Entek raises utilization rate with new extruder for color compounding
Most extruders used for color compounding sit idle 60 percent of the time, so the key to building a better extruder is simple: design a machine that runs 60 percent of the time.
Entek Extruders, Lebanon, Ore., discovered the low utilization rate when it surveyed customers. The survey was the beginning of a 2½-year project that culminated in January with the unveiling of a new, 43mm, co-rotating, twin-screw extruder trademarked QC3-43MM.
"Our goal with the QC3 is to raise the utilization rate," said Kirk Hanawalt, president of Entek's extruder division, when the new machine was shown at Entek headquarters in Lebanon. "We have done it. This is a beautiful machine!"
QC3 stands for quick change, quick clean and quality control.
Entek's engineering and production staff exuded excitement when they unveiled the QC3, which is the company's first new extruder since 2006. One QC3 extruder has been built and will be shown at NPE, then returned to the showroom in Lebanon. Two more already have been sold and will be delivered this summer.
Hanawalt says the market for small extruders has changed. "The industry now is characterized by shorter runs. Users don't want to keep inventory so they need flexibility," he says. "We found that 10-15 screw-set changes in a day is not unusual."
Entek started research for the QC3 in 2012 with a survey of 10 customers. The dialogue continued with some of those customers until the design became reality.
Officials found the low machine utilization rate was largely due to lengthy screw-set and color change-over procedures and maintenance times.
"If a company makes 15 batch changes in 24 hours, it takes a lot of change-over time," says Hanawalt. "We are the first one in the industry to market an opportunity to significantly reduce that time."
The 5-minute screw-set changeover by one operator can significantly increase machine utilization. Customers told Entek it took an estimated 15-25 minutes with two operators to perform the same procedure. The faster time is accomplished by quick-opening access panels, required tools stored at the point of use and an all-new self-alignment feature that guides the screws into couplings. Another new key design allows screws to be installed in only the correct way.
"Some users were settling for less than optimal screw designs because of the work it took to change the screw design," says Craig Benjamin, a design engineer at Entek. "Our new design makes it faster to change the screw and makes it mistake-proof."
Another significant improvement in extruder utilization rate comes from a new strand die that Entek designed. The strand die comes with two die plates. The unique design allows one die plate to be taken off for cleaning and replaced with the second die plate, which returns the machine to service in a matter of minutes.
With a traditional strand die, the entire unit must be removed, which includes disconnecting or removing connections for resin, pressure transducers, heaters, sensors, probes and such. Next it goes into an oven to remove resin, then is replaced so the machine can be put back into service.
"With this new design, all those things stay on the machine," said Melissa Jensen-Morgan, an Entek design engineer. "One person can take off just the die plate that has to be cleaned and immediately install the clean one. This also eliminates potential for contamination."
Jensen-Morgan said the new design helps "mistake-proof the die" by simplifying the changeover procedure.
The strand die is sold separately and the price has not yet been set, although one Entek official said that the intention is to price it at a very value-driven number.
Maintenance and cleaning time on the stainless steel and powder-coated extruder has been reduced by designing the frame to deflect dust. Quick-opening panels provide easier access inside.
John Effmann, director of sales and marketing for Entek Extruders, said the QC3 will cost only slightly more than the 40mm unit it replaces. "We want to offer more for about the same money," he says. "We started with a clean sheet of paper and looked at everything. We used lean manufacturing principles throughout the process to reduce costs."
Nearly all the extruder's components are manufactured at Entek's Lebanon plant.
The 200 horsepower motor (at 1,200 rpm) provides 33 percent higher output shaft torque than the extruder it replaces. The gearbox has been redesigned and includes a simpler lubrication system. The screw OD/ID ratio has been increased for better throughput of difficult materials.
The cooling system uses water-to-air heat exchangers and is integrated into the extruder as opposed to hanging on the outside.
Effmann said the 43mm bore diameter was selected because "our research has shown that this size is the most common for general material compounding applications."
New design and features on the QC3-43MM will now be phased into Entek's other extruders, which range in size from 27mm to 133mm. While still important, the quick-changeover features of the new QC3-43mm extruder become less critical on the larger machines since those are generally used for longer production runs.
For more information:
Entek Extruders, 541-259-1068, www.entek.com
Ron Shinn | Editor
Editor Ron Shinn is a co-founder of Plastics Machinery & Manufacturing and has been covering the plastics industry for more than 35 years. He leads the editorial team, directs coverage and sets the editorial calendar. He also writes features, including the Talking Points column and On the Factory Floor, and covers recycling and sustainability for PMM and Plastics Recycling.
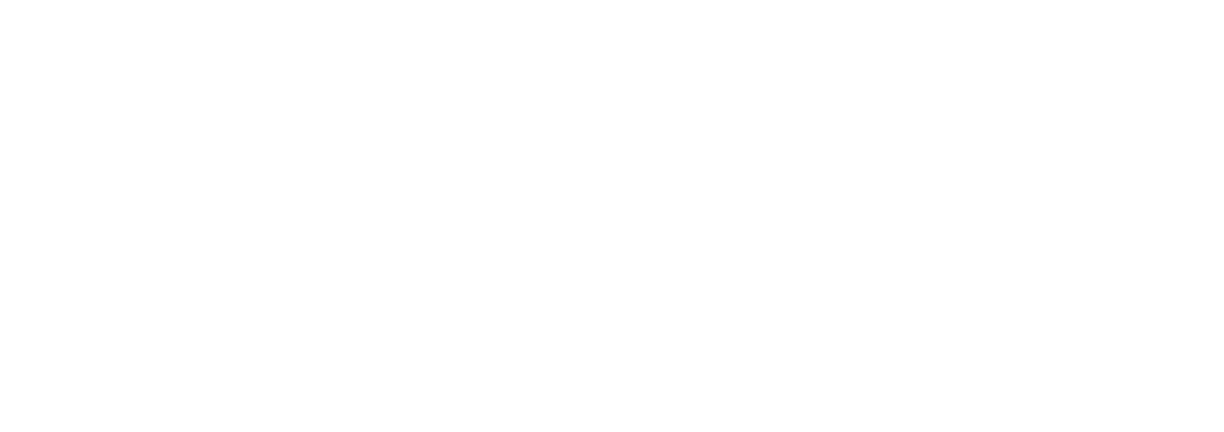