Yudo Group, Incheon, South Korea, has developed a new method for manufacturing hot-runner manifolds that incorporates flow channels designed with conformal cooling principles in mind. Yudo introduced the technology in October during the International Plastic Fair in Tokyo.
Yudo's ISO Technology uses a special bonding method and insert-core technology to create melt channels that perform better than conventional gun-drilled channels, said JongBae Kim from Yudo's hot runner system division.
Melt flows about 30 percent more efficiently, with less shear, through a specially created conformal channel than through a gun-drilled channel, Kim said.
A key benefit of the bonding technology is that it creates a curved channel where a change of direction is required. Conventional gun drilling creates a T-shaped or L- shaped intersection to produce a change in the flow path. A sharp corner in a flow path can become a dead spot, which impacts material flow. In addition, a sharp corner changes the shape of the channel's cross-section, increasing the area. Varying the shape of the flow channel can change the shear rate experienced by the melt.
Melt injected by the plasticizing unit enters the manifold through a single large channel. If the manifold is designed for a multicavity mold, the main channel in the manifold feeds a multilevel or tiered hot-runner system. The tiered configuration allows for more cavities while keeping channel lengths uniform. However, the melt has to travel, either from one level within the mold to another, or when it branches from a channel to an individual nozzle that injects the polymer into a mold cavity. Gun-drilled channels have sharp corners wherever the melt is directed to another distribution level or is split into two smaller, uniform flow paths into the mold.
With Yudo's approach to manufacturing conformal flow channels, part of its ISO Technology, the dimensions of the flow channel remain unchanged when there is a directional change.
To produce a manifold with the optimized melt channel, Yudo slices a block of steel into two layers. A CNC machine cuts half of a flow channel into each layer. Using the bonding process, the metal layers are rejoined, forming a complete channel.
Yudo developed special testing and inspection equipment to ensure the performance of the special bonding technique.
Yudo said that using ISO Technology reduces the stress on the resin, which is a benefit when processing sensitive materials such as resins containing long glass fibers. ISO Technology also helps to maintain a thermal balance within the mold. Color changes are faster because dead spots are minimized.
Yudo also is applying ISO Technology to the cooling channels of the mold. Yudo said incorporating a conformal cooling channel produces more effective mold-temperature control and can shorten mold cooling (and hence overall production cycle time).
The development of the ISO Technology is based on its 30 years of experience in injection molding, the company said.
Yudo is known in the Americas primarily as a supplier of hot-runner systems, hot-runner temperature controls, servo-valve cylinders and sequencing timers, as well as take-out, six-axis and Cartesian robots. But it also offers a real-time, plantwide monitoring and control system, and molds for medical, packaging or PET preform applications. In the U.S., it is represented by Yudo Inc.
Mikell Knights, senior staff reporter
mknights@plasticsmachinerymagazine.com
Contact
Yudo Inc.Livonia, Mich., 734-744-8120, www.yudousa.com
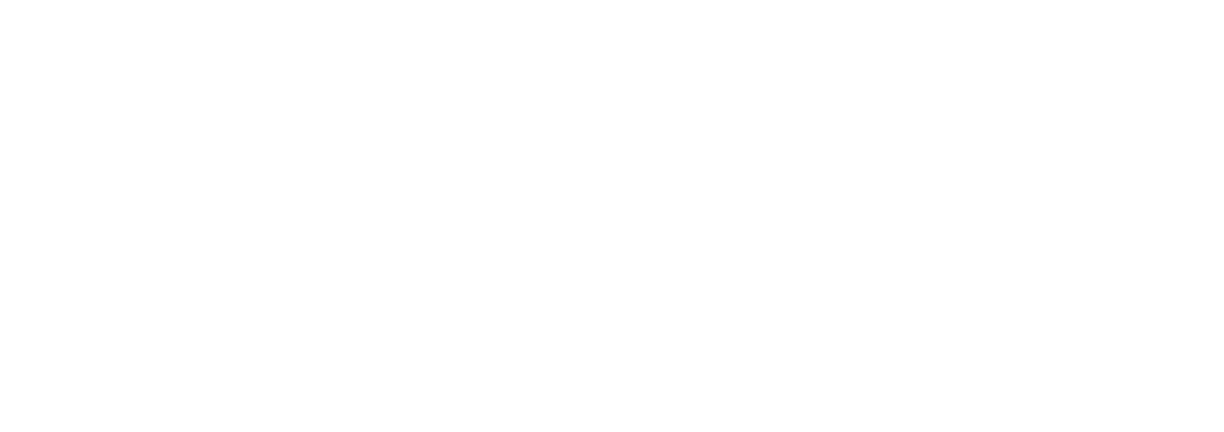