Makers of extruders and extrusion blow molding machines are offering energy-recovery technologies to capture and reuse heat, or turn mechanical energy into electricity.
Gneuss
Gneuss Kunststofftechnik GmbH last year worked with a customer to develop a system in which heat from a Gneuss MRS extruder was captured and transferred to the hopper. This reduced the required power and heat to melt the material in the extruder and resulted in lower overall energy consumption.
"It's really very simple," said Monika Gneuss, VP and sales and marketing manager for Gneuss Inc. "It's really just some metal piping that moves the hot air from the extruder back to the hopper. There is a lot of heat generated in the extruder."
Blowers on the outside of the extruder, which are needed to control the temperature of the unit, force the heated air into the hopper, where the resin is heated before falling into the extruder.
"What we have seen is we can run higher throughputs by doing this," Gneuss said. "We haven't been measuring savings in energy, but we have seen throughput increases of 10 to 15 percent. It's very considerable."
The results were so successful, the company is offering the system to other customers and plans to begin quantifying the energy savings. In addition, it is looking at tweaking the technology to offer greater control over the amount of heat being returned to the hopper.
The next steps are to engineer primary and secondary airflows by using additional blowers, a heat exchanger and controls to better regulate the conditions of the resin in the hopper, including temperature and volume flows.
Gneuss said the company is pleased with the results so far, but wants to learn more. "We are excited, but it needs to be explored a little bit further and be quantifiable so we can say more in detail what effect it has and what to expect," she said.
Battenfeld-Cincinnati
As an option, Battenfeld-Cincinnati offers a Green Pipe system for polyolefin pipe production that encompasses energy-recovery and energy-savings technologies.
The energy-recovery portion of the system is part of what the company calls its Efficient Air Cooling, or EAC, system. It is an internal pipe-cooling system in which ambient air flows through the pipe against the direction of extrusion and cools the pipe evenly from the inside.
Exhaust air from the internal pipe cooling can be used for heating and drying resin pellets before they are introduced into the extruder, saving energy.
Battenfeld-Cincinnati, together with Labotek A/S, Frederikssund, Denmark, have developed a method of reclaiming the heated air and using it for warming and drying HDPE; throughputs range from about 3,300 pounds per hour to about 5,500 pounds per hour. Energy savings of as much as 88 percent are possible using the technology.
The warm exhaust air from the EAC pipe head is sucked by a ventilator past a filter and into the Labotek system. There, the resin is heated and dried by warm air.
The EAC system is built into the Helix II VSI-T and VSI-T+ pipe heads. With the EAC system, the length of the cooling section can be shortened by 30 percent to 50 percent. The EAC system also improves pipe quality by significantly reducing sagging, especially in large-diameter pipes, and pipe geometry and roundness are improved, according to the company.
EAC can be used for PE and PP pipes with diameters from about 2.5 inches to 102 inches and wall thicknesses of up to about 4 inches.
Rex Materials Group
Rex Materials Group sells its TCS, or Thermal Control Solution, product as a system of efficient band heaters for extruders and injection molding machines that can reduce energy consumption and improve processing consistency. However, some extrusion customers also are using the bands to recover and reuse energy.
The TCS system replaces inefficient, traditional band heaters with thermally insulated radiant heating elements embedded in high-temperature insulation. The system directs heat into the melt and minimizes heat that escapes into the atmosphere, according to the company.
The system reduces barrel heater energy consumption by an average of 40 percent compared to traditional band heaters, according to the company. It also reduces air-conditioning requirements in climate-controlled environments.
TCS offers an optional, unique cooling system designed to pull high-velocity air directly over the surface of the barrel, removing excess heat, and releasing the heat where desired.
"We have had customers use TCS to both heat the incoming melt and pull the heat from the zones closest to the die to preheat the resin," said Ken Van Nimwegen, global sales manager. "Our standard cooling system very specifically pulls the air, rather than pushing it, so it can be exhausted where desired. This makes reclaiming the heat very easy."
While most customers release the heat outside the plant, two of Rex Materials' customers — one in the U.S. and one in South Korea — have used the captured heat to warm resin before it goes into the extruder, Van Nimwegen said. Preheating the resin reduces the heat needed to extrude the plastic and increases throughput.
In addition, Rex Materials is working with a distributer in Germany that is developing technology to pump the reclaimed heat into a dryer.
Kautex Maschinenbau
Kautex Maschinenbau incorporates energy-recovery technology in all its KBB all-electric extrusion blow molding machines.
This energy recovery involves generating electricity from the machines' high-speed movements. This occurs during the dry-cycle phase of operations rather than as the plastic is extruded.
"Where you get the energy back is that all the movements are done with motors that turn themselves into generators when they are in their braking phase," said Chuck Flammer, VP of sales for North America. "So, when you are moving your clamp back and forth at high speed, when you are trying to slow it down, your motor becomes a generator."
Energy also is generated when motors brake the blow-pin movements and the bobbing of the extruder platform frame, Flammer said.
The energy is then fed back into powering the machine or into the power grid.
"The amount of energy recovered depends on the types of bottles you are making," Flammer said. "If you are making small bottles with quick cycle times that require lots of motions, that will get more of your energy back. The faster the speed of the machine, the more energy that will be recovered. So, if you have a large container that has a longer cycle time, your energy savings is not as significant."
In testing, Kautex found that its equipment on some very small containers was recouping as much as 42 percent of the spent energy. The company did a direct comparison of a hydraulic machine to a comparably sized electric machine to achieve this total energy value by running the same bottles. When producing larger containers, however, the energy recovery was significantly less.
Flammer said Kautex is the only company he is aware of that recovers energy from extrusion blow molding machines.
"In a lot of cases, they take the energy and they just use it into a braking resistor," he said. "That will allow them to slow the machine down with the motors, but they are not capturing the energy. They are just basically releasing it as heat."
Kautex began introducing energy-recovery technology in its electric extrusion blow molding machines in 2013, and it most recently introduced it into two larger machines, the KBB 200 and KBB 400 models, in October.
The company developed those models specifically for manufacturing stackable liquid containers that can hold up to 35 liters.
Bruce Geiselman, senior staff reporter
bgeiselman@plasticsmachinerymagazine.com
For more information
Battenfeld-Cincinnati USA,McPherson, Kan., 620-241-6843, www.battenfeld-cincinnati.com
Gneuss Inc.,Matthews, N.C., 704-841-7251, www.gneuss.com
Kautex Machines Inc.,North Branch, N.J., 908-252-9350, www.kautex-group.com
Rex Materials Inc.,Howell, Mich., 517-223-3787, www.rexmaterials.com
Bruce Geiselman | Senior Staff Reporter
Senior Staff Reporter Bruce Geiselman covers extrusion, blow molding, additive manufacturing, automation and end markets including automotive and packaging. He also writes features, including In Other Words and Problem Solved, for Plastics Machinery & Manufacturing, Plastics Recycling and The Journal of Blow Molding. He has extensive experience in daily and magazine journalism.
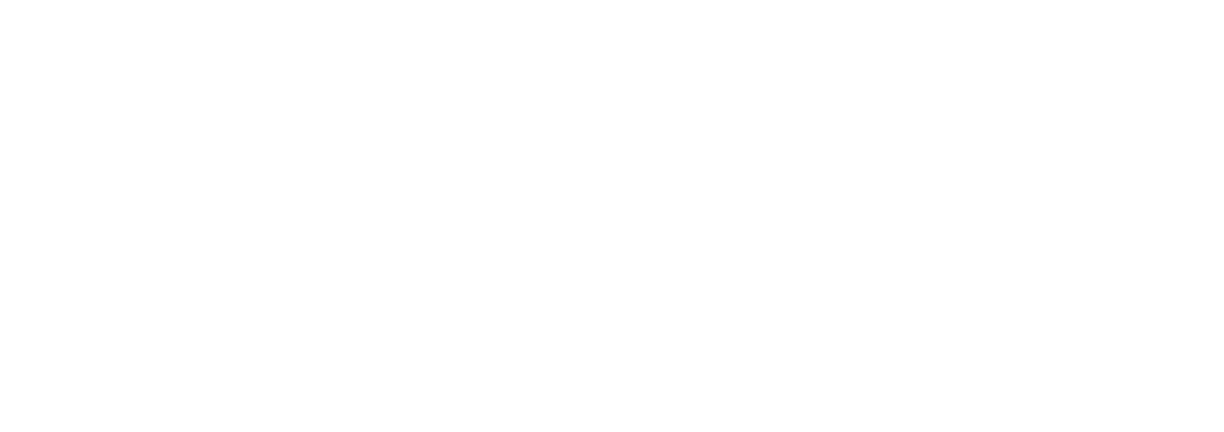