Software advances are helping bridge the communication gap between humans and robots. Recent developments include a software upgrade from Hypertherm and the announcement of a partnership between Absolute Robot and ABB Robotics that will make speaking to robots easy enough for a non-expert to handle programming.
HYPERTHERM INC.
Robotmaster V7, the newest version of Hypertherm's task-based robot programming software, is built from scratch on a new architecture.
Robotmaster V7 is designed to make robot programming easy and intuitive for manufacturing companies, even if they are first-time robot users, according to the company.
While robots come with their own programming software, their functions can be somewhat limited. There are several independent software providers, but the programming often can be time-consuming to learn. Figuring out the most efficient paths for a robot to complete a task can be a matter of trial and error. In addition, if a company has robots from different manufacturers, employees might need to learn how to work with multiple types of programming software.
Robotmaster V7 is designed to simplify and streamline programming for robots from all major manufacturers, according to Hypertherm.
For "high-mix, short-run" manufacturing, the cliché that time is money couldn't be more true, said Brian Gordon, Hypertherm representative.
"Programming a robot can be complicated," he said. "The way to make a strong return on investment for short production runs is to ensure that the entire setup is rapid and efficient."
Some robot software is highly complicated and requires extensive training, Gordon said. Many manufacturers offer only a teach pendant to program a robotic arm's movements. However, that can be a tedious process to find the most efficient arm movements to complete a designated task, he said.
"It can take two weeks to program a robot with a teach pendant, but with Robotmaster programming software, it can take less than 30 minutes," Gordon said. "That's because of highly specialized programming tools, and that the new V7 Robotmaster platform offers an integrated and stand-alone solution that incorporates CAD/CAM path creation. The robot is then automated to follow that path."
People who try to program a robot can encounter any number of motion problems; for instance, they can discover a robot arm can't reach a certain point, he said. Some problems require reprogramming the robot arm and trying again.
"With Robotmaster robotic programming software, you see all of these issues in advance, and they are simultaneously corrected for error-free programming," Gordon said. "The difference between our software and everything else is you actually have error-free programming up front without simulation, and you don't have to be an expert in programming."
Because Robotmaster V7 uses integrated CAD/CAM functionality, for the first time, Robotmaster can be used by people who aren't well versed in programming or CAD/CAM software. Just like past versions, Robotmaster V7 allows end users to leverage any CAD/CAM tools of their choice. Either way, the software offers an intuitive interface that anyone could use, with or without robotics expertise.
"Robotics and CAD/CAM expertise are not a prerequisite to create error-free robot programs with Robotmaster V7 since it is a task-based robot programming platform built around the user, for the user," said Chahe Bakmazjian, head of strategy for robotic software. "Robotmaster V7 also has unmatched flexibility and configurability and transfers the job to another robot brand or work cell, without task reprogramming. This is an industry first."
Robotmaster V7 also includes what the company calls a workspace-analysis tool that determines whether a task can be successfully executed given the part's location within a robotic cell relative to the robot's range of motion. The software performs immediate analysis and provides a visual cue to the operator who can correct problems. Simply clicking and dragging the part back into range automatically reprograms the robot.
For example, Gordon said the company worked with a yacht manufacturer that was preparing to buy a large robot costing about $1 million to trim excess fiberglass from boat hulls. However, Robotmaster V7 software determined that the robot arm would not be able reach all areas of the hull that needed trimming. Instead of making an expensive purchasing mistake, the company purchased a better alternative from the same company, Gordon said.
Robotmaster V7 software can be used in the plastics industry to program robots for tasks including trimming, cutting, dispensing and deburring. It navigates complex part geometries and optimizes motion paths while synchronizing movements and preventing collisions involving robots, parts and tooling, according to the company.
ABSOLUTE ROBOT INC. (ARI) AND ABB ROBOTICS INC.
Last month, ARI announced its robot integration services as part of a new partnership with ABB. According to Tim Lavigne, an ARI business unit manager, the partnership now enables ARI to offer customized firmware designed especially for the demands of injection molders. Molders can get the new EZ Mold Application only by purchasing six-axis ABB robots through ARI.
"We take the ABB controller and lay in our injection molding-specific software so it is much easier for the set-up and operations people in a molding shop to operate the robot," Lavigne explained.
He said the firmware upgrade allows users to program their systems even if they don't know the Rapid language ABB's robots use. As an additional benefit, the firmware offers bypass-robot and auto-backout functions. With the bypass function, users can easily opt to allow the press to run while the robot is idle — such a feature can be important during situations such as press setup. Designed to allow automatic resets after an alarm has been triggered, the auto-backout function enables a robot to retrace its movements out of the mold area and return to its home position.
A reject part function also comes standard with EZ Mold Application.
With payload capabilities ranging from 6.6 pounds to 1,102 pounds, ABB's robots can operate on all brands and sizes of injection molding machines.
Bruce Geiselman, senior staff reporter
Contact:
ABB Robotics, Auburn Hills, Mich., 248-391-8772, https://new.abb.com
Absolute Robot Inc. (ARI),
Worcester, Mass., 508-792-4305,https://absoluterobot.com
Hypertherm Inc.,
St. Laurent, Quebec, 514-225-2214 ,[email protected],www.robotmaster.com
Bruce Geiselman
Senior Staff Reporter Bruce Geiselman covers extrusion, blow molding, additive manufacturing, automation and end markets including automotive and packaging. He also writes features, including In Other Words and Problem Solved, for Plastics Machinery & Manufacturing, Plastics Recycling and The Journal of Blow Molding. He has extensive experience in daily and magazine journalism.
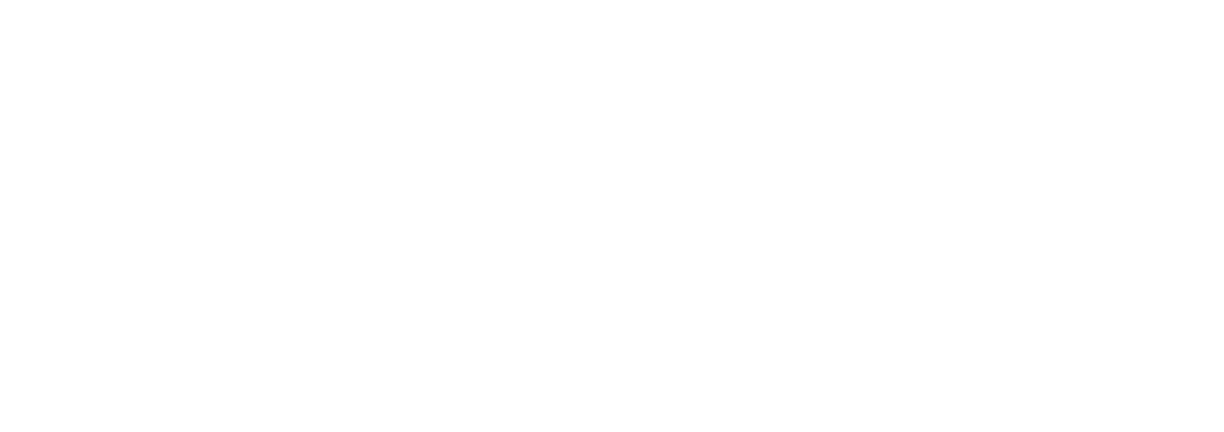