Extruders must operate dependably despite the high temperatures, plastic dust and, in many cases, space constraints that all put demands on electric motors. The question is: How can processors maximize the dependable operation of the electric motors that drive extruders? The question applies to all extruded products, whether pipe, profile and tubing, sheet or film.
Fortunately, electric motors that fill the need are widely available. They include DC motors, NEMA-frame AC motors, and laminate-frame AC motors. American Kuhne, Ashaway, R.I., which manufactures extruders for pipe, profile and tubing as well as sheet and film, supplies extruder motors based on the preferences of its customers, says Kevin Slusarz, VP of process technology. One of the mechanical advantages of laminate-frame AC motors is size, he says. "If you have a very tight arrangement for the extruder, you can take advantage of the smaller motor," he says.
He does not see particular performance advantages for any one motor type, regardless of the type of product being extruded. He says that the company designs a 15 percent safety factor into its extruders for the amount of torque required, regardless of the type of motor used. "As things wear, as the life of the extruder goes on, you will need to turn up the speed of the extruder and take advantage of that safety factor," he says.
Yet, other industry sources interviewed for this article say that laminate-frame AC motors do have particular advantages for extrusion.
Proponents of the laminate-frame AC motor design — which uses sheets of steel that are stacked to create the core of the motor — cite features that they say make it particularly well suited for extrusion applications. The motors can be installed on original equipment and used as retrofits.
Dan Carney, director of sales at T-T Electric USA LLC, a Delafield, Wis., electric motor manufacturer, notes four advantages of laminate-frame AC motors. Especially when compared to NEMA-frame AC motors, he says they offer:
• Low profile, making them a good choice for situations in which space is an issue.
• High power density with the ability to run at a low temperature.
• Low inertia, with the ability to perform at an extended speed-versus-torque range, and high overload capacity at zero speed.
• The versatility to run different resins through the same extruders.
Heat is the enemy of electric motors. Carney notes that it's important that laminate-frame AC motors are spec'd correctly with regard to temperature rise above ambient temperature and insulation class. Of the three temperature-rise classes, which reflect safety margins — H (a rise of 356 degrees Fahrenheit), F (311 degrees Fahrenheit) and B (266 degrees Fahrenheit) — Class B motors are the largest. Of the three major insulation classes — the insulation that a motor requires for a certain temperature rating — motors with Class H insulation can operate at the highest temperatures.
OVERHEATING PREVENTION
Using an undersized motor, which can overheat, can create problems in extrusion applications. Carney says that laminate-frame AC motors have high power density yet will run at cool temperatures if they are sized properly. Most laminate-frame AC motors have Class H insulation, and in many cases it is possible to size them for Class F or Class B temperature rise and still not exceed limited space requirements, he says. He maintains that some OEMs have not sized these motors properly for extruders, which has led to premature motor failure.
"For a time, the practice of sizing a [laminate-]frame motor to Class H temperature rise was applied to extruder applications," he says. "This created too much heat, having a negative impact on the workplace environment and on the motor itself."
He says that running the motor hot stresses motor windings and allows plastic dust to build up inside and outside the motor, creating a thermal blanket that prevents the motor from dissipating heat.
David Dorosa, VP of engineering at Processing Technologies International, LLC (PTi), Aurora, Ill., which supplies sheet extrusion systems, agrees. He explains that laminate-frame AC motors are cooled by a forced-air ventilated system, which blows filtered ambient air through the motor. Very fine plastic dust typical in many plants can be a problem if the motor runs too hot, particularly if it's specified for Class H temperature rise. "If allowed to get hot, those particles, over time, will begin to collect inside the motor, because they get so hot they begin to get soft," he says.
PTi uses both NEMA-frame AC motors and laminate-frame AC motors on its extruders. He says that NEMA-frame AC motors are physically larger, leading to the perception among some customers that they are more rugged. Nonetheless, he says that if properly used, laminate-frame AC motors are well-suited to extrusion environments. They are smaller and more power dense, delivering the same horsepower in a smaller package.
He says the construction of laminate-frame AC motors provides significant flexibility of design, which cannot be achieved with cast-iron-enclosed NEMA-frame AC motors. Among the advantages, laminate-frame AC motors can be designed for better air flow for better cooling, and high power density to get more power out of a smaller package.
For example, laminate-frame AC motors typically are designed as longer motors with smaller diameter rotors to minimize inertia, resulting in better speed control. While he acknowledges that a longer motor, plus a gear reducer at the end of an extruder, require a significant amount of floor space, alternative arrangements with U-shape gear reducers can economize on space.
COOLER RUNNING
Richard Schaefer is general product manager for variable-speed motors for Baldor Electric Co., Fort Smith, Ark., which supplies laminate-frame AC motors under the RPMAC nameplate.
He says typical RPMAC motors for plastic extruders are designed for a B temperature rise, so they run at cooler temperatures. Baldor's extruder-duty motors are designed with B temperature rise and H insulation, "to get the best of both worlds," he says.
Schaefer says laminate-frame AC motors handle constant torque down to zero speed, versus standard NEMA-frame AC motors, which have limited speed range. "These motors can produce full-load torque down to zero speed and up to base speed," he says.
The RPMAC motor provides thermal protection of the windings with closed-loop feedback. On extruder-duty motors, there are two sets of thermostats. One tells if the motor exceeds its B temperature rise, and the other tells if it exceeds the H insulation capacity.
Schaefer also says that laminate-frame AC motors are not tied to NEMA-frame AC motor horsepower and speeds. This is a plus for efficiency, he says. "When you size the motor for the application, you don't have to oversize, and these motors have 200 percent overload torque as standard."
AN OPTION FOR RETROFITS
Scott Barlow, president of Integrated Control Technologies, Coppell, Texas, which retrofits RPMAC motors on extruders, says laminate-frame AC motors work well as replacements in terms of size and performance. He says they were designed as replacements for DC motors; compared to NEMA-frame AC motors, they are easier to match up to the frame for a DC motor in a retrofit. "Many of these motors can be mounted under an extruder barrel, and there is no way you can get a NEMA-frame [AC] motor under there," he says.
Barlow says many customers decide to retrofit to improve efficiency in their plants. Also, they want to replace aging DC motors to reduce downtime. Yet, in the case of retrofits, it's crucial to choose the right motor for the job, he says. "Most of the issues I see are application-oriented, people not really understanding what they are looking at, as opposed to product-oriented," he says. The biggest mistake he sees in retrofits is choosing the motor with the wrong base speed. Base speed is important because it determines torque, the force on the screw.
Barlow says laminate-frame AC motors are designed to work with a variable-speed AC drive. They have a constant blower, so air is continuously blowing across the motor, resulting in cooler operation regardless of the motor's speed. "The laminate-frame motor has 1,000 to one constant torque speed range; it's designed to work down to one-1,000th of its base speed and be cool enough to operate," he says.
In retrofits, a 200-horsepower DC motor and drive can be replaced with a comparable 200- horsepower AC motor equipped with an AC vector drive. The laminate-frame AC motor with a vector drive is able to deliver the required torque at lower speeds, he says. Barlow says that laminate-frame AC motors are 10 to 15 percent more efficient than DC motors. He says efficiency improvements generally result in a payback in two years.
John DeGaspari, senior correspondent
Contact:
American Kuhne 401-326-6200, www.americankuhne.com
Baldor Electric Co., 479-646-4711, www.baldor.com
Integrated Control Technologies, 972-906-7445, www.integratedcontroltech.com
Processing Technologies International LLC, 630-585-5800, www.ptiextruders.com
T-T Electric USA LLC, 262-244-0581, www.ttelectricusa.com
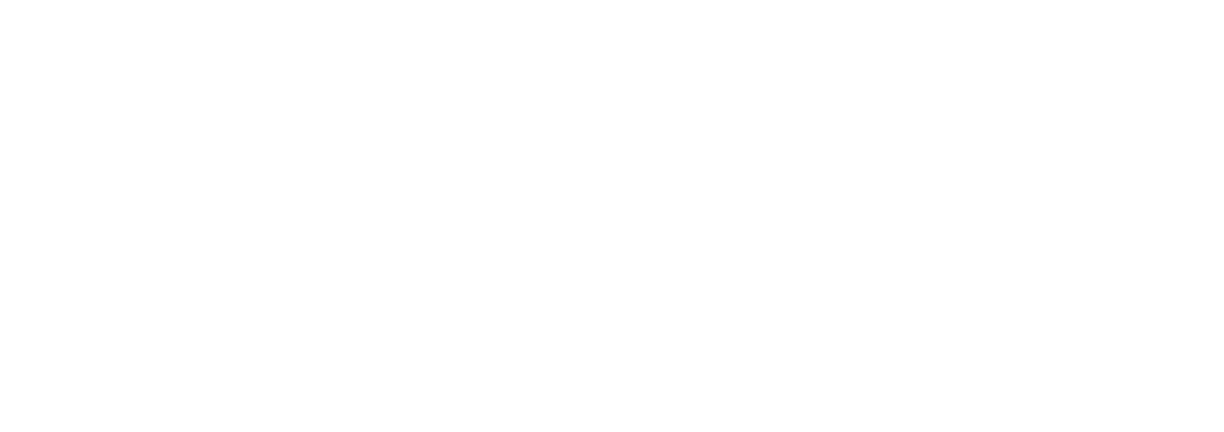