words and Problem Solved, for Plastics Machinery & Manufacturing, Plastics Recycling and The Journal of Blow Molding. He has extensive experience in daily and magazine journalism.
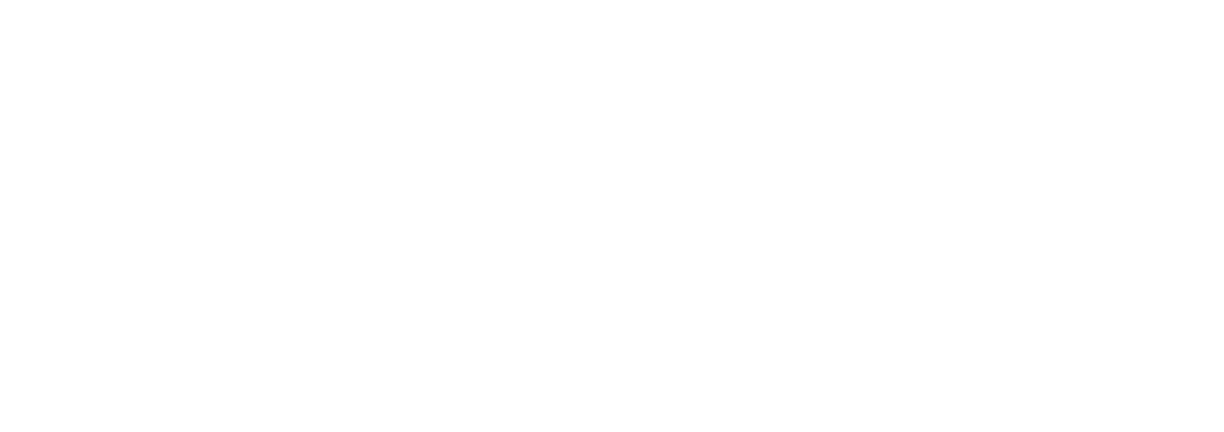