Several suppliers are promoting new processes for gas-assisted molding with carbon dioxide (CO2), as well as updates and advancements in equipment and technology for nitrogen-based gas-assisted injection molding. The technology involves hollowing the core of a molded part with thick sections using gas to reduce molding cycle time and save material.
Developments in the market include technologies that allow for spot cooling or better control over how the gas is introduced or tracked during operations. Plantwide and at-the-press systems have also been updated.
These innovations come despite the economic downturn that started about eight years ago, when the bubble burst for several well-known suppliers of gas-assisted injection molding technologies. Major suppliers, including Gain Technologies, Alliance Gas Systems, Epcon and Cinpres, have exited the market or no longer exist. However, other suppliers are filling the void.
SUPERCRITICAL CO2 DEBUTS
Linde AG, Munich, a leading international supplier of compressed and liquefied gases, is promoting the use of CO2 as a higher performance alternative to nitrogen in gas-assisted injection molding applications with the introduction of two new processes.
The Gases division of Linde (represented in the U.S. by Linde Group LLC, Murray Hill, N.J.) has entered the plastics industry with what it calls an enhanced Gas-Assist Injection Molding (eGAIM) process. The process uses CO2 in its gas, liquid and supercritical fluid phases to deliver cooling to the interior of a part while creating a smooth, hollow interior channel, according to Edward Smith, applications specialist for industrial applications. CO2 eGAIM was developed by Linde a year and a half ago; however, NPE marked the debut of the equipment for the process, says Smith.
"With the proper pressure boosting and cycle optimization, cooling cycles can often be reduced by more than 50 percent compared to nitrogen gas-assisted operations. Overall cycle times can be reduced 20 to 50 percent with CO2 compared to nitrogen," according to a white paper published by Linde. Use of CO2 can reduce cycle times of PP molded parts by 10-15 percent and PC part cycle times as much as 40 percent, says Smith.
Carbon dioxide is gaseous at ambient temperature and atmospheric pressure. When CO2 is compressed to more than 1,070 pounds per square inch (72.8 bar) and heated above 87.8 Fahrenheit (which occurs when the liquid CO2 encounters the molten polymer in the mold), it reaches a supercritical state where the material exhibits the heat capacity and non-compressible properties of a liquid.
CO2 in its supercritical state is denser than nitrogen at the same pressure yet has a much higher heat capacity, enabling the CO2 to effectively cool the interior surface of the part as the pressurized liquefied gas creates a hollow channel, according to the report.
The supercritical CO2 fluid removes latent heat captured from the interior of the part as it hollows out the molten material. The phase change to a gas takes place during venting, says Smith, where the pressurized liquid evaporates when the pressure is released. There is no need to dry the inside of a part or handle the material in liquid form. "Unlike water-assisted injection molding, there is no concern regarding corrosion of machine parts, damage to electrical controls or the development of microbiological growth on the interior of the part due to moisture," says Smith.
CO2 eGAIM can be used for any part made using nitrogen gas-assisted molding, but Linde's focus for the process is on large parts with thick sections or parts where cooling time is a major percentage of the overall cycle. Hollowing large parts, such as pipe for automotive cooling fluid and handles for white goods or furniture, is an initial application.
For small molding applications, liquefied CO2 is supplied by Linde in steel cylinders or tanks at a pressure ranging from 800 to 900 psi. Siphons draw the CO2 from the tank, feeding Linde's specially developed control unit that increases the pressure, then manages the delivery of the pressurized liquid into the mold.
For plantwide delivery of CO2, Linde supplies the liquid under lower pressure (290 psi) and at a temperature of 0 Fahrenheit in tanker trucks to a storage tank. The storage tank feeds Linde's new Presus C compressor station, which boosts the pressure to 5,000 psi (300 bar) using a proprietary liquid pump. The liquid CO2 is piped through the plant and sent to one or more CO2 pressure control units, each of which supplies an injection press.
Linde's control unit is designed to process CO2 or nitrogen, and users can make the switch from the control panel. Different sealing materials are used in the equipment depending on the gas used. At NPE, CO2 eGAIM was used at injection molding machine maker Sumitomo's booth to produce a long handle from PC.
Linde, together with ISK GmbH, Ainring, Germany, also developed a spot cooling technique using specialized equipment and CO2 for localized cooling of hot spots in molded parts. The spot cooling technique supplements mold cooling by bringing cooling to hard-to-reach areas, such as long, thin cores, fillets, slides and ejectors. In these areas, space limitations can prohibit the creation of a mold cooling channel or result in a thin mold cooling channel becoming clogged by deposits or becoming the cause of pressure losses. In either case, hot spots can form on the mold, which can extend cooling and overall cycle times.
Linde's spot mold cooling technology can reduce cycle times up to 50 percent, says Smith. The system uses special solenoid valves designed for liquid CO2 that deliver the material to specially designed stainless steel capillary tubes inserted into small chambers in the mold. The chambers in the mold may be drilled or eroded into the mold itself, or formed by a hollow-core pin design. "We've gotten spot cooling into a medical mold with a space of 0.083 inch," says Smith.
With spot cooling, liquid CO2 is fed under 850 psi through the capillary tubes to the points where cooling is required. An expansion chamber at the end of the capillary tube encourages a phase change that creates a CO2 snow and gas mixture with a temperature of minus 109 Fahrenheit. The CO2 pulls heat from the mold and escapes from the expansion room as a gas through an annular gap between the hole and capillary tube.
Existing molds can be retrofitted with the spot cooling temperature control system. The unit is equipped with a programmable logic controller (PLC) and operates off of a signal from the PLC of the injection press. Linde engineers assist with system design, setup and operation.
ALL-IN-ONE GAS-ASSISTED UNIT
Bauer Compressors Inc., Norfolk, Va., said NPE marked the commercial availability of N2IT, the company's new integrated nitrogen generator, booster, storage and process-control unit. The all-in-one unit was introduced at the last K Show in Germany, but the first working unit available for sale was introduced at NPE, says Rick Goralski, business unit manager for plastics systems within the Bauer Plastics Technology Group.
The unit requires compressed air and electrical inputs to generate its own supply of nitrogen. It is offered with a nitrogen generation rate of 4 standard cubic feet per minute (SCFM) and 98 percent purity nitrogen, while a 2 SCFM model generates nitrogen with 99.5 percent purity. Oxygen in the nitrogen can cause problems for the part and the tooling, so high-purity nitrogen works best for gas-assisted molding, says Goralski. "It can generate enough nitrogen for virtually every current gas-assisted application," he says.
Features include a 7-inch Siemens touch-screen display and a UL-certified control panel with a PLC controller for operation, maintenance and troubleshooting tasks. Multiple pressure sensors are part of the turnkey system, including supply pressure, compressor inlet pressure and process pressure. Bauer sourced components from other gas devices designed by its parent company, the Bauer Kompressoren Group, Munich, for this configuration. The portable unit rides on casters.
In addition to a nitrogen-purity monitoring feature, the system features Bauer's True Track Ramping process, which lets the molder more smoothly adjust the pressure profile for the gas- assisted operation. True Track Ramping doesn't allow the nitrogen delivery system to deliver gas pressure in a shortest time-maximum pressure scenario, which can cause fingering. A dome regulator and the controller ramp up the pressure from 0 to 1,500 psi over time, as a value of psi per second, says Goralski. Users can create a pressure ramp profile that the system can track, and is repeatable. The feature allows the molder to process out some of the defects inherent to putting a maximum blast of gas in a part, says Goralski. The slightly slower ramp up allows the walls of the part to set up a little bit longer, which can enhance final part quality.
A popular application for gas-assisted molding is a kayak paddle, which features a thin blade and thick center core. If a quick burst of gas is applied, gas would bleed into the thin-walled areas. With True Track Ramping, the gas pressure is increased incrementally (with user-selected starting and ending pressures). True Track Ramping has been an unnamed feature available with all of Bauer's gas-assisted systems, says Goralski. It was given a formal name across its product line with the introduction of the N2IT unit.
Bauer also announced at NPE that it is bringing two other gas-assisted technologies here that it previously sold only in Europe. FCC 5 is a high-pressure controller for gas-assisted injection molding with a plethora of control features. They include a PLC for closed-loop operation, a 10.4-inch touch-screen interface and graphic screens for set point and current value display. The unit features an automatic cleaning cycle, in which a burst of nitrogen can be set to occur between molding cycles while the mold is open. The system allows for pressure ramping to be set up based on time. The system is designed to handle one to four valves for gas assist, supplying 5 to 400 bar pressure to the nitrogen. Process data can be stored on a compact flash or USB or through an Ethernet connection.
Bauer also introduced its Volume Control (VC) device designed to measure and track nitrogen consumption from shot to shot for each molding cycle that uses a gas-assisted approach. The VC works as a quality-control tool, measuring the volume of gas used in each shot. Processors can review a log of nitrogen consumption to determine process stability or discover problems, says Goralski.
Knowing the actual volume of nitrogen consumed can be useful for detecting a leak. Monitoring nitrogen use can prevent gas nozzle blockage, and can help molders avoid molding defective parts, says Goralski.
The VC is stationed between the high pressure conveyor and the system controller. The unit is offered as a stand-alone or add-on version, and offers the ability to measure up to 350 bar. "The unit only measures gas volume, and is capable of putting the machine in alarm if the volume changes," says Goralski.
VETERAN SUPPLIER ADDS CAPABILITIES
NitroJection Corp., Chesterland, Ohio, offers parts for every brand of nitrogen gas-assisted system, including its own. It also repairs, services and rebuilds all brands of equipment for nitrogen gas-assisted molding, including systems from companies that no longer exist, like Gain Technologies, Alliance Gas Systems and Epcon, says President Steve Johnson.
"NitroJection has the second-largest patent portfolio relating to gas-assist injection molding in the United States, and it was the first company to commercialize a gas-assist and processing system in North America," says Johnson, noting that it is the largest reseller of used equipment in the U.S. The company, formed more than 25 years ago, buys, sells and exchanges equipment, and manufactures its own line of gas-assisted molding equipment.
NitroJection introduced two nitrogen gas- assisted models about two years ago. The Nitro- Jection Satellite Unit (NSU) is specifically designed for molders with an existing source of high-pressure nitrogen. The NSU is designed without an internal pressure intensifier and attaches to a plantwide nitrogen gas supply line. NSU requires the plant line to deliver nitrogen at high pressure (6,000 psi).
NSU is designed to serve one or two molds on one or two presses. It is offered with one, two or four valves to allow gas injection through a machine nozzle, or independently into a multi-cavity mold using an in-mold gas pin from the company, says Johnson. Features include fast-acting Tescom-brand electronic regulators that control gas injection pressures, as well as an industrial PLC and 8-inch color touch screen. Additional features include a programmable, selectable alert function that lets the operator know if the incoming gas pressure drops below a user-selected pressure. Other features include an auto purge cycle as well as remote output and independent start signals that allow for gas injection to multiple presses, says Johnson.
NitroJection also offers its Nitro Booster System (NBS) 1000 series gas intensifier system, which is a compact portable source for high-pressure nitrogen generation. The air-driven NBS-1000 is supplied as a fully assembled turnkey system that receives regulated nitrogen (250 psi) from gas cylinders or other sources and intensifies the pressure up to 6,000 psi. The final output pressure is controlled by an adjustable mechanical pressure switch. The system, ideal for the pressurization of any inert gas, features a pneumatically driven gas booster that requires either shop air at 100 psi or nitrogen up to 2,500 psi.
NBS-1000 has air- and nitrogen-isolation valves, a system vent valve and a control panel that displays the inlet pressure, outlet pressure and drive air gauges. "NBS-1000 uses the same pump system as is used in our NitroJection Processing Unit. It is just pulled out and framed up as a separate unit," says Johnson. NBS-1000 is basically a pumping system designed to supply nitrogen to one or two injection units when the plantwide nitrogen supply line is down for maintenance.
The NitroJection Processing Unit (NPU) is a portable, stand-alone gas-assist controller that intensifies and injects nitrogen into the mold through patented nozzles or in-mold pins from NitroJection. Features of the system, which has been out for many years and targets molders starting out with gas-assisted molding, include a new auto-purge feature and 8-inch color touch screen. The system will intensify gas pressure up to 10,000 psi, and allows for seven stages of digitally controlled nitrogen injection pressures.
NitroJection is looking to broaden the application of gas-assist in the injection molding process with the future introduction of a system that delivers gas into the barrel of the press for material foaming prior to injection. This approach has been done with structural foam applications for a long time, says Johnson. Unlike the MuCell process from Trexel Inc., Wilmington, Mass., this approach will be designed to operate with a conventional screw and barrel.
The new unit's advantage over foam molding with a chemical blowing agent is that the system in development allows the user to control the amount of nitrogen dispensed into the injection unit and scale the amount of foaming and the cell size of the foamed structure. Several trials are underway with the new unit, which will target parts with a non-Class A structural foam-type surface.
NitroJection also developed a line of spring-loaded pins for gas-assisted molding in which a pin in a sleeve opens under the pressure of gas during gas injection, which increases gas flow. The pin is closed under zero pressure by the spring and is designed to eliminate plugging. An auto-purge feature is also included on the controls to reduce the time required to clean the pin, says Johnson.
NEW CONTROLLER UNVEILED
Maximator GmbH, Nordhausen, Germany (represented in the U.S. by Maximator-AIM Inc., Whitmore Lake, Mich.), a supplier of high-pressure and testing equipment, hydraulics and pneumatics, launched its new RM350 series of CO2 and nitrogen gas-assisted controllers in March.
The basic unit comes with two or four electromagnetic, direct-acting, high-pressure gas-control valves that handle gas supply up to 5,000 psi. Two interfaces allow the unit to work with one or two injection units at the same time. The system comes with an optional air-driven booster that allows for use of nitrogen from standard gas bottles without the need of a regulator. Hydraulic core packs can be added to operate overspill pins or valve gates. Units that operate without a gas booster are now available with a high-pressure receiver to intensify the gas pressure. Users can add a new larger cabinet or a two- or four-valve internal hydraulic power pack with a 6.5-gallon tank as part of the company's MAX option. High-speed closed-loop control can be programmed on a 10-inch widescreen LED touch panel.
Mikell Knights, senior correspondent
Contact:
Bauer Plastics Technology Group, 586-247-1900, www.bauerptg.com
Linde LLC, 800-755-9277, www.lindeplastics.com
Maximator-AIM Inc., 734-449-8301, www.maximator-aim.com
NitroJection Corp., 440-729-2711, www.nitrojection.com
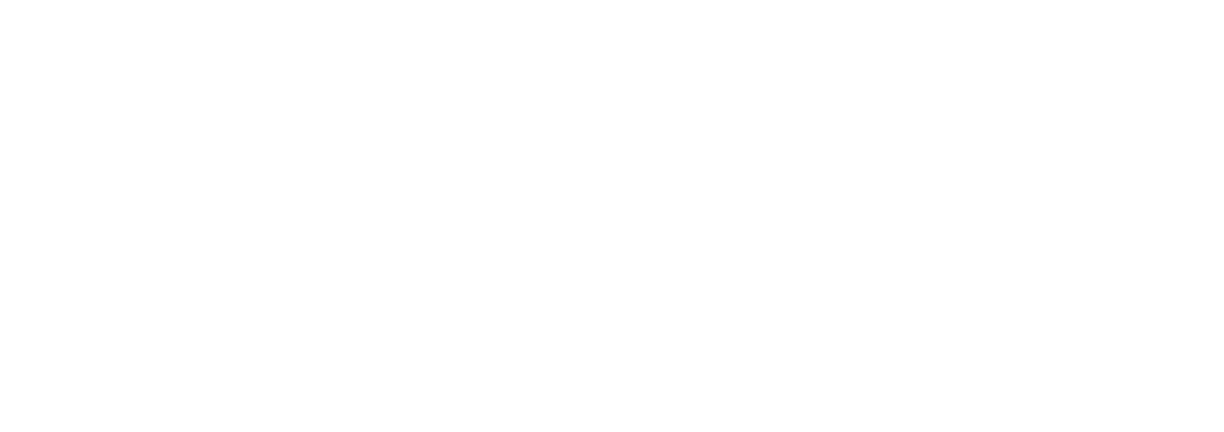