Illig Maschinenbau GmbH & Co. KG, Heilbronn, Germany, demonstrated a digital printing technology using ultraviolet inkjet inks that allows thermoplastic sheet to be printed before thermoforming. The company first showed the technology, which was developed by Fujifilm Corp., Tokyo, for thermoplastics, at Fakuma.
Illig demonstrated the technology on a UA 100g thermoforming machine, which formed a custom-designed shell of a replica sports car. It created the car from a 3mm-thick PET glycol copolyester (PETG) pre-printed sheet, using a maximum forming area of about 38 inches by 26 inches.
Fujifilm developed the inkjet colors specifically for thermoforming decorated thermoplastics. Because the colors harden when exposed to ultraviolet radiation, the printed sheet can be formed right away. According to Fujifilm, the technology allows printing on plastic substrates that can be formed into 3-D shapes. The company says that the process can create branded items in short runs and single-batch orders, and with lower set-up costs than are typical with screen printing.
Illig sales manager Jochen Butz says that Illig and Fujifilm have been collaborating on the technology for about a year. He says previous attempts to thermoform thermoplastics printed with ink have not been successful. The key to the successful application of this technology is the ink, which does not crack or flake off the thermoformed parts. Printing on the plastic sheets is done in a separate stage prior to the thermoforming process, on printing machines supplied by Fujifilm.
The PETG used in the demonstration is clear polyester with good chemical resistance and impact resistance. Illig says the ink has excellent adhesion properties on many plastic surfaces and is suitable for both outdoor and indoor use.
INSIDE THE MACHINE, RAPID MOVEMENTS AND PRECISE CONTROL
Butz says that Illig ran successful trials on its UA-g series machines six months prior to Fakuma. No alterations on the thermoforming machine were necessary, but certain features on the machine, particularly the chain drive that carries the sheet through the thermoformer and centering devices responsible for properly positioning the sheet in the press, help ensure the success of processing the pre-printed sheet, he says.
Single sheets can be fed into the machine and positioned manually, or sheets can be fed and positioned automatically with a loading and discharging device. The UA 100g machine used in the demonstration was equipped with servo drives for all machine movements. Butz explains that the servo drives on the forming tables provide precise movements of the sheet and the tool during the thermoforming process, as well as precise movements of the forming table during the demolding process.
Accurate positioning of the sheet during the thermoforming process is especially important to get the desired results with the decorated thermoformed part, Butz explains. Infrared sensors, together with the servo drives controlling movement of the sheet through the machine, ensure accuracy. Infrared sensors measure temperatures at the machine frame, transport device and material sheet and compare them to the machine settings, which is compensated for by changing the temperature of the heating elements. During the production cycle, a built-in compensation control counteracts the effects of voltage fluctuations or variations in the machine frame temperature.
PRECISE HEATING AND
COOLING OF THE PART
According to Illig, color is an important factor when heating the pre-printed sheet because colors absorb radiation in the wavelength range of visible light. This could be a problem when colors are heated up using halogen heater elements, which operate in the wavelength range of visible light. Sections of the material absorb differently, depending on the colors, which results in imperfections in the forming of the material.
According to Butz, halogen heaters are difficult to adjust to achieve consistent heating overall for the plastic sheet. The UA-g thermoforming machine uses ceramic heater elements as a standard feature, which emit longer wave infrared radiation, resulting in more uniform heating of the colored material, with shorter heating times.
After the parts are formed, central cooling air supply also helps ensure consistent process conditions, according to the company. The central cooling system, which is available as an alternative to cooling fans, draws cooler air from the floor level or the outside, where the air is conveyed to the thermoforming machine to cool the part. Illig offers the piping system as an option, which also includes a filter to remove dust and dirt from the cooling air before it is used on the part. The centralized cooling air supply provides consistent cooling as well as significant reductions in cycle times, says Butz.
The UA-g series is an automatic universal thermoformer suitable for thermoforming from sheet and roll stock. Illig offers a number of other sizes, including the UA 150g, UA 155g, UA 200g, and UA 225g. The UA 250g has a maximum forming area of about 96 inches by 57 inches. The company says the series offers flexibility, precision, reproducibility and long-term stability.
The prices of the UA 10g thermoforming machines range from about $107,900 to $431,600, depending on options, says Butz. The machine demonstrated at Fakuma costs about $399,250, he says. The company has customers in Europe that are using the printing technology.
John DeGaspari, senior correspondent
Contact:
Fujifilm USA, 914-789-8100, www.fujifilmusa.com
Illig LP, 484-639-7124, www.illig.de/en/illigmaschinenbau
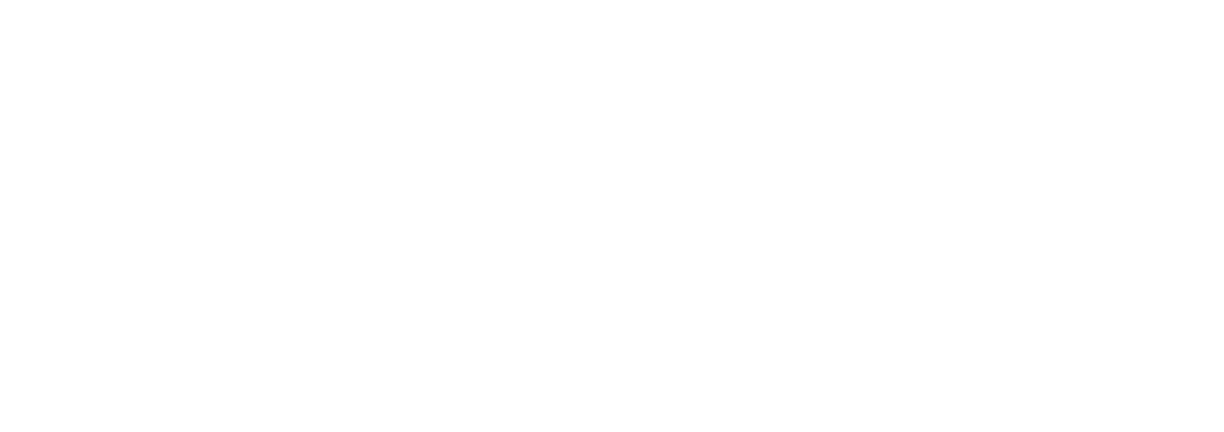