Demand for lighter, complex and thermally tolerant ducting for new auto engine designs is heating up the suction blow molding industry.
The parison suction process, which efficiently produces convoluted ducts, debuted more than 30 years ago, but interest is growing rapidly because of better equipment and new high-heat engineering resins developed for compact turbocharged engines.
Suction blow molding machines, such as those made by Uniloy, Kautex and S.T. Soffiaggio Tecnica, can create ducts with sophisticated shapes that cannot be achieved by other processes. Some machine suppliers have made recent upgrades. And while traditional extrusion blow molding machines can be retrofitted to perform suction blow molding, demand for dedicated machinery is growing.
"System suppliers are searching to produce the ducts in one material, using a single process step, because the standard practice is to assemble separate elements in hard thermoplastics or metal and soft thermosetting rubbers," said Mauro Riccio, Uniloy's global product manager of industrial applications.
An example of complicated blow molded metal-replacement parts is a turbo compressor outlet duct made for the 2017 Alfa Romeo Giulia sedan by the ABC Group, a Toronto automotive parts manufacturer. Compared to a metal version, it is 30 to 40 percent lighter, with a cost reduction of 20 to 25 percent, according to the SPE Automotive Division. The part was a finalist in the division's most recent design competition. Thanks to newly developed engineering resins, the part can withstand continuous-use temperatures as high as 428 degrees Fahrenheit and pressures as high as 30 pounds per square inch.
Overall, using higher-grade materials, the suction blow molding process can achieve cost reductions of 50 percent and weight reductions of 40 percent, compared to parts made in other ways.
S.T. Soffiaggio Tecnica
S.T. Soffiaggio Tecnica technology reflects an industry trend toward using engineering plastics. Across the industry, examples include polyphenylene sulfide, polyamide 66 and polybutylene terephthalate.
The company's latest suction blow molding machine, the ASPI 150.3, is especially adept at making parts for the air-induction systems of turbocharged engines. Parts made by the energy-efficient machine exhibit uniform wall thickness and no seam lines.
"The major technical advances performed by S.T. have been in the dynamic control of the parison thickness," said Marco Solinas, senior global product manager for the Monza, Italy, firm. "Optimizing the wall thickness of the blow molded item means minimizing the weight and the use of expensive engineering resin."
The third-generation machine offers larger platens (35.4 inches wide by 43.3 inches high) that can accommodate molds up to 63 inches long. It boasts patent-pending innovations in the measurement of the parison diameter and uses a dot-printing technique to achieve optimal registration of the parison during extrusion. The technique allows for the printing of characters and text.
"Those innovations help the customers both in tuning the process and in maintaining it within the set processing window, resulting in higher quality of the blow molded items and less rejects," Solinas said.
A new Smart Heating Control prevents power surges that can occur, for instance, when a plant heats up numerous machines at once after a holiday.
In addition to the ASPI 150.3, S.T. plans to introduce a new double-cavity machine for customers and markets requiring higher production capacity.Last year, DuPont installed a $1.1 million S.T. suction blow molding machine at its technical center at Meyrin, Switzerland, for the development of blow molded air ducts.
In the U.S., Hollo Plastics Equipment represents S.T.
Kautex
Kautex, which describes itself as the market leader for suction blow molding equipment, says the process requires less resin and clamping force than conventional blow molding and uses less-expensive tooling. A vacuum sucks the parison into a pipe-shaped mold cavity. Parts do not have compression seams, meaning they're stronger, and they have even wall thicknesses.
While the turbocharging trend has been strongest in Europe and Asia, it is gaining ground in North America.
"The global market for turbocharged vehicles is expected to grow from 20 [million] to 40 million in the next three or four years as engines become smaller," said Bill Farrant, president of Kautex Machines Inc.
At the K show, Kautex introduced the KSB10, a new suction blow molding machine. "Because it's dedicated, the machine footprint is reduced by 50 percent," Farrant said.
Machine features include an efficient servo-hydraulic system and a radial wall distribution system (RWDS) that allows the tooling to move radially to the axis of the die head. "We use it to not have the parison kink in the elbows of the mold and make the part a lighter weight with the same mechanical characteristics," said Chuck Flammer, Kautex VP of sales.
The extruder die-head platform is adjustable in three directions. It can achieve up to 10 tons of clamping force and can be configured with one or two stations. The KSB10 can be fitted with conveyors or robots.
Uniloy
As a division of Milacron, Uniloy can take advantage of its expertise in other areas of plastics, Riccio said.
"The big difference that Milacron has, compared with other competitors, is the possibility to integrate all the solutions used for high-performance polymers in injection in the suction blow technology," Riccio said. "This is due to the fact that Milacron is the only group that has all the main technologies available."
Designed for making automotive and technical parts, Uniloy's suction blow molding machines are offered in 10 different machine models. Some of the models can handle sequential coextrusion, while others are made for single-resin processing. They have clamping forces from 12 tons up to 30 tons and can be configured with a single extruder or injector.
For more information
Hollo Plastics Equipment Inc.
Northfield, Ohio, 330-467-9595, www.holloplastics.com, www.st-blowmoulding.com
Kautex Machines Inc.
North Branch, N.J., 908-252-9350, www.kautex-group.com
Uniloy Americas,
Tecumseh, Mich., 517-424-8900, www.milacron.com
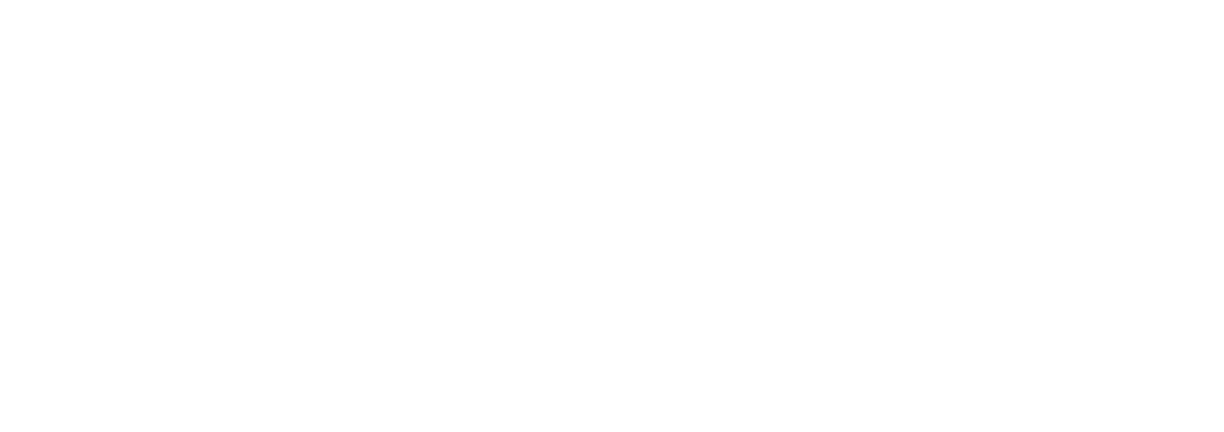