At Fakuma last month, Sepro America introduced the S5-25 Speed, a new top-entry Cartesian robot designed for fast-cycling injection molding applications. It is a faster version of the standard S5-25 model, which is one of three models in Sepro's S5 high-performance three-axis product line, said Raul Scheller, Sepro Group's managing director for North America.
The S5-25 Speed is sized for presses with 120 to 450 tons of clamping force and is designed for use in packaging applications. The vertical (Z) axis of the new model operates 50 percent faster than the standard S5-25 unit. This ensures robot in-and-out times of less than 1 second and overall molding cycle times under 4 seconds, Scheller said.
The quickness of the S5-25 Speed is made possible through the incorporation of a powerful, higher-torque motor, as well as upgraded electronics and pneumatic valves, and a lighter-weight vertical telescoping arm. "These enhancements enable the robot to execute long horizontal and vertical strokes more quickly without sacrificing precision or reliability," Scheller said.
The S5-25 Speed incorporates Sepro's Visual 2 or Visual 3 controller for programming and control. It can be configured with a horizontal stroke from 4.9 feet to 19.6 feet. It has a vertical stroke of up to 3.9 feet and a demolding stroke of up to about 2.3 feet. It handles a maximum payload, including end-of-arm-tooling, of 15.4 pounds.
GUARDING, SENSORS MAKE ROBOTS SAFER FOR WORKERS
Sepro also rolled out a system that allows humans to interact with standard linear and six-axis robots safely and efficiently.
Known as Seprobot, it combines physical guarding and sensor technology to ensure the safety of operators entering a robot work area. Most of the time, the robot operates at full speed, but, when humans enter the guarded space, laser or light-curtain sensors signal the robot to slow down or stop until the space is clear and it can return to full speed when the humans depart. A significant benefit of the Seprobot package is that it allows a conventional robot to work more like a collaborative robot, or cobot.
The design of Seprobot stems from Sepro's detailed evaluation of collaborative robot applications in the injection molding environment.
"Today, almost all robot applications in injection molding can be handled by a guarded robot operating fully independently," Scheller said. "By 2025, however, we project that fully collaborative cobots will be required in about 10 percent of applications. Further, we expect that an additional 40 percent of applications can be handled with only limited interaction between robot and human. These are the applications that Seprobot is intended for."
This means that a conventional robot — rather than a cobot — can be used, and that the robot can operate at full speed most of the time and handle heavier payloads. "Seprobot can operate two to three times faster than a typical collaborative robot," Scheller said.
The Seprobot package, which includes physical guarding and a fully integrated safety system, is available with any three-, five- or six-axis Sepro robot. Operators get safe access to feed components to the robot through an opening in the guarding. The opening is protected by proximity and motion sensors, light curtains or other safety devices that are fully integrated into Sepro's robot control.
Claude Bernard, product marketing director at Sepro, said the interest in cobots is growing, but collaboration can come at the price of productivity. "The Seprobot design is based on reducing the costs of collaboration. We start with a conventional robot, add reliable plug-and-play sensors and utilize a common guarding layout that maximizes robot speed, yet slows and stops for any needed human interaction," Bernard said.
Typical applications for Seprobot include secondary manufacturing operations like testing, assembly and packaging. The Seprobot system is not appropriate for operations where autonomous robots already excel, such as part removal and many insert-feeding and post-mold operations.
Mikell Knights, senior staff reporter
Contact:
Sepro America LLC Warrendale, Pa., 412-459-0450,
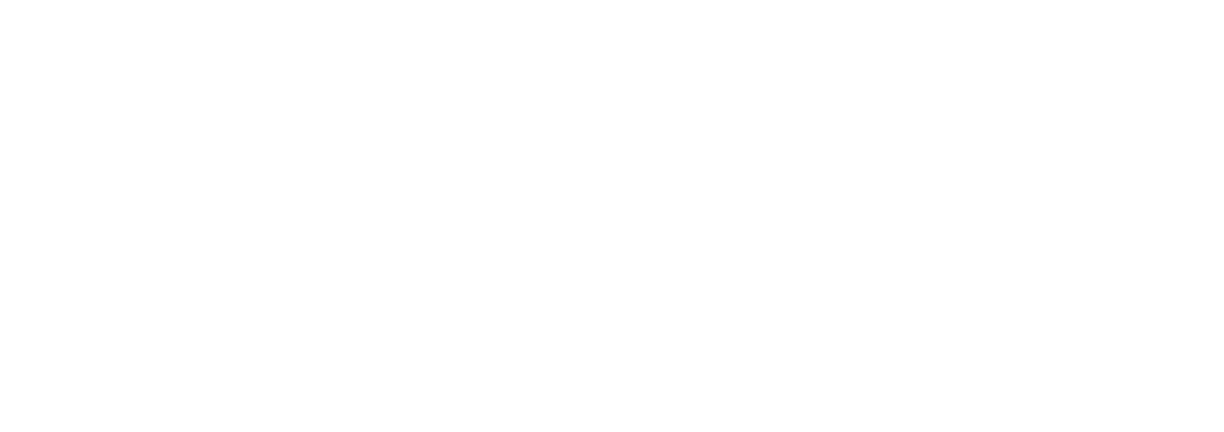