At a ceremony, HRSflow literally rolled out the red carpet for what company officials are calling the most modern facility in North America for the production of hot-runner systems. They celebrated the opening of the new Byron Center, Mich., facility on Sept. 23.
Measuring roughly 40,000 square feet, the new plant is a duplicate of production facilities in Italy and Shanghai. To ensure quality, officials say the plants' technology, equipment, methods and design are identical. HRSflow is owned by INglass Group SpA, San Polo di Piave, Italy.
"Much of what you see is automated robotics to further improve process and efficiency," says Maurizio Bazzo, president and CEO of INglass-HRSflow. "Our metals of construction are unique. All manufacturing sites are identical, identical in quality and performance."
The Michigan site was selected based on the company's long-term strategy. Because of the proven infrastructure that is in place at the other locations, it took just 10 months to get the new site operational. While it was important to have three locations to serve the needs of the local markets, Bazzo says that the company has the flexibility to accommodate backlog at any of its plants, should a capacity issue arise. HRSflow has sales and service operations in Windsor, Ontario, and Greenville, S.C.
The new site in Michigan represents an amalgam of sophisticated software use and technology. The warehouse is automated with a Modula lift system. Enterprise resource planning software from Infor LN exchanges information with the production division throughout the factory based on the picking list. The assembly lines are fed based on the needs of that list. State-of-the-art machinery includes a Palletech machine, which is for manifold construction and allows many unique designs to be machined at once. It is capable of expansion and robust enough to handle more needs as they arise. Its multitasking capabilities are hailed as being appropriate for any manufacturing or volume requirement. In this way, users can make the most of labor where one employee can operate multiple machines. The building also has three CNC machines that can run for two days unattended.
"The pieces coming from here have to be perfect. We invest a lot in machine quality," says operations manager Umberto Santin. The goal is to produce quality components and reduce or eliminate human error.
In a fully automated cell, a Comau six-axis robot works in conjunction with an LNS Quick Load Servo S3 T-L bar feeding system and a DMG Mori CNC milling machine to produce components. Officials have set out to further automate the process not only because it removes human error but also because it removes bottlenecks that can occur when making a product that is an assembly of components. This concept reduces overall manufacturing cost, while improving quality.
The Flexflow valve gate hot-runner system is HRSflow's latest product. It is a servo-driven valve gate that is designed to independently control each pin by precisely adjusting position, acceleration and velocity of the stroke. This product made its North America debut at NPE. Standard valve gate technology on the market controls pin movement in only a fully open/closed condition or, in some cases, two positions, officials say.
The Flexflow uses the servo-motor operation directly transferred to the valve pin stroke. A specially designed control system operates the valve gate pin, which can be programmed in eight distinct positions with varying velocity and pressure in both the opening and closing phase of operation. This provides optimal flow control from each valve gate nozzle into the molded part. By precisely varying the effective orifice size, flow is controlled at a consistent volume. The position accuracy provided by the servo-motor delivers an accurate and repeatable result not available before the development of this technology. The precise control of pressure and flow rate during cavity filling ensures inner tool pressure builds evenly and without the sudden pressure drops that occur in conventional systems. Pressure transducers can also be incorporated to monitor the packing phase and this ensures repeatability in the process.
A standard valve gate does not have uniform pressure, says Flexflow product manager Moreno Carvani, during the demonstration of the production cell. Flexflow, though, provides automatic control and uniform pressure distribution.
The demonstration cell at the ceremony incorporated Flexflow on a 990-ton Engel press that was molding a rear spoiler from thermoplastic olefin in a 55-second cycle. If the part was molded in a standard style without Flexflow technology, it would experience a mold deflection of 0.1mm. With the technology, the mold deflection is reduced by 50 percent.
The company has more than 100 installations of Flexflow, many of those in Europe, says John Blundy, president of HRSFlow North America. The technology is designed for medium to large multigated injection molded parts that typically are found in the automotive industry. Product examples include spoilers, door panels, grilles and pillars. The main advantages are improved surface finish of Class A molded parts; improved part performance; part weight reduction; reduced mold deflection resulting in less clamp force; and accurate and reproducible family mold applications. Clamping force reduction is about 20 percent.
Angie DeRosa, managing editor
Contact:
HRSflow North America, 616-228-6894, www.hrsflow.com
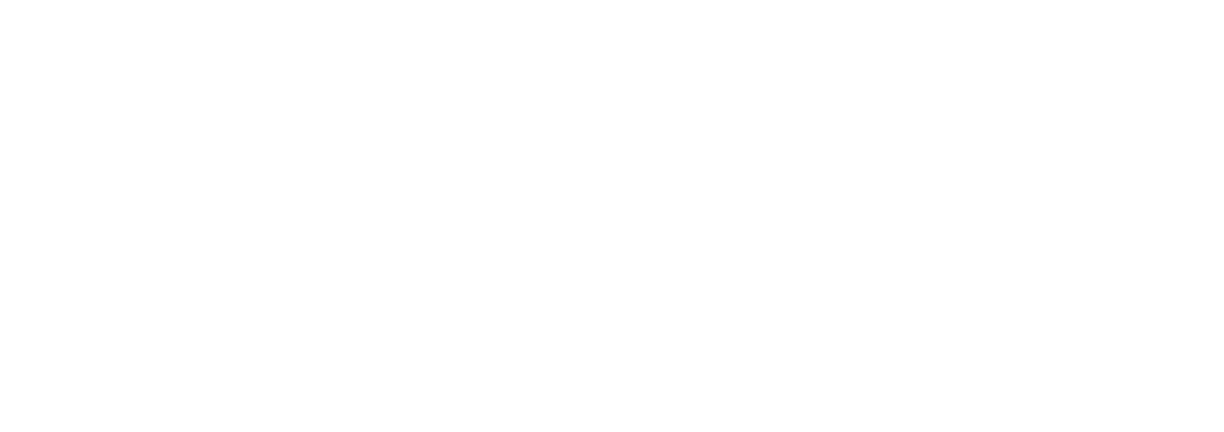