Coating suppliers are turning to some recent innovations to extend the life of plasticizing components. The new approaches include using a higher-performing tungsten-carbide coating and combining coating types.
NEW TUNGSTEN-CARBIDE COATING INCREASES UPTIME
Nordson Corp.'s Xaloy MPX, a new nanoparticle-based tungsten-carbide coating, resists wear and abrasion better than standard tungsten-carbide coatings that are applied through a high-velocity oxygen fuel (HVOF) thermal spray.
The Xaloy MPX thermal spray coating, introduced at the K show, is suited for use with single and twin plasticizing screws and can be applied to the entire screw or to specific areas, said Mark Colella, global product manager for Nordson's Xaloy brand. The coating also can be used to protect valves.
The shape, density and minute size of the particles in the coating improve its resistance to wear and abrasion. The coating, composed primarily of tungsten carbide, is produced in a controlled plasma process that yields uniform, spherical particles that are 5 microns in diameter.
"The particles are six to seven times smaller than those in standard HVOF coatings and are more densely packed together, owing to the uniform spherical shape of each particle," Colella said.
This allows the coating to be applied to a surface at a higher velocity. "This results in a stronger bond with the substrate metal," he said.
The coating is less porous than standard coatings. Nordson recommends using the MPX screw coating in conjunction with its Xaloy X-800 nickel/tungsten-carbide alloy for barrel lining, or a comparable barrel inlay.
Nordson spent two years developing the thermal spray coating, which extends the life of plasticizing screws processing halogenated materials such as flame retardants and PVC, as well as compounds containing 15 to 35 percent loadings of glass, carbon fiber or calcium carbonate.
Compared to a standard HVOF tungsten-carbide coating, Nordson said Xaloy MPX exhibits 8.5 percent greater bond strength in ASTM C633 bond testing, 61 percent less mass loss under ASTM G65 abrasion testing, and 18 percent less mass loss in ASTM G77 sliding testing. This extends the life of the plasticizing screws, Colella said.
CONSIDER COMBO COATINGS
Bodycote K-Tech says its Tech 17 chromium-oxide ceramic coating can be combined with an HVOF thermal spray coating for enhanced protection of plasticizing components.
"New uses for existing coatings are being driven by increasingly demanding end-user applications. Molders are processing different types of polymers to make different types of components," senior GM Jeff Carr said.
Molders are seeking different coatings to protect their equipment from premature wear and produce high-quality products with low scrap rates. Challenges include higher loadings for filled materials, engineering resins that are more sensitive to shear and unusual material formulations.
"Many of the applications are hush-hush. The molder may only tell us what the characteristics of the material are and how processing it is affecting their equipment. We then look at our products and determine a solution suitable for the application, based on what we know," Carr said.
Bodycote has an HVOF thermal spray operation in Houston, which primarily serves clients in the oil and gas sector, but is working with that division to find ways to use both the HVOF formulation and the Tech 17 coating.
Tech 17 is a refractory-coating formulation that seals chrome-plated screws that are used to process chlorinated resins. The coating is applied to a metal substrate, then the coated product is subject to a firing process to remove water, which oxidizes the material and starts a chemical reaction that creates a bond with the metal substrate and the chrome plating. The coating is drawn into the microcracks and pores of the chrome plating through capillary action.
The chromium-oxide ceramic combines with the chrome plating to create a very hard, corrosion-resistant coating that exhibits increased bond strength.Last year, Bodycote started using Tech 17 for components that process noncorrosive materials. The company discovered that its coating allows users processing nonchlorinated materials to purge the plasticizing screws more quickly.
Bodycote is investigating additional uses for its Tech 12 formulation, designed for application to bare metal, and its Tech 23 coating, which is formulated for use with stainless steels and some tool steels.
Mikell Knights, senior staff reporter
For more information
Bodycote K-Tech Inc.,Hot Springs, Ark., 501-760-1696, www.bodycote.com
Nordson Corp.,New Castle, Pa., 724-656-5600, www.nordsonpolymerprocessing.com
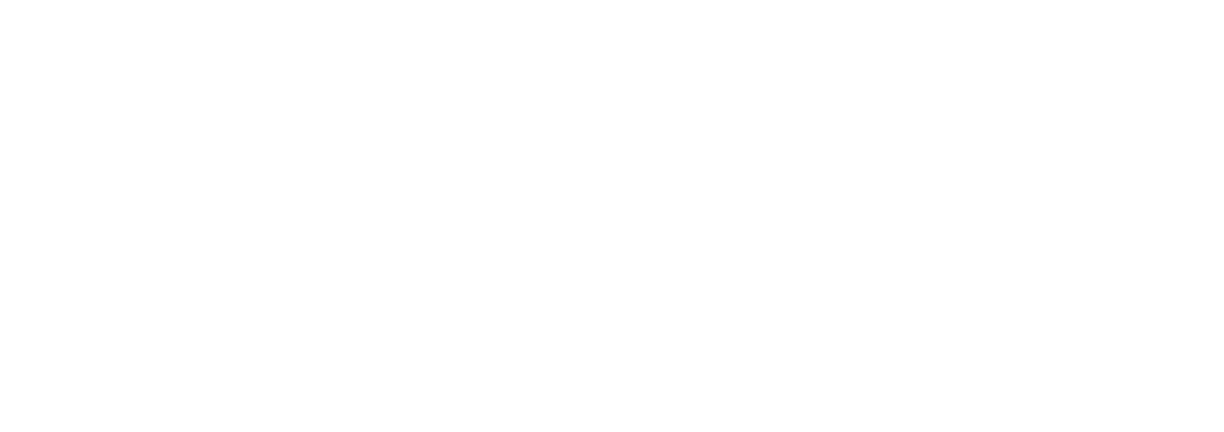