Designing a processing facility with safety in mind can be complicated — particularly when potential dangers can lurk in the most mundane activities, like materials storage or working alongside forklifts and other heavy machinery.
From storing materials properly, to creating safe exits for employees, to ensuring the facility meets all building codes, there are a lot of details to manage. But it's far better to put the time and effort into the design stage than to suffer what could be dire consequences down the road.
The building blocks of a safe facility
Long before the specific requirements of plastics processing are even considered, companies need to ensure their facilities meet all of the requirements of the federal, state and local governments. They can be cumbersome, but they are absolutely critical. They don't just protect workers from harm; they protect the business from fines and potential litigation.
The next step is to consider the additional safety requirements of operating an industrial facility. There is a plethora of potentially dangerous things in such a plant — forklifts, superheated resin and huge presses, to name a few. But one of the first considerations should be the risks posed by the materials being stored and used in the building, said Mark Hertzfeldt, an architect with Design 2 Construct Development Corp.
While some of those materials are clearly dangerous, such as flammable gases and liquids, the risks of others might not be as obvious. "Materials can be considered hazardous if they produce large volumes of smoke or otherwise hinder the ability of the fire department to perform their duties," Hertzfeldt said.
"The building code has very specific regulations not only about the amount of material that can be stored within the facility, but also how that permitted material is stored," he said. "If the plant is going to have more of that material than is permitted, the excess material must be stored within a 'control area,' which is a fire-rated — and sometimes explosion-rated, too — enclosure within the building."
In some cases, it also may be necessary to provide spill control, which would protect workers and the environment if there is an accident involving a hazardous material.
The types of materials onsite and how they are stored also affect the design of the fire-protection systems in the building, specifically the sprinkler system. When working on a building that will contain flammable materials, Design 2 Construct installs an early suppression fast response (ESFR) sprinkler system. "This provides a fire sprinkler system that allows for material racking storage without the need to install sprinkler lines within the racking, which adds substantially to the cost," Hertzfeldt said. "It also helps alleviate some concerns relating to the hazardous materials."
When sprinkler contractors evaluate a building, they assign an occupancy hazard classification to it. This hazard category tells the contractor how robust the sprinkler system must be to provide adequate protection for the building and its occupants. A fire alarm system with both heat and smoke detection also could be required. "This can be a challenge to design and install around the machinery and processes taking place on the production floor" because that equipment generates so much heat even when operating normally, Hertzfeldt said.
The production area offers other challenges, as well. Building occupants need clear paths of travel around the equipment and material storage areas on the production floor so they can exit quickly in case of an emergency. Egress doors must be placed in locations that limit the distance occupants are required to travel before they are able to vacate the building in an emergency; those locations can be as close as every 100 feet. That can be inconvenient when it comes to the placement of equipment and storage areas.
"Emergency lighting and exit-light fixtures also must be installed to provide minimum lighting levels and egress direction," Hertzfeldt said. "That can make things pretty complicated, given how much rack storage and large machinery is used in plastics production."
When designing a building, owners always consider factors such as having adequate parking, and ensuring that trucks have easy access to the loading areas. Access for emergency vehicles is also critical.
"The fire department has very strict requirements for access to the site, proximity to the building on the site for their vehicles, and locations for onsite fire hydrants to help them fight fires," Hertzfeldt said. Many of these requirements only apply to large buildings, but plastics facilities are big enough to be subject to them.
Post-construction considerations
The next step is to identify what additional safety steps need to be taken once the structure is built because it's impossible to completely eliminate risks through facility design, no matter how detailed and thorough the planning might be.
For example, a plant is inevitably going to have certain areas that pose greater risks than others. If robots will be operating in a given area, physical barriers such as fencing can prevent workers from unknowingly entering the danger zone.
Where there will be heavy forklift traffic — or blind turns, where someone could inadvertently walk into the path of an oncoming forklift — signs should be posted to alert people, said Subodh Sharma, president and CEO of Oak Tree Engineering. Those types of low-cost measures can pay big dividends over time. "Unfortunately, people often either neglect or forget to put up the signs," he said.
Addressing the specific risks associated with plastics processing is the final step in designing for safety (although safety and risk management are ongoing practices that never really end).
When designing a new injection molding plant, for example, consideration should be given not only to the amount of space required for injection molding machines and robots but also safety equipment, including fencing or other guarding systems.
"Safety is always the biggest thing with automation for us," said Jason Long, national sales manager for robots and automation at Wittmann Battenfeld. "When it comes to floor space, you have to think about how much reach that robot has. Where can that robot reach when it is running? Guarding has to be just outside the reach of the robot."
When it comes to injection molding, plants normally use one of two types of guarding: a wire mesh fence or clear PC or plexiglass walls.
"The plexiglass design, because it is solid, can allow for a smaller footprint when designed for automation because nothing can get through it," Long said. "But wire mesh, because it has holes in it, you can reach a finger or hand through it, so it requires a bigger footprint."
Other options include light curtains, which use beams of light instead of a physical barrier to protect workers. If the beam of light is broken, a robot or an entire work cell will shut down. However, the technology rarely is used for injection molding because light curtains require even greater space around a robot to ensure adequate time for the robot to shut down before someone breaking the beam could come into contact with it.
There are a lot of safety standards out there and they often are difficult to understand, Long said. It's one of the big reasons companies hire integrators to do automation.
With extrusion equipment, employees often have to stand on top of the machine to perform their duties, so platforms should be constructed in those areas, complete with a railing and a door that opens inward. "Some companies have started to have operators wear a safety harness when working on top, connected to a ceiling strut," said Ottmar Brandau, president of Guelph, Ontario- based Apex Container Tech, which provides design services to the blow molding industry.
In compounding facilities, dust and fumes from the extrusion process are a common problem. Normally, plant designers can minimize exposure to dust and fumes by employing efficient and well-designed dust- and fume-extraction systems, Sharma said.
However, in some cases — depending on the type of materials and the size of material containers — where dust explosions are possible, operators need to provide proper explosion venting to direct the explosive force outside of the building, rather than inward.
Similarly, in mixing rooms where dust is almost always present, design considerations should be given to make sure that explosion panels can be installed on an outside wall, Sharma said.
For more information
Apex Container Tech Inc.,Guelph, Ontario, 705-429-1492, www.blowmolding.org
Design 2 Construct Development Corp.,Jackson, Wis., 262-677-9933, www.design2construct.com
Oak Tree Engineering LLC,Monroe, Mich., 734-244-5231, www.oaktreellc.com
Wittmann Battenfeld Inc.,Torrington, Conn., 860-496-9603, www.wittmann-group.com
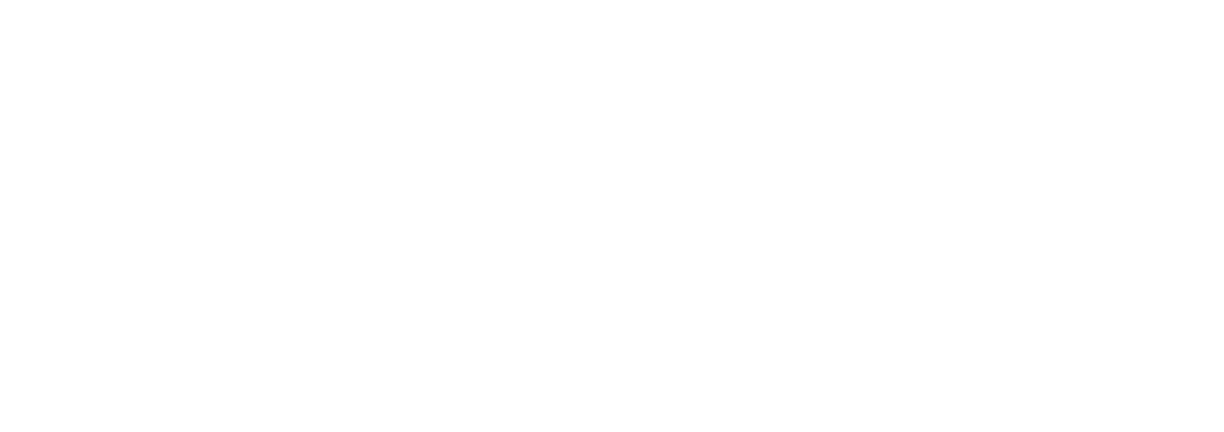