Special Report: High-tech alternatives for extrusion die cleaning
Regular cleaning of plastic extrusion dies and inspection for damage is necessary to ensure the quality of products, reduce scrap and extend the life of the die.
In a document that Nordson Extrusion Dies provides to its customers, the company advises disassembling flat extrusion dies at least once a year. The purpose of the procedure is to remove polymer buildup from the flow surface inside the die, lubricate moving parts and inspect the die for possible damage.
Manually cleaning a die involves workers using abrasive pads, copper gauze, brass scrapers and die soap or another cleaning agent.
Nordson sells die-cleaning kits. The company also sells an EDI Ultracart System, which streamlines cleaning procedures by allowing die halves to be easily rotated to access flow surfaces. The cart can be wheeled to the processing line for offloading of the die and moved to a work area for die cleaning and maintenance. Nordson says its carts enhance worker safety, reduce downtime, simplify die disassembly and reassembly, and help prevent costly damage to critical die surfaces during maintenance.
Many companies offer alternatives to hand cleaning of dies. Accurate Thermal Systems, Dinamec Systems and Omegasonics have introduced upgrades to their fluidized cleaning systems. Cold Jet supplies dry-ice blasting equipment, while Polymer Cleaning Technology (PCT) is moving into the extrusion die cleaning market with a new oven. In addition, extruder supplier Entek has updated a die specially made for easier cleaning.
Fluidized baths
In late 2016, Accurate Thermal introduced a new fluidized temperature bath called the FTBLL12W for cleaning midsize breaker plates and dies.
The bath is larger than the standard FTBLL12. The new FTBLL12W can accommodate larger dies and parts. The tank has a diameter of 12.4 inches and a depth of 13 inches.
"The addition of the FTBLL12W allows customers to better control their purchasing budget and acquire just the right amount of cleaning area without stepping up to a much larger bath costing 50 percent more," sales manager Walter Combs said. "We have assisted a number of customers needing a more affordable 'middle-ground' tool cleaner."
Accurate Thermal's fluidized baths use heated aluminum oxide for cleaning, which reduces the risk of damage to parts.
"It's not abrasive," Combs said. "You use aluminum oxide because it is a particle size that has wonderful heat-retention capabilities. We put that in motion. You get the equivalent of a boiling pot of water. Particles gently flow up and over the surface area, which causes the plastic to melt, and you'll soon be back down to bare metal."The alternative is guys are out there with torches and lathes and wire wheels, you name it. We're the guys that really try to keep them from tossing so much stuff into the junk box," he said.
With some systems, a worker needs to tend the bath to adjust the airflow as it heats up to prevent the particles from overflowing the tank, much like water might boil over.
Accurate Thermal's fluidized temperature baths have automatic fluidizing air control, so the operator does not need to monitor the bath airflow and make constant manual air adjustments as the bath heats up, freeing the operator to perform other duties and improving worker efficiency.
Fluidized Sand Bed
Dinamec Systems provides fluidized silica sand-bed cleaning systems for extrusion dies.
Dinamec Systems' newest fluidized sand bed, the E-model, is a labor-free tool-cleaning system with a smaller footprint and a lower ceiling height. The company began selling the model in November.
The new E-model fits in tight places. Its new design provides a totally enclosed environment during loading and unloading in the fluidized sand bed, guaranteeing no emissions escape during this process.
Cleaning cycles in the new E-model fluidized bed are short, typically an hour or two.
The system offers maintenance staff a safe and clean environment to thermally clean dies, screws, breaker plates and tooling.
The model comes with a patent-pending internal loading platform that allows users to easily customize how tools enter the system for cleaning. For example, tooling can be loaded with or without a basket, using an external hoist system or a direct robot loader.
Ultrasonic Cleaner
Omegasonics makes ultrasonic machines that can be used for cleaning extrusion dies.
Last June, the company introduced its Omegasonics Powerlift 4500 series that adds a lift table to the ultrasonic tank. The units are equipped with pneumatic lifting platforms that move components, including extrusion dies, in and out of the cleaning tanks safely and easily.
The platforms eliminate the need for an overhead crane for this procedure, President Frank Pedeflous said.
"The lift table allows the operator to put the [tooling] onto a platform, press a button, and now the platform lowers into the tank and you set the cleaning cycle. It adds the extra convenience of not having to use an overhead crane," he said.
Lifting pistons are inside each unit's cleaning bath. Three models currently are available, with the largest tank holding 264 gallons. The lift table can handle up to 1,500 pounds, and its platform measures 60 inches by 28 inches.
Dies and molds can be disassembled and placed in the ultrasonic tanks for cleaning.
The tanks use an ultrasound transducer to generate sound waves higher than the frequency detectable by humans. The ultrasonic waves cause water molecules to vibrate rapidly, resulting in cavitation bubbles. The bubbles, as they burst, agitate and remove even tiny particles and substances from the extrusion dies.
The tanks, which can heat water to about 165 degrees, use this energy, along with soap, to clean small areas in the dies more efficiently and more thoroughly than manual cleaning, according to Pedeflous.
Dry Ice
Cold Jet develops and sells dry ice cleaning equipment for the plastics industry, among others. Using dry ice to clean is faster and easier and doesn't generate additional waste, said Steve Wilson, the company's director of global business development for plastics, rubber and composites.
The company's roots in the plastics industry began with equipment designed for cleaning injection molding equipment. However, the company two to three years ago also turned its attention toward the needs of the extrusion industry. About 18 months ago, the company introduced its model Aero 40FP, which is designed for extrusion die cleaning needs.
The Aero 40FP uses 3mm dry ice pellets for cleaning because extrusion equipment needs larger pellets that create more kinetic energy for cleaning than is required for cleaning injection molds.
"It throws more rice-size particles, whereas the one used in molding throws sugar-size particles," Wilson said. "The 3mm pellets create more kinetic energy; that's the difference."
The Aero 40FP offers higher pressures — up to 300 pounds per square inch — than previous models used for cleaning extrusion dies. In addition, the pressure now can be adjusted and newer nozzle designs can reduce the dry ice particle size if needed. In certain instances, when working with aluminum tooling, for example, an operator might want to reduce the application pressure and size of the pellets to reduce the risk of damage to the softer metal.
The dies can be opened and cleaned while in place and still hot.
"You open it up right on the line and clean it," he said. "There's usually a hinge. You unbolt one side, and you rock it back on a hinge. You clean both halves and you close it. That's the beauty of dry ice: You clean it in place … It's a nonabrasive way to clean. It keeps things dry. There are no chemicals and no sand or soda to clean up."
Wilson uses the acronym ICE — for impact, cold, expansion — to describe the dry ice cleaning method.
The impact of the dry ice particles moving at 800 to 1,000 feet per second is responsible for most of the cleaning action. However, cold from the pellets, which come out at minus 109 degrees Fahrenheit, causes the plastic residue on the extrusion dies and tools to shrink and lose its bond on the metal. Finally, expansion that occurs as the dry ice hits the hot metal and turns to gas helps dislodge the plastic residue.
"You crack it, you shrink it, and you blow it off the surface," Wilson said.
In addition to cleaning extrusion dies, the Aero 40FP can clean sizing rings and collapsing towers used in blown film lines.
Pyrolysis oven
PCT may be best known as a provider of parts, refurbishment, service and cleaning for hot-runner systems used in injection molding.
However, the company is branching out by offering a new method for cleaning blown film extrusion dies.
The company is adapting technology it uses to clean internal hot-runner manifold systems to help extrusion customers.
"We started working about a year ago with one client in particular, and we have done several cleanings," PCT President Robert Duffy said. "We've been setting up a process cycle with them, and we're now ready to introduce this."
PCT's process uses a specially configured pyrolysis oven for cleaning blown film dies in their fully assembled condition.
The process works regardless of the number of film layers the die is designed to accommodate, Duffy said.
The conventional approach involves heating up a blown film die while it is full of plastic. Technicians then disassemble the die layer by layer. This process is time-consuming and can cause damage to the die surface. In addition, the individual die segments need to be hand cleaned after disassembly, adding more labor hours.
PCT's process involves slowly heating a pyrolysis oven containing the fully assembled die. The oven, designed to prevent the presence of oxygen during the cleaning process, ensures there is no overheating or damage to the die.
The lack of oxygen prevents the plastic in the die from combusting. The process generally takes less than 24 hours. After the die is cleaned, the individual segments are easily disassembled, Duffy said.
"The process has several advantages," Duffy said. "It significantly reduces the risk of damage to the die during disassembly, it eliminates a large amount of the labor required to clean a die, and a final advantage is the quality of the cleaning."
Blown film dies have intricate flow paths, and removing all plastic and carbon residue from them can be difficult, he said. The PCT process ensures that all residue in every portion of the die is removed.
PCT provides the cleaning service to customers on a contract basis. However, if a customer is interested, Duffy said his company could sell the technology and provide the training.
Die design
Entek, a maker of twin-screw co-rotating extruders, has made available its QC3 strand die designed for simplified cleaning and maintenance.
To allow for a quicker changeover, Entek now is supplying duplicates of the die plate and hard-to-clean die parts — pieces with small flow paths. The new design means a clean set of the hard-to-clean parts can always be on hand, allowing additional time for the dirty set to be cleaned without holding up production.
In addition, the new die design means no sensors, heaters or burst plugs need to be removed because they stay with the extruder. Traditionally, such parts needed to be disconnected or removed.
All bolts are the same size in the new design, allowing pieces to be quickly removed and replaced with the help of an air ratchet. In addition, sealing surfaces are flat and easy to scrape with a putty knife or similar tool.
For cleaning, the die goes into an oven to remove resin, then is replaced so the machine can be put back into service.
The QC3 die allows for considerable time savings because the design allows parts, including the breaker plate, die body and die plate, to be easily removed and replaced.
"With the QC3 die, the processor has options," Entek design engineer Melissa Jensen-Morgan said. "They can remove the entire unit as one piece and put it in the oven for cleaning, or they can disassemble the unit and access only the specific parts they want to clean. Also, this design prolongs the life of the heaters and sensors since they don't need to be regularly connected and disconnected."
Bruce Geiselman, senior staff reporter
For more information:
Accurate Thermal Systems LLC,Hainesport, N.J., 609-326-3190, www.accuthermal.com
Cold Jet LLC,Loveland, Ohio, 513-831-3211, www.coldjet.com
Dinamec Systems LLC,Acworth, Ga., 770-421-1181, www.dinamecsystems.com
Entek Extruders,Lebanon, Ore., 541-259-1068, www.entek.com
Nordson Extrusion Dies Industries LLC,Chippewa Falls, Wis., 715-726-1201, www.extrusiondies.com
Omegasonics,Simi Valley, Calif., 888-989-5560, www.omegasonics.com
Polymer Cleaning Technology Inc.,Hillsborough, N.J., 908-281-0055, www.polymercleaning.com
Bruce Geiselman | Senior Staff Reporter
Senior Staff Reporter Bruce Geiselman covers extrusion, blow molding, additive manufacturing, automation and end markets including automotive and packaging. He also writes features, including In Other Words and Problem Solved, for Plastics Machinery & Manufacturing, Plastics Recycling and The Journal of Blow Molding. He has extensive experience in daily and magazine journalism.
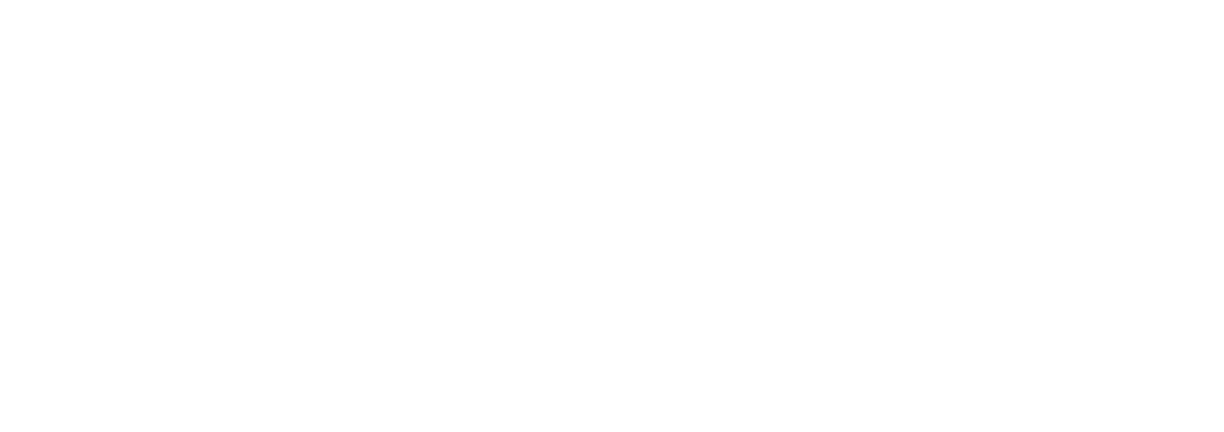