Special Report: Advanced mold water flow controls maintain temperatures
New styles of mold water flow controllers are designed to perform like an advanced temperature control unit (TCU) to achieve consistent cooling and quality parts.
Koziol GmbH, an injection molder in Erbach, Germany, reports that with this technology, the number of parts it rejected because of issues with mold temperature control was significantly reduced, from a high of 24 percent.
The monitoring and control of water flow rate, temperature and pressure into an injection mold ensures a uniform temperature across the entire mold surface.
TCUs consistently release water at a set temperature, flow rate and pressure for transfer to the mold. However, they are less likely to detect anomalies within the mold that can impact part quality, say sources from injection molding machinery makers Engel Machinery Inc., York, Pa., and Wittmann Battenfeld Inc., Torrington, Conn. To combat the problem, the companies have individually introduced advanced mold water flow-control technologies that bring automated monitoring and control to water distribution systems. Water flow regulators are installed after the TCU but before the mold, and are used to balance the temperature profile in the tool, a key parameter in the uniform molding of parts from cavity to cavity, cycle to cycle.
The companies say that for some applications, using a TCU by itself is not enough. Joachim Kragl, the director of advanced molding systems and processing for Engel North America, says TCUs reliably operate at the maximum flow rates and pressures to deliver an optimum cooling temperature. However, the fluid hydraulics may not perform as cited by the mold designer. In addition, the TCU doesn't indicate what the flow rate is in each cooling channel.
Buildup within the mold is another potential problem. Minerals such as calcium carbonate or impurities in the water, such as diluted solids, can be missed by a filter, and even a strainer in the TCU may fail to capture them. Rust and lime scale also can constrict cooling circuits. In addition, filters, kinked hoses, pump wear and fluctuations in the supply water pressure can negatively influence flow through a channel.
"Over time, the individual cooling channels in a mold can become constricted due to minerals or other elements within the water itself that are deposited within the cooling circuit," says Michael Stark, divisional manager for material handling and auxiliaries, Wittmann Battenfeld. "Increasing buildup can result in a degradation of water flow in a cooling circuit, which causes inadequate cooling to a molding cavity and leads to part quality problems, including sink marks, higher stresses and nonuniform shrinkage." Additionally, a restriction in one circuit causes the water to flow into another cooling circuit, impacting part quality in another cavity, says Stark.
Stark says injection molders sometimes fail to correctly diagnose the problems they're experiencing. "Injection molders in North America producing parts for automotive, packaging and medical industries often experience a buildup of deposits that cause molding problems and extend mold cycle times, yet many do not consider the mold water system as the culprit," says Stark. Often, the tool is returned to the mold shop and the metal is modified to balance the mold or the molder will adjust the process without investigating why a high-performance tool no longer runs well.
Temperatures and pressures throughout the tool can be different from circuit to circuit due to blockages or pressure issues. Even so, because the overall flow into the mold might be equal to the flow out of the mold, problems within the tool can go unrecognized. Stark says that molders may build or buy a simple, fixed manifold system that distributes cooling water to the individual channels, but those approaches provide no higher functionality.
Gaining control over the water within the manifold can lead to numerous benefits.
"Adjustable water manifold systems let the molder modify the water flow to always stay in the turbulent range, hence providing the best heat removal. The flow is matched to what the mold is designed for, and each cooling channel is monitored," says Kragl.
The flow valves in the water manifold system can open automatically when disturbances are detected, allowing the desired target value to once again be attained, says Kragl. Continuous monitoring and control using these new flow-control systems set them apart from prior iterations.
AUTOMATIC AND PRECISE WATER CONTROL FROM WITTMANN BATTENFELD
Wittmann Battenfeld launched its new Flowcon plus water flow controller, designed for automatic and precise adjustment of water flow rate and temperature, at Fakuma.
The Flowcon plus unit incorporates a proportional valve that is driven by a stepper motor to adjust the amount of water flow directed into each cooling circuit. The original Flowcon unit relied on solenoid valves which abruptly opened or closed the valves and did not allow for fine adjustment, says Stark.
Flowcon plus features 1.25-inch-diameter ports for main water supply and return connections (which handle the primary water supply from the TCU and return line from the mold). It has 0.375-inch ports that minimize pressure losses and ensure high water flow rates. Flowcon plus can be designed with two to 12 circuits, which can serve up to eight zones in a mold. Four Flowcon plus units, each serving 12 cooling circuits, can be tied through data cables to a single controller.
Each circuit has a stepper-motor-controlled proportional valve and can handle flow rates up to 4 gallons a minute. The unit allows for water flow to be matched to the dimensions of the mold cooling channels.
Flowcon plus can handle water temperatures up to 248 degrees Fahrenheit. The unit features a water flow sensor and a separate water temperature sensor integrated into the body of the unit, which is compact and is designed to be mounted onto the clamping unit of the injection press. The sensor technology detects fluctuations in pressure, flow or temperature.
Flowcon plus uses microprocessor control to adjust the proportional valves. It can maintain process parameters and temperatures to within 2 degrees Fahrenheit. The system signals an alarm if the water temperature exceeds a set limit.
Flowcon plus can be fully integrated into the machine control of a Wittmann Battenfeld injection press. Users also can set upper and lower limits for the temperature or flow of Flowcon plus using a stand-alone version, which features a 5.7-inch touch-screen display.
A key benefit of the automated valve adjustment is that monitoring and control data and set-up parameters can be archived and retrieved. In addition, since Flowcon plus operates as a closed loop system, it can quicken mold startups or validate a tool. "The programming can move with the mold and it can be adjusted at any time," says Stark.
Flowcon plus joins a family of water regulators, which include its Flowcon unit with plunger-type solenoid valves, and its Water Flow Control series of water controllers that feature manual adjustment of the valve. Wittmann Battenfeld says it has sold more than 600,000 flow regulators, primarily in Europe, making it the largest developer and manufacturer of water distribution systems for plastics processing. Stark says Flowcon plus is suited to any molder seeking a consistent process where cycle time is important and the molding project calls for long process runs.
AUTOMATIC AND ADJUSTABLE FLOW MONITORING FROM ENGEL
Since launching its Flow Monitoring System, or Engel flomo, in 2010, Engel has made numerous upgrades to its technology. The improvements include a new release at Fakuma.
Last year, Engel updated its technology with e-flomo, which incorporated electrical control valves onto the unit, allowing water flow rates to be fine-tuned and controlled in a fully automated process. Engel flomo manually adjusted the valves, while e-flomo automatically adjusts the flow rate in each cooling circuit. Users are able to shut off water delivery to the mold or to individual circuits if desired, and the incorporation of the control into the machine control allowed users to save recipes. Users can automatically set desired water flow rates, which correspond to an ideal mold temperature setting, at the start of a production run. That enables shorter mold set-up time and reaching a thermal balance quicker, says Kragl.
Engel's e-flomo uses flow and temperature sensors in the return supply line. Users can base control on the mold temperature and water flow rate, or the difference between the mold inlet water temperature and the mold outlet water temperature, or just on the return supply temperature. A temperature sensor directly on the water inlet allows e-flomo to monitor the supply water temperature coming from the mold TCU, says Kragl. Constant monitoring of these parameters in a closed-loop reduces scrap and reject parts, minimizes downtime and cleaning and increases molding machine availability. Engel's flow monitoring devices mount directly onto the mold platen, which allows for the use of shorter hoses from the device to the mold, minimizing pressure and heat losses.
The e-flomo units handle cooling media at temperatures up to 248 Fahrenheit and operating pressures up to 145 pounds per square inch. Engel flomo handles temperatures up to 194 Fahrenheit. Each unit can monitor and control between two and eight cooling circuits. Users can operate the e-flomo using Engel's CC300 or CC200 machine controls, or a stand-alone unit. Engel offers e-flomo in two models. One is capable of monitoring and controlling flow rates from 0.3 to 4 gallons a minute; the other can adjust water flow in a range of 3 to 10.5 gallons a minute. Both will signal an alarm if the flow rate moves outside of a set range. Molders can choose to stop the machine or keep producing parts after the alarm is triggered.
Molders with a multicomponent 2+2 cavity tool that wish to operate different sections of the tool at different temperatures would require separate e-flomo units because both zones cannot be served by a single e-flomo unit. Engel offers three versions of its mold manifold units, distinguished by the level of electrification. All three units use the same flow and temperature sensors.
At Fakuma, Engel released the product's newest development, e-flomo premium. It provides automatic machine-controller integrated control for all aspects of the unit, including the shut-off valves to the main water supply lines (using electrically driven ball valves). Engel says more than 2,500 e-flomo units are installed worldwide.
Mikell Knights, senior correspondent
Contact:
Engel Machinery Inc., 717-764-6818, www.engelglobal.com
Wittmann Battenfeld Inc., 860-496-9603, www.wittmann-group.com
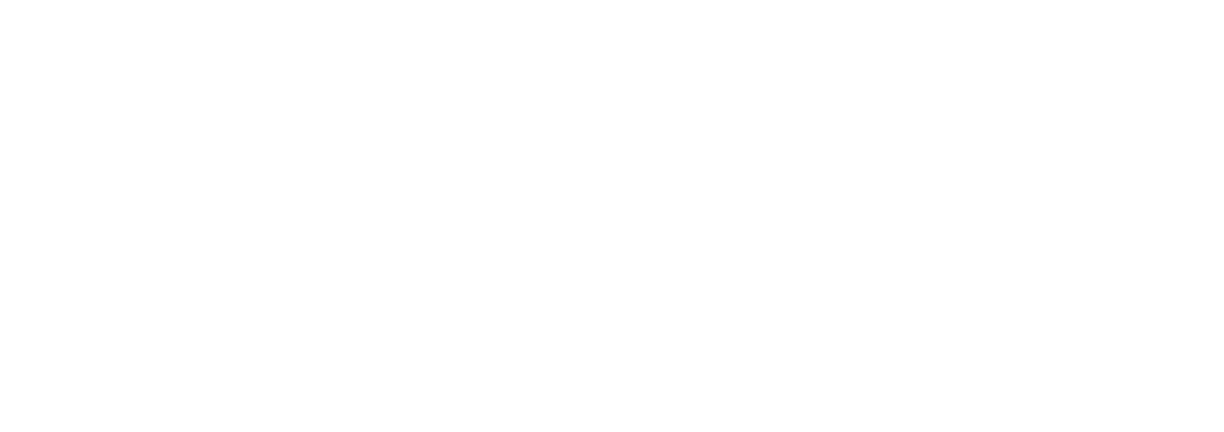