Laser-etching technology used on molds to create unique textures and designs in plastic products is making its move into the packaging market after leaving its mark in the automotive industry. Pushing it beyond automotive is the goal of Custom Etch Inc., New Castle, Pa., which specializes in texturing and engraving.
Consumers have seen the effects on products such as the 20-ounce Mountain Dew bottle. Though that bottle, called "Sidekick," was released to the market a few years ago, the design and texture portended a trend. The bottle has a grid design of squares wrapped around it. This design is approximately 0.007 inch deep and is perfectly aligned through the parting lines so characters meet evenly throughout.
It points to the trend of mass customization in packaging, says Gisbert Ledvon, director of business development with GF Machining Solutions LLC, Lincolnshire, Ill. Brand owners want the bottles to get to market faster and they want the bottles to be unique.
"Before consumers grab something from the shelf, they want to see something unique. If it's more appealing and more unique in the packaging, they're more likely to grab that," he says.
The primary goal with the design of that Mountain Dew bottle was shelf appeal and gripping ability. The advantages of laser-etching technology on such applications were the focus of a presentation given by Don Melonio, VP of Custom Etch, during the SPE Annual Blow Molding Conference held in October.
Custom Etch is the first company in the United States to invest in the Laser 4000 5Ax, a five-axis machine from GF Machining Solutions, says Ledvon. Custom Etch installed its first machine in 2014 and as of October, had commissioned its second machine of that size. This machine has X-, Y-, and Z-axis travel with speeds of 1,181 inches per minute (ipm), 1,181 ipm and 787.4 ipm, respectively. The working height over the floor is 5 feet 9 inches. The maximum workpiece dimensions are 98.42 inches by 59.05 inches by 35.43 inches.
Melonio said the technology is an alternative to photochemical texture etching, which is a manual, two-dimensional process. That laborious method involves disassembling molds and using acid to etch away the negative space of the pattern. The positive space of the design is left, raised above the negative portions. This process poses a lot of potential damage to tools. The chemicals used also require special disposal.
Take, for example, a 38,000-pound, 2+2 mold for an automotive lens. With photochemical etching, there would be a traditional masking process, then a manual pattern application and then acid etching. With laser etching, that same mold is loaded into the Laser 4000 machine fully assembled. The data for the pattern is loaded into the machine via CAD software and the pattern is imaged onto the surfaces; the design is laser-etched into the cavity surface.
"The accuracy is so much better," says Melonio. "You no longer have the human factor." The machine achieves accuracy down to the micron. Acid cannot etch away by degrees so the level of complexity that can be achieved via laser is much higher.
With the 3-D nature of plastic parts, an upgrade in the technology was necessary, says Melonio. On that Mountain Dew bottle, for example, the geometric grid runs around the bottle and through the parting lines of the mold. That grid would have been impossible to make with manual technology, says Melonio. On an order from Pepsi, more than 1,000 molds had to be built and textured within one year's time. With laser etching, multiple tools can be loaded and run at the same time. Also, texturing can be achieved across multiple materials, for example, a cavity made of P20 mold steel and aluminum bronze gate insert.
"That was the reason we started seeking out laser was to fulfill a Pepsi order," he says. "We never really intended to buy more than one machine. But it has blossomed from there."
Molds for bottles and similar packaging are laser-etched on an AgieCharmilles Laser 1000. Custom Etch also has a 600 and 1200. The numbers assigned to the machines indicate the X-axis travel in millimeters of the machine table. This February, Custom Etch will take delivery of another 1000. It is anticipating significant business from the beverage market within the next year. But Melonio also sees great potential in automotive lighting. The textured finishes act as diffusers of light and also as reflectors.
"We can put shapes and geometries into the mold to reposition the light as it goes into the plastic to change the way the light is being focused through the lens," he says.
The technology has been used most notably in the European automotive market on parts for vehicle interiors. In a project for BMW, for example, the carmaker wanted to differentiate its i3 electric car, specifically on the interior in parts like the dashboard. That project used textured molds to achieve a leather-like look from plastics. Mercedes was the first carmaker to use the technology to achieve grains that had only ever been produced via laser-engraved rolls. In North America, Ledvon believes the technology has great potential in the automotive market as well.
"We're just starting to tap into this market," he says. "The big OEMs, specifically in car manufacturing, the mold-making industry, they're just noticing this type of technology. More and more designers are demanding these type of textures. The designers always want to differentiate their products. Every manufacturing item you make and you want to bring to the consumer, the designer wants to set themselves apart as very distinguished. So far, there were a lot of limitations from a conventional approach to make textures and finishes on certain products."
The other markets where this technology can be applied include building and construction. The appearance of intricate wood grains can be accomplished via laser etching; therefore, makers of composite doors are finding it an attractive alternative for entry doors used in homes.
LASER ETCHING, ACID ETCHING NOT MUTUALLY EXCLUSIVE
If it makes sense in a particular application, the two technologies can be used together in what Melonio calls a hybrid laser-acid process. An example would be where the laser is used to remove photoresist — a tough film used for masking — prior to the acid etching of the mold. The mold then is masked again and acid etched using the traditional process. The hybrid process is considered for simpler, 2-D patterns, for example, blow-molded flower pots. Acid removes metal at a much faster rate than lasers. Multiple cavities can be in the acid bath at the same time, Melonio points out. There also is superior repeatability of pattern application versus manual printing. But there are also negative aspects to the process, including the increase in labor hours to apply resist and remove it post-acid etching. There is the possibility of staining or damaging to the high-polish areas and blasting is required in most cases.
Angie DeRosa, managing editor
Contact:
Custom Etch Inc., 724-652-7117, www.custometch.com
GF Machining Solutions LLC, 847-913-5300, www.gfms.com
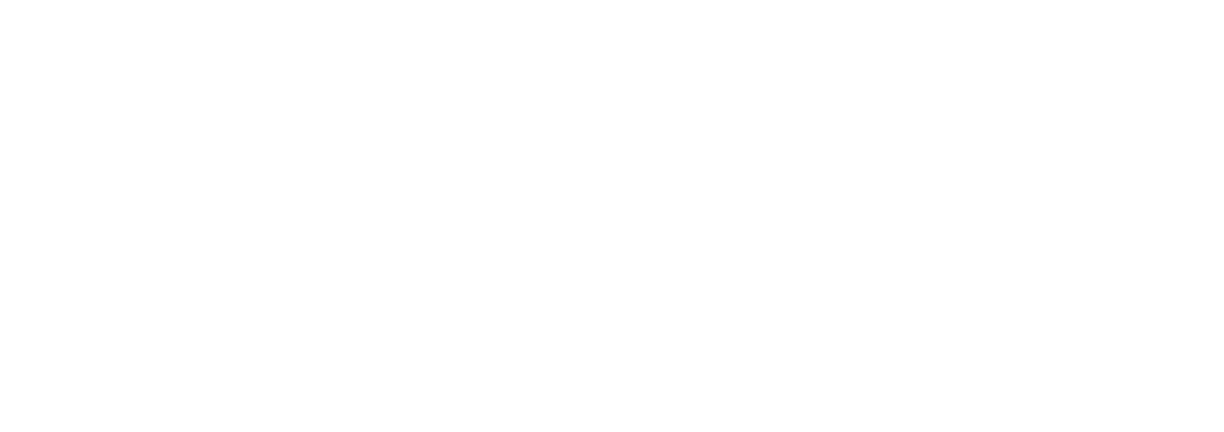