Rapid Delivery is a key for success for M.R. Mold & Engineering Corp., Brea, Calif., which makes molds for liquid silicone rubber production. With that goal in mind, the company is continuing to expand its use of technology.
M.R. Mold has built thousands of intricate, complex tools for the medical market and other industries with applications requiring liquid silicone rubber molding, says Rick Finnie, president and owner. Intensifying demand for increasingly complex part designs has prompted the 30-year-old tool designer to invest in its first five-axis CNC machining center.
M.R. Mold currently operates 11 three-axis CNC machines at its mold-making plant, but expects the new five-axis unit to greatly enhance its capabilities. "The type of complex 3-D part geometries that is common in the industry gives a five-axis machining center a distinct advantage over a three-axis CNC. Better surface finish, shorter cutter tools and faster cutting speeds are all benefits of five-axis machining. We can build a tool with complex geometries easier and more quickly with the new unit," says Finnie.
M.R. Mold invested $700,000 in the purchase of a Yasda YBM Vi40 precision machining center, manufactured by Yasda Precision Tools KK, Satosho-cho, Japan (represented in the U.S., by Yasda Precision America Corp., Elk Grove Village, Ill.). The vertical jig borer features three-axis of movement on a rigid platform. Two additional axes of travel are initiated through a table rotation. The unit, designed for high-accuracy milling of very hard and high-grade molds, can reduce the number of process steps for mold building compared to competing tool-making equipment.
ELIMINATE EDM
The Yasda Vi40 five-axis unit will better handle much of the intricate tooling work done on M.R. Mold's high-speed mill. Finnie cited a tooling project for a medical OEM that required three electrodes to burn a single, complex geometry. "Using the Yasda five-axis CNC eliminates the programming, cutting and burning of those electrodes and the hours required on the electrical discharge machine (EDM) and creates the geometry in one step. Our goal is to eliminate EDM operation from our mold builds, which will provide our customers with quicker lead times," says Finnie.
M.R. Mold expects use of the Yasda CNC will trim delivery lead times by 20 percent by eliminating the EDM process and its associated programming, electrode cutting and burning from the production of intricate tool geometries. The higher cutting speeds and shorter tool length requirements of the five-axis also yield cost savings.
M.R. Mold says at least 70 percent of the molds it builds feature complex geometry. Those tools will see some bench time on the Yasda and benefit in some way from its easier setup and higher performance capabilities. Molds for medical parts with complex features such as CPAP masks, nasal prongs, baby bottle nipples and micro-medical parts will be built on the Yasda unit, says Finnie. Parts with a simpler geometry will be made on its three-axis machine centers. The company's equipment includes two lathes, two EDMs, a Micron for electrodes, a wire EDM and three OKK-type CNC units.
To date, M.R. Mold has cut one cavity using what it calls 3+2 axis machining. Cutting steel using the full five-axis capability will come with additional training for its programmers and operators. M.R. Mold says one of its lead mold makers will become the dedicated operator of the unit.
M.R. Mold purchased hyperMill CAM software from Open Mind Technologies AG, Wessling, Germany, for use with the five-axis unit. It uses Mastercam software from CNC Software Inc., Tolland, Conn., for its three-axis machine centers.
M.R. Mold also operates a 4,000-square-foot technical center within its 15,000-square-foot mold-making plant, featuring six injection presses (including models from Arburg, Boy Machines, Engel and Negri Bossi), a compression molding machine, LSR pumping equipment from Fluid Automation and 2KM North America and a curing oven. The mold maker also has several in-house developments for use with mold testing and trials, including single- drop cold-runner systems, a custom single-axis hydraulic robot for parts removal, robot EOAT and a pneumatic stuffer for gum stock silicone.
Mikell Knights, senior correspondent
Contact:
M.R. Mold & Enigeering Corp., 714-996-5511, www.mrmold.com
Yasda Precision America Corp, 847-439-0201, www.yasda.com
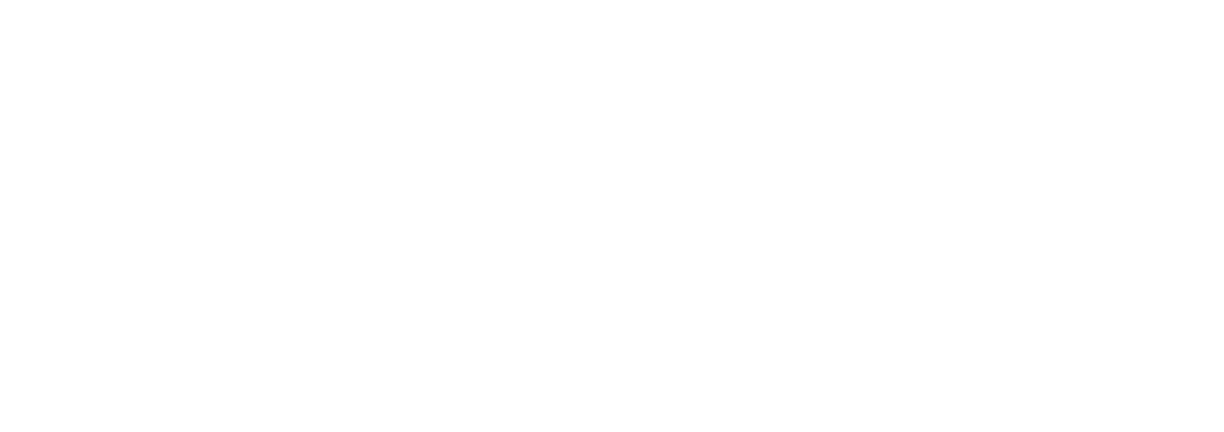