At NPE2018, advances in injection molding machines with two-platen clamping designs focused on molding larger parts and delivering greater operating speed, versatility and efficiency. Many of the new models featured updated or redesigned servo-hydraulic or "hybrid" drive systems to control the movement of the injection unit or clamp.
MILACRON ROLLS OUT NEW LINE FOR BIG PART MOLDING
Milacron introduced its new Cincinnati line of large-tonnage two-platen machines, designed to meet the demands of markets requiring big molded parts, such as the automotive or appliance industries.
The Cincinnati line includes nine models with clamping forces ranging from 1,470 tons with the Cincinnati 1500 model to 6,745 tons with the Cincinnati 6600 model. Suited to multi-component applications, the machines deliver fast clamping speeds and an ability to handle heavy molds. The machine layout, with easier access to the ejectors and mold area, makes operation, maintenance and servicing easier than competing models. The line complements Milacron's Maxima two-platen line, which ranges from 500 to 1,100 tons of clamping force, said Ron Hertzer, director of technology research and development for Milacron's Advanced Plastics Processing Technologies unit.
Milacron introduced the new injection machine line at the show with a Cincinnati 2250 model. With 2,250 tons of clamping force, the machine was the largest-tonnage injection molding machine ever at NPE, the company said. The unit generated a 10.5-pound shot of HDPE to produce a dashboard for an all-terrain vehicle in 130 seconds. The demonstration unit at NPE2018 featured a TempMaster iM2 temperature controller from MoldMasters. A six-axis robot from Sepro operated through the machine controller, Hertzer said.
Milacron said the new two-platen design is compact and rigid, yet light, which helps to save energy costs. All critical machine movements are driven by a proprietary servo-hydraulic system that incorporates four servo motors and drives from Fanuc to control the hydraulic gear pumps. For improved melt-temperature control, the Cincinnati line has an additional heater on the injection side, and the hot runner can be integrated into the injection unit.
The machine also is equipped with newly designed transducers and active sensors that capture and transmit data used to determine the overall equipment effectiveness of the machine. The data collected by the sensors show in detail if a process is out of tolerance and how to correct the issue. The machine is equipped with Milacron's Mosaic software.
Milacron also designed the machine to provide quick access to the screw and barrel for rapid changeovers.
The 6,745-tonner has been ordered by an Ohio-based molder. The Cincinnati 2250 model it displayed at NPE2018 was sold to i2-tech, a custom injection molder based in Iowa.
KRAUSS-MAFFEI ADDS SPEED OPTION
Krauss-Maffei has updated its GX series of two-platen presses with a new speed option that makes the machine more efficient when molding large packaging and logistics products. It also has made enhancements to the machine controller. This combination achieves higher injection speeds with faster cycle times.
The GX series is Krauss-Maffei's medium-tonnage two-platen line, with clamping forces ranging from 440 tons to 990 tons.
The new speed option allows for injection speeds of up to 700mm per second depending on the type of injection unit, and clamping speeds as fast as 0.45 second, President and CEO Paul Caprio said.
The use of the company's E-Plast electrically driven plasticizing unit enhances parallel movements to support the shorter cycle times. Use of the company's HPS high-performance barrier screw, standard with the GX series, also enhances performance.
The design of the GX series allows for different drive system combinations for the injection unit or clamping. The PowerPack system incorporates the latest generation of variable-speed hydraulic delivery pumps and employs premium components. The company's Blue Power servo drive motor and pump technology can be used instead of the variable-speed pumps to run the hydraulics, resulting in 10 percent to 30 percent greater energy efficiency. Additional options for the PowerPack are available for faster clamping force buildup, screw decompression or injection unit movement.
The MC6 machine controller adds several new functions that improve operating efficiency. For example, the ProcessDesigner tool provides a clear visual presentation of the status of all current processes in operation. Users see a graphical representation of the machine and can modify an operation using drag-and-drop or swiping movements. A new Eco button guides the machine operator in determining the configuration that yields the most energy efficiency for an application, Caprio said.
The company updated the panels on its machine base for easy access to the hydraulic components. The panels feature a quick-click design, allowing them to be removed or snapped into place quickly.
The GearX locking system is an enclosed clamp-locking device located behind the moving mold platen that requires only a short motion to engage or disengage. Clamp force is generated through four pressure pads behind the stationary platen.
At NPE2018, a GX 900-12000 unit employing the speed option produced 5-gallon buckets in a two-cavity mold in a cycle time of less than 14 seconds. The speed option allowed for part decoration using an in-mold labeling (IML) process. Until now, printing has been the primary decoration method for large molded parts like buckets, Caprio said. IML is difficult with the standard injection speed of conventional large-part molding, which exposes the labels to the heat of the injected resin for longer, increasing the potential for damage to the labels. The GX speed option completes each cycle more quickly, decreasing the labels' exposure to heat and increasing output and cost-effectiveness.
YIZUMI-HPM CREATES SERIES FOR NORTH AMERICA
Yizumi-HPM introduced its new DP-N series of two-platen molding machines designed for the North American market with clamping forces ranging from 550 tons to 4,000 tons. The model line targets large-part automotive or consumer products such as bumpers, grilles, garbage bins or washing-machine drums.
At NPE2018, a UN1200-DP-N-12050 model with 1,200 tons of clamping force demonstrated FoamPro, a rapid-heat, rapid-cool microcellular foam injection molding process developed in partnership with Trexel Inc., Wilmington, Mass. The DP-N machine and FoamPro process produced an 880-gram briefcase from PP in 49 seconds.
Compared to a traditionally produced briefcase, the FoamPro process made a part that weighed 20 percent less while maintaining part strength. It also reduced the clamping force requirement up to 50 percent, said Bill Duff, GM of sales and marketing.
The DP-N is outfitted with components from globally recognized companies. This includes servo valves and proportional valves from Bosch Rexroth of Germany, servo-motor technology from the Italian company Phase, a hydraulic motor from Staffa of Britain and Hägglunds of Sweden and machine controls from Keba of Austria.
FCS UPDATES LA-SV LINE
Fu Chun Shin (FCS) Machinery Manufacture Co. Ltd., Tainan, Taiwan, sold here exclusively by Maruka USA, debuted its updated LA-SV line ofservo-hydraulic two-platen machines. Machines in the line have clamping forces ranging from 550 tons to 4,070 tons of clamping force. The company added the 4,070-tonner earlier this year. The series uses the Keba i2880 touch-screen controller.
FCS improved the clamp mechanism for quicker locking. This allows the clamping force to build up in 15 percent less time than previous designs. At NPE2018, FCS displayed an LA550SV model with 550 tons of clamping force producing food trays.
WITTMANN BATTENFELD TOUTS MACROPOWER NEWS
Wittmann Battenfeld announced the first shipments of the largest model in its Macro-Power line of servo-hydraulic two-platen injection molding machines.
The line, offered in 19 standard sizes with clamping forces from 400 tons to 2,000 tons, has a four-tie-bar, two-platen clamping design. A modular twin-pump hydraulic system with electrically adjustable delivery pumps drives all major machine movements.
A molder can swap the standard asynchronous motor for a drive-on-demand servo motor.
At NPE2018, a MacroPower 850/8800 demonstrated new machine intelligence technologies developed by Wittmann Battenfeld. For the first time, all the models incorporate the company's new B8 machine controller.
The injection molding machine, used to produce a vehicle spoiler in a single-cavity mold fitted with five servo valve gates and several cavity-pressure sensors, operated with the company's HiQ optional process-optimization tools. The suite enhances the melt monitoring, flow monitoring and cushion monitoring capabilities that are standard with the machine controller.
The tools included the HiQ-Melt software, which monitors material viscosity and automatically controls the machine parameters to maintain consistent quality, and HiQ-Flow software, which finds the optimum production switch-over point from filling to hold (based on position or holding pressure), providing greater real-time control than the flow monitoring that is standard with the machine controller. Additionally, HiQ-Cushion software controlled the melt cushion for more efficient operation.
NEW LINE COMBINES UBE/MITSUBISHI TECHNOLOGIES
Ube Machinery has developed a new high-performance servo-hydraulic two-platen series dubbed the U-MHIPT MMX. The machine line comprises seven models with clamping forces from 200 tons to 3,900 tons, said Romy Vlad, engineering department manager.
Models in the series have a four-point, two-platen clamping mechanism that's designed to handle an unbalanced load but able to deliver uniform clamping pressures across the mold with minimal deviation of platen parallelism. Although electric motors drive material plasticization in the injection unit, a servo-hydraulic system governs the remaining major machine movements. It features the company's Smart Pump System, which combines an induction motor and a variable-capacity piston pump. A fast-response servo motor controls the "smart pump" system.
This drive combination uses 40 percent less energy than a conventional fully hydraulic two-platen press molding the same part.
The MMX series comes with a new MAC-VIII+ controller that features a 12-inch touch-screen LCD panel and has programs used to achieve ideal molding conditions efficiently, such as automatic setup.
Users can quickly access main control screens by pushing the digital buttons on the control panel. In addition to displays of the process cycle, alarms or settings, the control system has a display, called the NG screen, that flags incorrect setting values.
Mikell Knights, senior staff reporter
Contact:
Krauss-Maffei Corp.,
Florence, Ky., 859-283-0200,www.kraussmaffeigroup.us
Maruka USA Inc.,
Lee's Summit, Mo., 816-524-1811,www.marukausa.com
Milacron LLC, Batavia, Ohio, 513-536-2000, www.milacron.com
Ube Machinery Inc.,
Ann Arbor, Mich.,734-741-7000,www.ubemachinery.com
Wittmann Battenfeld Inc.,
Torrington, Conn., 860-496-9603,www.wittmann-group.com
Yizumi-HPM Corp.,
Iberia, Ohio, 740-382-5600,www.yizumi-hpm.com
Carteaux championed industry
Bekum announces leadership changes
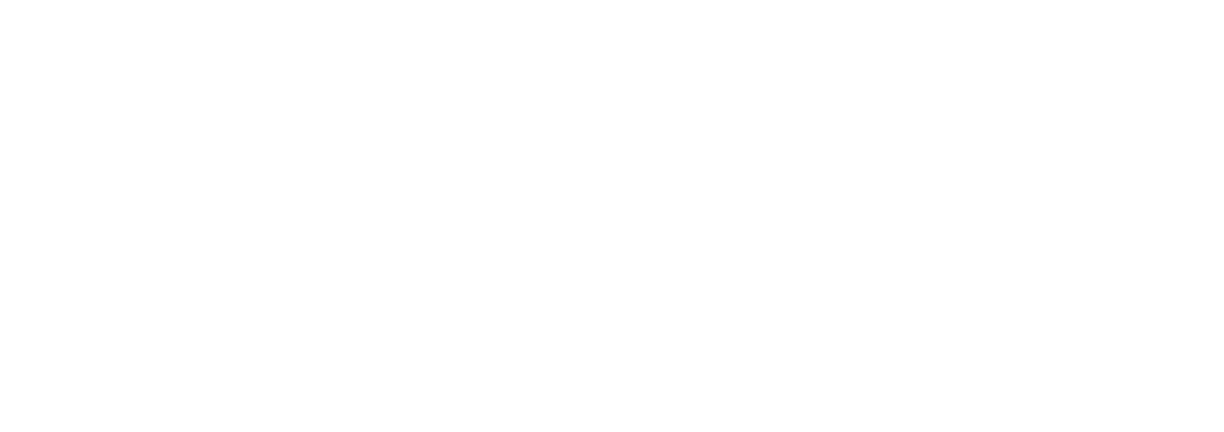