Controlling water use is an important step for processors interested in reining in utility costs.
The costs for water and energy are interlinked in many ways, and both are key considerations when designing a manufacturing plant. If a plant can reduce its water usage, it can typically reduce water-cooling costs.
Several equipment systems suppliers weighed in on water management techniques. They offer some of the latest equipment on the market.
Plant managers can choose between traditional cooling systems with chillers and cooling towers and newer processes that rely on closed-loop systems. Variable-speed devices, which offer better control of utility costs than on-off switches, are gaining popularity, experts said.
THERMAL CARE
For optimal water management, processors need to consider the entire water ecosystem, said Bob Smith, director of product management for Thermal Care, which supplies process-cooling equipment, including portable chillers, central chillers and cooling towers.
"Process cooling is the lifeblood of a manufacturing facility," Smith said. "If you compare it to a human body, the machines are like the muscles and the power is like the veins. It brings nutrients and energy to the entire system."
Water is essential to keeping the system cool (like perspiration) and running at optimal efficiency, Smith explained.
"But it's not just the chiller; it's also the pump and the piping, it's the whole system," Smith said. "The best way to save is to design an overall system. Make sure you have proper flow to the system; make sure that you have pumps that provide enough flow to the system and make sure that you have the right piping to reduce the resistance to flow."
Continuing the human body analogy, the pumps are like the human heart, while piping that is too narrow is like plaque built up in the circulatory system, Smith explained. "A lot of people neglect the piping. Poor systems result in a lot of pressure drops because the pipes are the wrong size. That burns up a lot of energy."
He added that too many suppliers concentrate on single components like the chillers, pumps or piping, without looking at the entire system.
Pipes need to be the right size so that water flow isn't restricted and pumps should offer variable speeds, so they can conserve power and water by running only at the capacity that's required, Smith said.
Smith was among process-water experts who recommend using equipment with variable-speed compressors, which operate chillers more efficiently than fixed-speed units, Smith said. Thermal Care offers variable-speed compressors for both stationary and portable chillers.
Fixed-speed chillers maintain a constant demand on the compressor to avoid wide fluctuations in the coolant temperature delivered to the process for consistent output.
Thermal Care's NQV variable- speed chillers constantly monitor the heat load and adjust the compressor speed for peak efficiency and temperature control. By automatically adjusting the compressor speed, the chiller works only as hard as necessary to provide optimum performance with significantly reduced power use.
According to Thermal Care, a 20 percent reduction in motor speed can lead to a 51 percent savings in energy consumption.
FRIGEL
The choice of chiller makes a difference in energy usage, said Al Fosco, global marketing manager for Frigel.
"Without proper and thoughtful design of a cooling system, problems can occur that can shut a plant down completely," Fosco said, weighing in on the inefficiency of central chillers. "They use huge amounts of water and chemicals," he said.
Frigel instead provides its Ecodry 3DK adiabatic liquid closed-loop cooler. Because the water isn't exposed to the outside air and can't evaporate, the system reduces water consumption by as much as 95 percent compared to a cooling tower, Fosco said. This also keeps the water cleaner, reducing the need for chemical cleansers.
"Our Ecodry system has multiple, individually wired fan motors and automatic standby pumps, which prevent catastrophic failure and our machine-side, individual Microgel concept also prevents complete blackouts as can happen with a central chiller system."
In the 3DK units, hot air passes through the lower adiabatic chamber. In the chamber, nozzles create a fine mist of water from a separate source only when required due to elevated ambient air temperatures.
Humidification of the air reduces the temperature prior to contact with heat exchangers. A patented design prevents water from leaving the chamber, eliminating heat exchanger scaling and the risk of proliferation of bacteria. To ensure consistent cooling, the control system continuously adjusts the amount of water that's sprayed. The heat exchangers, meanwhile, stay dry.
The controller monitors pressures, temperatures, coolant levels, and the performance of the pump. The accurate, real-time information allows operators to identify problems that require maintenance early. With intuitive, touch-screen controls and commands, including alarms and fault indicators, issues can be identified early.
The system control panel enables operators to connect to a building-wide monitoring system via Modbus RTU over an Ethernet TCP/IP network, while also providing remote, real-time monitoring capabilities to Frigel's global service technicians.
GREEN BOX
Mike Peyser, director of sales and marketing for Green Box America, is another proponent of closed-loop systems. That's because, he said, they don't require a continual influx of chemicals.
Green Box has offered the cooling systems in the U.S. for several years, but newer, smaller systems just now are hitting the market, he said.
The Green Box fluid cooler modules, which are mounted outdoors, receive the hot water returning from the process and provide efficient air-to-water heat exchange. Each has variable-speed fans, to adjust capacity as needed.
When the fans operating at full capacity can't supply the needed cold water (for instance, during the heat of summer) the Green Box Adiabatic-SSS system atomizes water into the ambient air to reduce its temperature before it enters the heat exchanger.
According to Peyser, the Green Box fluid coolers feature a very efficient atomizing system, and the Adiabatic-SSS uses relatively little water. The fluid system's PU filters are cleanable and reusable; they don't decay like paper-fiber filters. The system also features brass nozzles and stainless-steel pipes.
The company's self-draining fluid coolers can provide a leaving-water temperature as low as minus 47 degrees Fahrenheit. Under certain conditions, the system will automatically drain the water to an indoor tank to prevent any damage from freezing. Such conditions include extremely low ambient temperatures, reduced process loads, plant shutdown and power outage. These units have recently become available in the U.S., Peyser said.
ADVANTAGE ENGINEERING
Like other experts, Advantage Engineering President Jon Gunderson recommends the use of variable-speed drives on pumps and fans. They help provide better process control and save energy. Advantage Engineering supplies central and portable water chillers, cooling towers and related equipment.
Most cooling systems are selected for worst-case conditions, which rarely occur; instead, cooling fluid flow and fan speed can be varied to meet ever-changing demand, Gunderson said. This provides a constant source of cooling fluid and saves energy — at the rate equal to the cube of the speed reduction. So, just a small decrease in speed can save a good deal of energy.
Over the last several years, "the cost of the components that control the speed has come down and the reliability has improved," Gunderson said. "Older systems can even be retrofitted with variable speed control devices."
Advantage Engineering's variable-speed drives for cooling system pumps include a controller that adjusts the speed of the pump motor to maintain a constant line pressure. As the line pressure increases due to the closing of mold-temperature-controller cooling valves, heat-exchanger valves or chiller-condenser valves, the demand for water flow decreases. Then, the drive control slows the motor speed to reduce flow and pressure. When line pressure decreases below the set point (caused by valves opening), the drive control increases the motor speed to increase the flow rate and pressure
Phil Britt, correspondent
For more information
Advantage Engineering Inc.,Greenwood, Ind., 317-887-0729, www.advantageengineering.com
Frigel North America,East Dundee, Ill., 847-540-0160, www.frigel.com
Green Box America Inc.,Schaumburg, Ill., 630-616-5400, www.greenboxamerica.com
Thermal Care Inc.,Niles, Ill., 847-966-2260, www.thermalcare.com
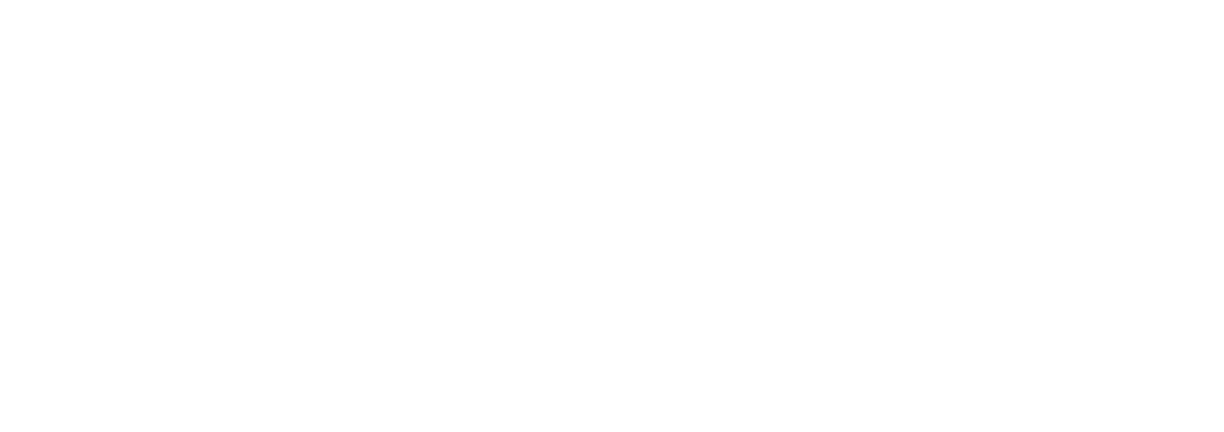