Whenever a business tries something new, it involves an element of risk. No matter how much a company researches and does its due diligence, breaking away from the norm always requires a leap of faith.
That leap of faith has brought two companies together recently — one in America and one based in Italy.
As Magic MP SpA of Monza works to expand its presence in the U.S., opening a showroom of its blow molding machinery this summer in Ann Arbor, Mich., New York processor Currier Plastics is experiencing an influx of new business, thanks to the equipment.
Currier, which purchased its first all-electric blow molding machine in 2015, recently commissioned new ME-L5/D models from Magic. With a clamping force of 13.4 tons and a mold stack height of 5.2 inches per mold half, the machines represent Currier's first Magic units. They have an opening stroke of about 9.8 inches and a 2-second dry cycle.
"The decision to go with Magic had more to do with delivery time and upfront cost, as well as the compatibility with our current medium-size extrusion blow molding [EBM] machines," said Ron Ringleben, VP of business development.
Magic offers eight models in its ME Line, including machines with up to 22.3 tons of clamping force. Extrusion heads are available for monolayer production as well as coextrusion of up to four layers.
Staying on the cutting edge
In October 2016, Currier sent a team to the K show in Germany to see what manufacturers from around the world had to offer. "We had representatives from our production, engineering and maintenance departments, and they had a common goal: to learn new technological advancements and who is doing them well," Ringleben said.
The blow molding engineering team members were searching for machines to use in Currier's medium-sized extrusion blow molding cell. As they studied the options, they had a list of criteria and requirements:
• cost,
• U.S. support,
• compatibility with the existing machine platform,
• compact footprint, and
• stability and experience.
Currier specializes in markets that require high volume and product precision, so the company "needed more of this size machine to support our growing business in the medical and consumer care markets," Steve Crawford, Currier's blow molding engineering manager, said of the decision to go with Magic equipment.
The company works hard to stay up-to-date with the most modern technology, especially because it is one of only a handful of U.S. companies that handle product design, injection molding and blow molding in-house.
"These new machines are significant to our market growth plans," Ringleben said. "Our customers new and old have come to rely on us for having industry-leading technologies."
As Currier focuses more of its attention on markets that require sanitary or clean-room molding, it makes sense to start adding all-electric machines. "The growth markets we are expanding in include medical, food and beverage and personal care," Ringleben said.
Currier prefers the all-electric platform to hydraulic machines for several reasons, including:
• repeatability of movement,
• cleanliness and greater level of environmental friendliness,
• quiet operation,
• reliability,
• reduced maintenance needs.
"These machines are built tough," said Jason Kelley, Currier's blow molding maintenance team member.
According to Pietro Spiga , who works in technical sales for Magic, the company sees great potential in the U.S. market. "The enormity of the U.S. market has opened new opportunities for Magic, [which] hopes to be able to offer the best experience for our customers and … the best support to their needs, creating a 100-percent customizable machine."
A minimally disruptive option
One of the most attractive aspects of the Magic equipment, and one that helped drive the decision to go with the Italian manufacturer, is that it was compatible with so much of Currier's existing equipment.
"The Magic machines by design will give us more machine capacity because we can use our existing molds, heads and secondary automation," Crawford said.
The Magic machines have the ability to make extrusion blow molded bottles and containers that are the same size as the ones produced by Currier's existing machines in that same EBM cell, so all of the machinery is able to share components such as heads.
"The center distance of the head determines cavitation of the molds," Ringleben said. "We have determined the best scenario of head and mold cavitation to meet our client's annual volumes based on years of experience. This means we can mold our client's custom containers in any of the machines without hesitation.
"We are using a common center distance to our existing platform so we can have more flexibility," he said. "The machine footprint is approximately 14 feet by 16 feet, so it meets our size requirements. The cycle time varies depending on the product. The machines in this cell have a range with a sweet spot of 1 ounce to 64 ounces, depending on the geometry."
Currier developed secondary automation that includes a take-out system that orients each bottle to an upright position before it reaches the leak-testing and vision inspection systems.
"The secondary automation we developed to support our current clients is added to new programs as well," Ringleben said. "This could include leak testing and vision inspection, both of which are important to verify product specifications. Important measurements for bottles include the neck dimensions and verifying ... tails are properly removed.
"The cameras today are sophisticated enough to detect the presence of flash and blow-ins, which is important to detect early so the process can be adjusted prior to the bottle going into the box," he said.
Michael T. McCue, copy editor
For more information
Currier Plastics Inc.,Auburn, N.Y., 315-255-1779, www.currierplastics.com
Magic MP SpA,Monza, Italy, 39-0392-301096, www.magicmp.it/en
Andrea Grandi is new GM of Sacmi Group
Plastics Hall of Fame seeks nominees
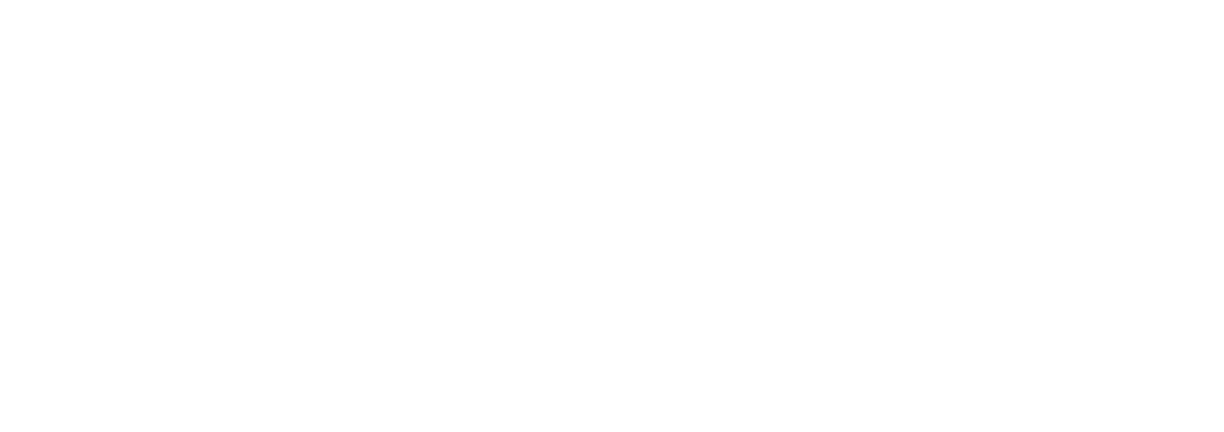