A1 Tool Corp. is an injection mold maker whose approach constantly is progressing on machinery, equipment, people and processes.
Under the leadership of CEO Geoff Luther, the operation is undergoing a metamorphosis as it adapts principles from the assembly line Henry Ford created in 1913.
"Our thought process has evolved in how to build molds," Luther said. "It continues to evolve. There is a lot more to mold making today than just designing the tool. We have complete ERP [enterprise resource planning]; we have a complete strategy in building our tools."
Within its nearly 85,000-square-foot mold-making shop, the latest high-speed and multi-axis machinery is at work creating high-quality molds with complex geometries, supported by a rigorously structured workflow. The workpieces include many types of molds such as stack and tandem.
A1 makes 100 to 150 molds per year for customers around the globe in a variety of industries; the end products include automotive, medical, and industrial parts as well as industrial containers, home appliances and home building products.
Every component is tracked and staff can view the status of each project, how close it is to being done, and the order in which unfinished components will be completed. Luther identifies his company's workflow as the most innovative aspect of its evolving transformation.
Central to the approach is the work of nearly 30 machining centers. The latest machining center is a DMC 125 FD duoBlock, a full-five-axis machine that does both milling and turning work all in one machine.
"Being able to do both lathe and mill work all in one machine improves efficiencies," Luther said.
According to DMG Mori, the machine manufacturer, the DMC 125 FD duoBlock performs milling and turning in one setup thanks to its DirectDrive rotary table with speeds of up to 800 revolutions per minute.
"There are different machining techniques and strategies that you would use for every machine," Luther said of the challenge of creating some of the intricate geometries.
"Some machines are more robust, some are less robust. If you are working with a multiple-axis machine, the machine will actually do a pivot on that axis and do what it needs to do to get to that geometry," he said. "You need to understand the accuracies of the component that you're working on and the ability of the machine to get the desired result."
Another recent machine, a Hermle full-five-axis machining center, allows A1 to achieve accuracies of 0.0001 inch even in simultaneous five-axis contour milling. Luther called it very dynamic, very fast and very accurate.
One other high-speed machining center, an FPT Pragma, has seven independently controllable axes with travel distances of nearly 30 feet.
On the day of a Plastics Machinery Magazine's tour, that mill was machining mold components for a shroud used on an air conditioning system for a four-wheel-drive agricultural tractor.
A1 produced the tool after extensive cooling and warp analysis. The complex mold had many bosses and tongue-and-groove components, and it successfully molded parts on its first sample run.
"You can machine well and accurately, but you need to have the ability to know and understand the complete mold and process," Luther said. "We are scheduling every process for every component. Our specialized work cells become a perfect area to train people."
A1 even has made it more efficient to make repairs and revisions to molds without prints by using laser scanners and coordinate measuring machines to do reverse engineering. They can scan the 3-D geometries of existing models, parts or molds, and then reconstruct those in the CAD system.
The 87 employees within A1 are expected to follow the process strictly. Work stations throughout the factory are designed to allow A1 to build molds faster. Each work station is laid out optimally to improve workflow.
"With our process, the ability to track the pieces and who worked on them creates accountability," Luther said. "By breaking things down into smaller bits and pieces, it is different than the way it used to be, but this allows us a better way. In this business, details matter."
Within the last few months, Luther appointed Joe LaMonica as CFO to create even more efficiencies. Having LaMonica focus on finances freed up Luther to focus on manufacturing.
The processes and systems allow A1 to tackle especially challenging projects, such as a very intricate two-shot mold for an automotive air- handling system.This project carried with it a particular challenge. The mold had to fit into a 650-ton injection molding press rather than an 800- or 1,000-ton machine.
"A passion for machining efficiencies is what sets A1 Tool apart," Luther said. "Our commitment shows in our operations and through to the tooling."
Angie DeRosa, managing editor
Contact:
A1 Tool Corp.,Melrose Park, Ill., 708-345-5000, www.a1toolcorp.com
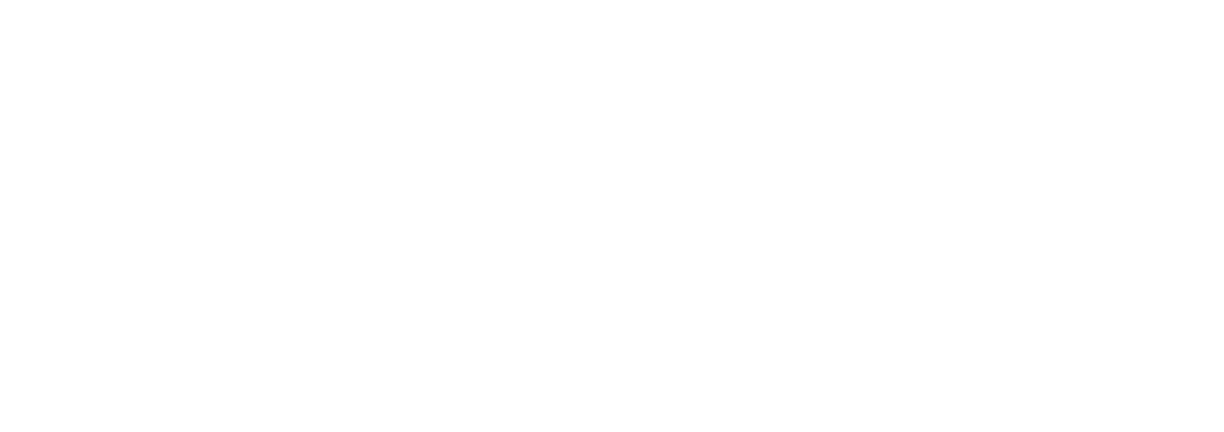