Sipa SpA, Vittorio Veneto, Italy, has patented a device that more efficiently cools injection molded bottle preforms with the goal of increasing the productivity of preform manufacturing lines. The cooling device can be used in high-speed rotary production systems making preforms from PET. In such lines, the preforms must be cooled quickly so that they can be grasped by a transfer device without risk of deformation, the patent states.
In the invention, preforms move along a helical tunnel. A manifold receives cooling air from external systems and conveys it into the helical tunnel to cool the preforms. The cooling tunnel is designed to cool the preforms faster than other systems, with the cooling speed dependent upon the flow rate of the air at the inlet and its initial temperature.
Additionally, the invention includes a chain or cable with clips for grasping the preforms and a hooking station for hooking the preforms to the clips, either in the neck zone or directly on the specific neck ring.
Patent 10,046,483; issued Aug. 14
Film calibration basket. Windmöller & Hölscher KG, Lengerich, Germany, has applied for a patent for a calibration basket that can reduce downtime in blown film manufacturing operations.
In current blown film systems, a calibration device with blowers is used to create an air cushion that guides the film between the ring nozzle of the extrusion die and the film-pulling device, according to the patent application. Sometimes, the blower elements become clogged and must be cleaned, meaning the entire blown film extrusion line must be shut down.
The invention involves a calibration basket having detachable elements. Each element can be removed for cleaning and quickly replaced with another element, minimizing downtime. In one configuration of the device, the exchange can be performed easily without tools.
Patent application 20180290364; published Oct. 11
Color feeding. Maguire Products Inc., Aston, Pa., seeks to patent a device for feeding colorant into injection molding machines. Existing color feeders operate in response to a signal from the primary machine that the feed screw is turning, according to the patent application. This means that there is a point in the process when plastic resin is fed into the machine, but colorant is not, which can cause uneven color distribution, particularly in large parts.
"A problem that has been ignored for years … relates to the amount of resin material drawn into the barrel, at the barrel throat, by forward movement of the screw during the injection step of the injection molding process," the application states. "While it seems logical and intuitive that material is drawn in only when the screw turns, this is not actually the case. It also happens that during injection, while the screw is moved forward to inject the plastic into the mold, the rear of the screw is also moving under the throat. The empty flights at the rear of the screw are now filling with material, drawing a significant additional amount of natural material into the barrel. … Operating in a way that knowingly meters one-hundred percent of the required color into only seventy-five percent of the natural material is clearly not the best way to operate."
The invention solves the problem by adding an input signal to the controls of the feeder so that colorant is metered when injection is taking place in the molding machine. The invention calculates the injection time as a percentage of screw recovery time and apportions the color or other additive accordingly.
Patent application 20180281250; published Oct. 4
Patents and patent applications can be viewed at www.uspto.gov
Have you applied for or received apatent? Contact [email protected]
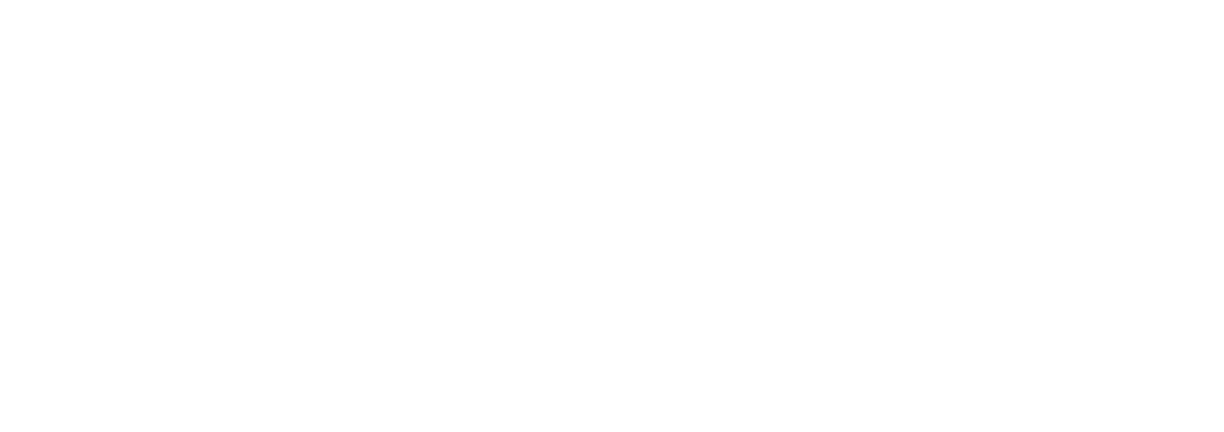