Engel Group is expanding its offerings of standard-application injection molding machines with the entrance of its Wintec subsidiary into the U.S. market.
The Changzhou, China-based subsidiary, which makes its debut in the market at NPE2018, will begin selling its machines in Canada, Mexico and Brazil, as well as the U.S., Wintec Americas President Peter Auinger said. Engel has tapped Don Ivey as Wintec's director of sales for North America, with responsibility for Canada and the U.S.
While Engel focuses on sophisticated applications that require tailor-made injection molding solutions and special processing technologies, Wintec machines are used for high-volume, single-component injection molding. Machines can be delivered preconfigured, allowing for quick startup.
Engel, based in Schwertberg, Austria, believes now is an opportune time to take advantage of market changes. "We see a strong demand in the U.S., as well as in Canada, Mexico and Brazil, for injection molding machines that handle standard applications. This is why we are bringing the Wintec brand to these areas," he said.
Auinger said Wintec has a dedicated sales force working throughout the region. The Engel service staff will provide after-sales service. The combination will allow the company fast on-site support from the start.
Wintec will offer the same product line in the American market as it does in Asia, but will refer to the clamping forces in short tons instead of metric tons. It will offer both electric and hydraulic machines.
"In addition to sophisticated applications that require tailor-made injection molding solutions, we see a strong demand in America for injection molding machines that handle standard applications," said Christoph Steger, the chief strategy officer for Engel Group. "This is precisely the market segment in which Wintec is at home. By expanding the sales area to the American markets, as the Engel Group, we can provide tailored solutions at an attractive price/performance ratio."
The company is offering its hydraulic two-platen t-win series with clamping forces from 500 tons to 1,900 tons. The machines are equipped with Wintec's servowin servo-hydraulic technology, which cuts energy consumption by more than 60 percent in comparison with presses with conventional hydraulics.
Wintec also estimates total overall ownership cost savings of 26 percent for the t-win, with 23 percent higher productivity, compared to conventional hydraulic machines. Operator comfort is improved by features like a low nozzle center line — the height above the ground — and its controller, which can swivel out and can easily be adjusted for height.
The t-win's dual-platen clamping unit guarantees maximum platen parallelism throughout the machine's service life, for excellent dynamics and short dry-cycle times, the company said.
The other line, the e-win, is used in a wide range of applications. The machines have clamping forces ranging from 55 tons to 310 tons. All the machine movements are servo-electric. Wintec said the machines' movements are very precise to ensure good part quality and a stable process. The parallel movements of the drives and the high acceleration of the injection axle allow for short cycle times.
With their electric drives, the e-win machines provide several advantages, including cost savings, Wintec says. Also, the machines are compact, saving space. The clamping unit automatically recognizes the mold height, which simplifies the set-up process because the operator doesn't need to enter that parameter.
The machines' high-precision dynamic clamping drive provides shorter dry-cycle times, better productivity, protection against mold wear and linear guidance of the moving platen.
A standard, swivel-out injection unit allows maximum accessibility of the screw tip and minimal overhead clearance for the changing and cleaning of the screws. Finally, the control unit's speed, stability and intelligent drive management result in performance that's 33 percent better than market average, according to Wintec.
The C2 control featured on both machines provides intuitive operation and reduces the risk of operator error. For ergonomic operation, the 15-inch touch screen can be pulled out and its height adjusted. The C2 is compatible with a variety of robot types and brands.
As part of Engel, Wintec can provide single- source, integrated production cells with robots designed and manufactured in-house.
Auinger said Wintec has no plans to expand machinery manufacturing from its current production plant in Changzhou, where the company started in 2014. The machinery is designed and developed in Europe.
Wintec said its machines have an operating life of 15 to 20 years or more and comparatively low operating costs.
Allan Gerlat, correspondent
Contact:Wintec Engel Machinery (Changzhou) Co. Ltd. Changzhou, China, 86-519-8159-5300,
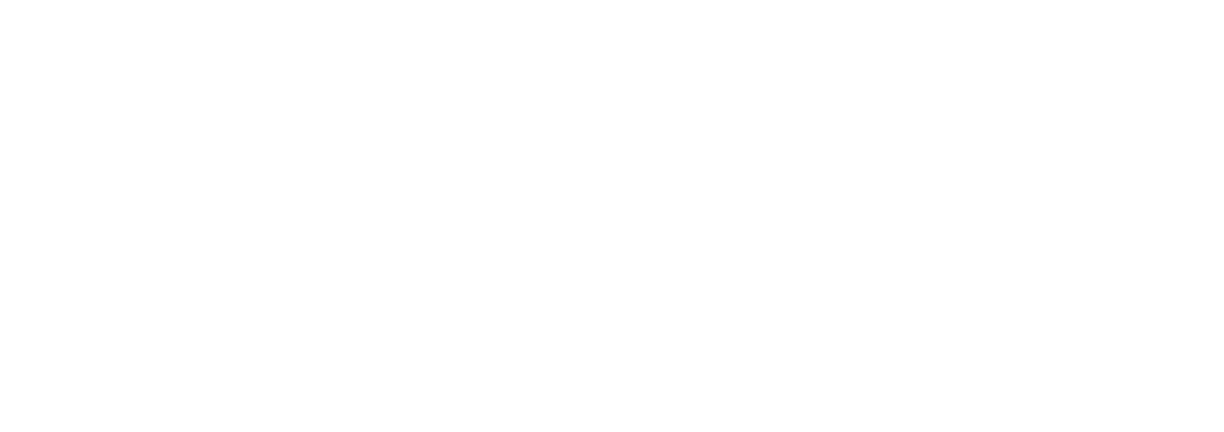