Auxiliary equipment supplier Conair Group, Cranberry Township, Pa., now has a fully equipped extrusion lab operating in Pinconning, Mich., a site located within its factory where the company's downstream equipment is produced.
The 8,000-square-foot lab now is home to five production-scale extrusion lines ranging from 1 inch to 3.5 inches, and the required downstream equipment including the vacuum sizing tanks, such as single-pass tanks that are used for small-pipe applications or the multi-pass tanks for higher extrusion rate applications.
It is all in the effort of promoting Conair's downstream equipment for extrusion, officials recently told PMM. The company wants to be able to do full line trials and it is staying plenty busy.
Within the lab space, Conair (NPE Booth W2143) is conducting factory acceptance testing (FAT) and trials for extrusion companies. The site is staffed full time by Dave Czarnik, Brian Hilton and Tony Sowiecki, each of whom is a process engineer. Together, the group has 72 years of experience. Czarnik manages the operation and is a tooling expert who holds five extrusion-related patents; Hilton is a downstream application expert; and Sowiecki's 17 years of extrusion experience has been with material suppliers, processors and Conair.
Recent work at the lab has been focused on perfecting on-line gauging and adaptive control for the extrusion of precision medical tubing, for example, tubing for cardiac and brain catheters.
"We do a lot of work with medical manufacturers helping them develop process improvement," Czarnik says. "I would say at least 40 percent of what we do in the lab is medical related."
Extrusions in medical applications include bump tubing, co-extrusions, micro-extrusions and multi-lumen tubing. In bump tubing, each end of the tube is a different diameter; multi-lumen tubing has multiple holes for medical necessities such as the delivery of certain fluids.
Since the economic turnaround, however, the lab also is seeing an uptick in automotive, including projects such as multilayer fuel lines. Construction is another active market for the lab, because the equipment can be ramped up to larger sizes to run trials for the extrusion of siding, pipe or profiles. Conair also is seeing more demand for filaments needed in 3-D printing.
Extruders installed at the site have product-specific screws, melt pumps, high temperature capabilities for resins such as fluorinated ethylene propylene or PEEK, and discrete controls and microprocessor controls. The latest in-line gauging equipment includes a three-axis laser gauge, a four-transducer wall unit and a Beta LaserMike Laser Speed 9000. Vacuum-sizing technology includes a closed-loop vacuum system, single- and dual-zone water temperature control system, flip-up precision roller system, an easy-clean feature for medical applications, external water level adjustment, and a vacuum chamber-mounted/wall gauge-mounted digital remote potentiometer with readout.
The lab's belt puller and cutter technology includes full taper/bubble tube capabilities, a dual servo-drive puller for extremely precise speed control, scrap modes, full gauge interface control potential, and cutting modes to allow any cutting, including angle cuts. Also available are an air regulator with high-speed analog of 0 to 10 volts DC, and capabilities to integrate both internal air and vacuum sizing.
Angie DeRosa, managing editor
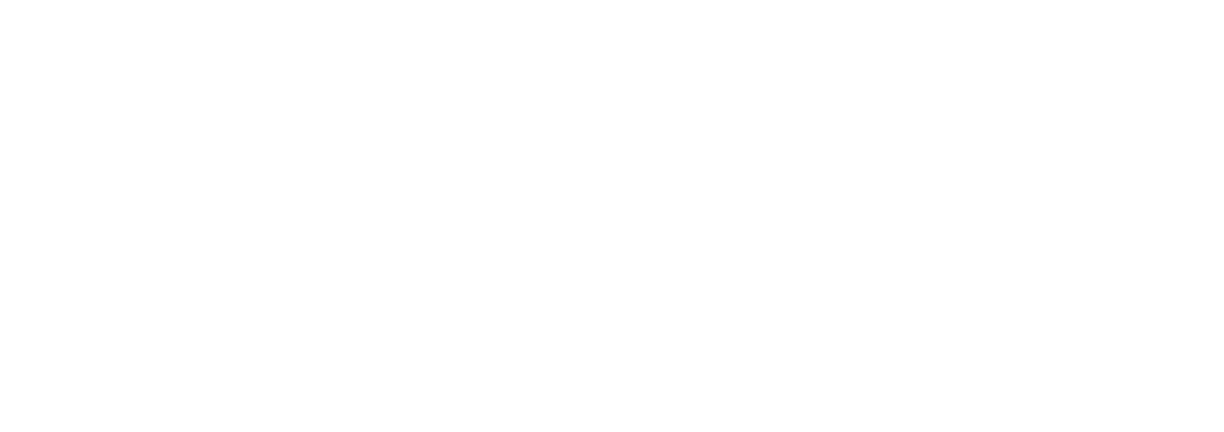