Kosmek, a manufacturer of magnetic, hydraulic and pneumatic clamping systems used for injection molds, jigs and fixtures, has introduced two new developments for its magnetic clamping systems.
A supplier of quick mold change systems for injection molding machines and die-cast machines, the company is touting its Multi Information Monitoring System (MIMS) for its magnetic clamping systems. MIMS provides more information to the user, such as the actual magnetic force being applied in an application, said William Shelley, a salesman at the company's satellite office in Belleville, Mich.
Kosmek's magnetic clamping system is comprised of two 37mm-thick, full-metal magnetic plates that are attached to the platens of an injection molding machine. Numerous round hockey puck-like aluminum-nickel-copper (Alnico) magnets designed by Kosmek are embedded into each plate at regular intervals to provide a uniform magnetic field. Kosmek says the 37mm plates are the thinnest in the industry. It also offers 46mm-thick magnetic plates.
When the plates are demagnetized, the magnetic force is balanced within each plate and no magnetic attraction is exerted on the surface facing the mold. To attach the mold to the magnetic plate, the mold is lowered into place and aligned with the locator ring. Then, an electrical current is applied to the Alnico magnets. This short application of current reverses the polarity of the Alnico magnets, which then generate a self-sustaining magnetic force that extends up to 20mm from the surface of the magnetic plate into the mold, holding it securely in place.
The magnets need no external power to produce this magnetic force and will maintain it until another electrical current is applied to reverse the magnets' polarity, allowing for the mold to be unclamped from the magnetic plate. It takes 1 second to activate the magnetic plate and 0.5 second to deactivate it.
The operator panel has a Magnetic Force Indicator, that signals an alarm when magnetic force falls below 75 percent of the system's total magnetic strength. The panel also displays an actual measurement of the mold contact area over the magnetic plate, so users are not required to input mold size or other data. A control box shows mold clamping force, and the system signals an alarm if it detects that a user-selected minimum clamping force is not reached. The magnetic plate control communicates with the controller of the injection molding machine to prevent operational errors.
MIMS also reads sensors built into the magnetic plate to monitor the temperature of the magnets, because higher temperatures can impair magnets' performance. Kosmek's magnetic clamping system operates in temperatures of up to 248 degrees Fahrenheit.
In addition to developing the MIMS control, Kosmek also has developed a wireless monitoring system for its mold clamping systems. The remote monitoring system collects machine condition and user information, and uses Wi-Fi or a 3G or 4G signal to send it to a customer's smartphone or tablet, as well as to Kosmek's maintenance/technical staff. The new wireless monitoring capability can be used with the company's magnetic, hydraulic or pneumatic clamping systems, and can be retrofitted to existing systems.
Mikell Knights, senior staff reporter
Contact:
Kosmek USA Ltd. Lombard, Ill., 630-620-7650,
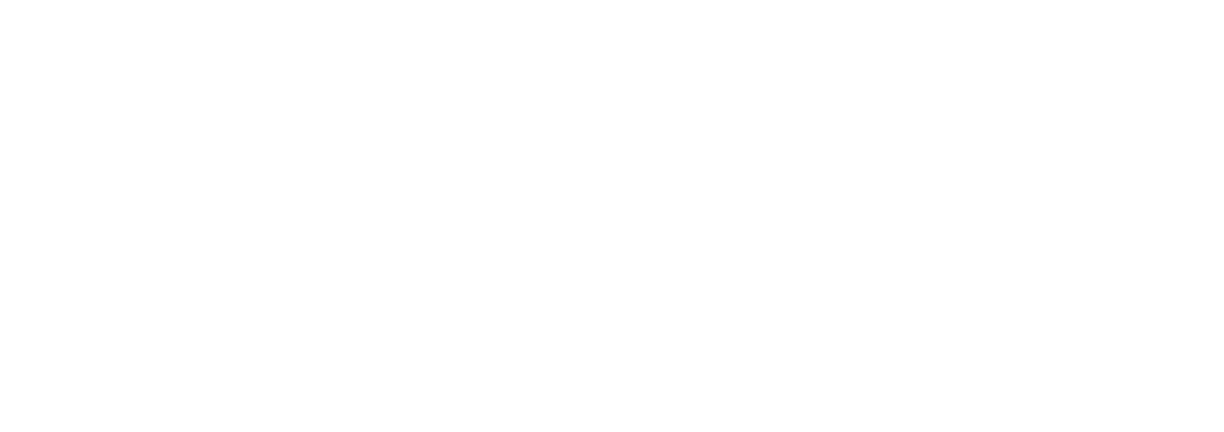