It was big at NPE and the Asian market saw the same emphasis during Chinaplas, held May 20-23 in Guangzhou, where industrial automation is a high priority. Why wouldn't it be? In the ultra-competitive world of plastics manufacturing, processors are getting their game on in terms of automating for increased efficiencies and less waste. This is all happening amid increasing energy costs everywhere and growing concerns about water conservation. Those realities know no continent.
For China, however, there is a simultaneous push from the central and provincial governments. Jack Tsai, marketing and service manager, automation business development, for Shini Plastics Technologies Inc., Dongguan City, China, says the Chinese government noticed the trend and realized the importance of automation in maintaining the country's manufacturing competitiveness.
"Beginning in 2014, China has set its major development policy to promote industrial automation and launched various subsidy schemes throughout its central and local governments," he says. "Foreseeably, in the process for China to move from Industry 3.0 to 4.0, using machines to replace labor is a no-return road and surely the automation business in China will continue to expand in accelerated speed in years to come. Especially when compared with 70 to 80 percent industrial robot utilization in developed countries, China is only at a relative low of 40 percent."
Another development at Chinaplas portends more efficiency. The China Plastics Processing Industry Association (CPPIA) announced its adoption of Operation Clean Sweep (OCS). The signing ceremony happened during Chinaplas. OCS is an initiative under the Society of the Plastics Industry to contain, reclaim and/or properly dispose of resin pellets. SPI and the plastics division of the American Chemistry Council have been working together on a revitalized program. Recommendations for worksite setup include using bulk-handling equipment that is designed to minimize pellet leakage; installing central vacuum systems where practical; and conducting routine inspections and maintenance of equipment used to capture and contain pellets.
Throughout Chinaplas, automation came in many forms, not just robotics, and that is an important distinction. Industrial automation means integrating all parts of the plastics manufacturing process and tying it together through the Internet of Things (IoT).
THE ROLE OF ROBOTICS
As the aforementioned macro trends make their impact, the Chinese government is simultaneously pushing forward with robotics research, according to the International Federation of Robotics. The country has the world's largest market in the sale of industrial robots but also has a low robotics density, as Shini's Tsai indicated. Here are the figures: China has only 30 industrial robots per 10,000 employees in manufacturing industries overall. Germany's robotics density is 10 times larger and in Japan, it's 11 times larger. For North America, robotics density is five times higher than in China. Automation in China is in its nascent phase.
Worldwide, growth and innovation among robot manufacturers have been peppering the manufacturing landscape. Global robotics manufacturer ABB Inc., Auburn Hills, Mich., displayed its IRB 460 high-speed robotic palletizer, which is specially designed for high throughput requirements for end-of-line and bag palletizing applications. The robot has a FlexGripper Clamp for handling heavy or open-top cases of products. This robot is equipped with the Robot Studio Palletizing PowerPac software for ease of setup and programming.
If you want a more telling example of ABB's commitment to the next generation of robotics, though, you should meet YuMi. ABB acknowledges that few production arenas are changing as quickly as small parts assembly, and the electronics industry is a prime example. YuMi is a dual-arm robot that essentially has humanized characteristics to work alongside people, specifically in the electronics industry.
Here is the reality that manufacturers are facing: Certain end markets, such as electronics, are seeing demand for products skyrocket past the supply of skilled labor, according to ABB.
Robotics demand is such that ABB now will manufacture robots in the U.S. The production will begin immediately at an existing plant in Auburn Hills. There, ABB is producing mechanical units and robot controllers. Robot controllers, including standard IRC5C controllers, IRC5C compact controllers and drive modules, will be built at the site from scratch. This is ABB's third robotics facility worldwide. Its other plants are in Shanghai and Västerås, Sweden.
Spokesman Alex Miller told PMM that the U.S. is ABB's largest market with $7.5 billion in sales. ABB has invested more than $10 billion in research and development in the U.S., capital expenditure and acquisitions since 2010. Continued investment in North America is a significant part of the company's strategy.
Wittmann Battenfeld GmbH, Vienna, recently announced plans to build more robots at its factories in the U.S., Vienna and Mosonmagyaróvár, Hungary.
Wittmann Battenfeld robots were playing basketball during Chinaplas, which drew a lot of attention. The company launched its new W8 pro robots recently. During NPE, its W8437X45 pro robot was on display in a molding cell. The new servo modules for the W8 pro series have an extremely ergonomic and space-saving design, according to the company. They can be ideally positioned within striking distance of the main servo drives. The company also has enhanced the W8 series with new servo-driven rotating additional axes.
Tieren Robot Automation Co. Ltd., Xiangyang, China, showcased its five-axis AC servo-driven robot. The robot used an opening control system developed by Tieren. Its breakthrough function is its centralized control to monitor and manage the production data of plastics during injection molding.
DESIGNING CONTROL
Keba AG, Linz, Austria, presented new and improved products for its KePlast control platform for injection molding machines. This line now features platen parallelism and clamping force control for two-platen presses. The company says the control system achieves gentle machine movements that guarantee lower maintenance requirements and shortened cycle times. A processor can get a machine started more quickly because of automatic calibration and simple, exact positioning through optimized servo valve control.
Keba's latest product is the KePlast i8000, which offers the latest multi-touch technology. It is a Linux-based package that has an open control platform and adaptability for the machine's needs. This control platform can be used on hydraulics, hybrids and all-electric multi-component machines as well as high-tonnage models.
KeMotion is the company's robot control platform. It is an open and individually adaptable system optimized for automatic parts-removal processes on injection molding machines. The benefits include rapid startup and programming due to a multitude of predefined parts-removal programs.
Keba works with many machinery suppliers, including Borch Machinery Co. Ltd., the injection molding machinery maker that is based in Guangzhou but that has an aggressive plan for growth in the North American market. Stateside, Borch does business as Borche North America with operations based in Ontario, Calif.
Barney Wang, Keba's marketing specialist in Shanghai, says that customers are demanding scalability, process monitoring for injection molding and remote support.
Angie DeRosa, managing editor
Contact:
ABB Inc., 800-435-7365, www.abb.com
Keba Corp. US (for Keba AG), 219-246-2195, www.keba.com
Shini Plastics Technologies Inc., 770-831-5959, www.shini.com
Tieren Robot Automation Co. Ltd., 86-710-2769830, www.trarobotic.com
Wittmann Battenfeld Inc., 860-496-9603, www.wittmann-group.com
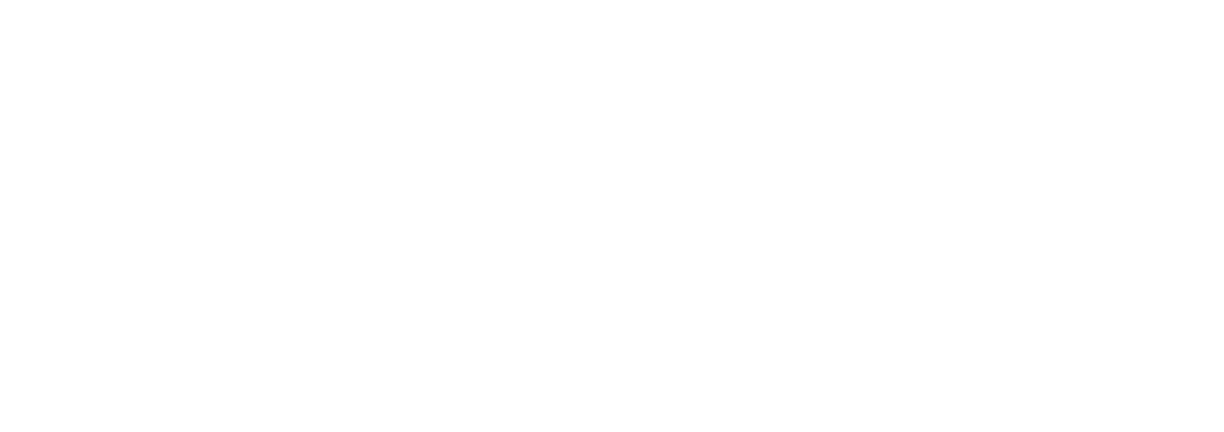