Reducing energy bills is a compelling issue for virtually every plastics processor, and machinery suppliers have responded with a very wide range of innovations designed to reduce the energy needed to make plastic products. The injection molding sector's efforts have garnered the most attention—fully electric presses, hybrids, variable displacement pumps and servomotors, to name a few. Likewise, numerous energy efficiency innovations are available for blow molders and extruders, including many from auxiliary equipment suppliers.
Less has been heard about reducing thermoforming energy costs, but infrared (IR) technology for heating extruded plastic sheet prior to forming offers a thermoformer a way to lower its kilowatt intake significantly.
Now, energy savings for thermoformers has been documented as a result of a side-by-side comparison study, and the savings already are being enjoyed by thermoformers in North America and beyond.
With the cooperation of one of its thermoformer customers, Ceramicx Ltd., Ballydehob, Ireland, a global supplier of infrared heating systems for thermoforming and other industries, commissioned a "real world" research study that confirmed a 40 percent energy savings with an infrared thermoforming heating system, when compared with a conventional Calrod heater.
But rather than turning to a lab test, Ceramicx commissioned an independent study to be done using two identical thermoforming machines on its customer's factory floor. The only difference between them: one was equipped with a Ceramicx IR heating system and the other used a conventional Calrod heater.
The independent study was conducted by Robin Kent of the plastics consulting engineering firm Tangram Technology Ltd., who measured and recorded the detailed differences in energy consumption between the two systems.
Direct comparisons between the two thermoforming lines at the customer's facility were further ensured by having identical tools making the same products at the same cycle times. The measuring equipment for electrical testing measured all three phases of the complete incoming supply to the thermoforming machine and used a single-phase supply (phase to neutral) as a reference voltage for the calculations.
The Ceramicx heating system decreased the average power drawn from 56.16 kilowatt for the Calrod system to 32.85 kW, a 41.6-percent reduction. Figures were taken to show a direct comparison between the two oven systems. With the machine base loads removed, the Ceramicx system showed a measured energy saving of 45.8 percent compared to the Calrod system. Additional study showed that further improvements and energy savings would be available with the Ceramicx-based system.
Each thermoforming machine was making the same polystyrene-based products for consumer and food service markets. The IR-based oven platen and control system was designed and built at the Ceramicx manufacturing facility in West Cork, Ireland, and shipped directly to the customer's manufacturing facility.
The oven has a total of eight built-in temperature sensors that can be selected individually or grouped for control purposes, and the heaters can be subdivided into as many as 132 separate zones to enable a wide range of control options. The Ceramicx system includes upper and lower heating platens, power control systems, enclosures, switchgear, and PLC control.
A total of 420 IR elements were deployed in this particular oven system. Each Ceramicx-made element has a unique and traceable heating fingerprint, the performance of which is documented and verifiable online. The oven assembly is fitted with pneumatic cylinders that are operated manually via two solenoid valves. The lower platen serves as a counterweight, using steel rope and pulleys. The control systems give the processor a choice of open- and closed-loop control, cost-saving startup procedures, fault monitoring and inline process energy control.
Ceramicx founder and managing director Frank Wilson said, "We are pleased to confirm through scientific study and measurement what we have always intuitively known — that Ceramicx-built IR heat solutions give fantastic and immediate savings for fast-cycling thermoformers."
Ceramicx was with its U.S. distributor, Weco International Inc., Clio, Mich., at the 2014 Society of Plastics Engineers' Thermoforming Conference in Chicago, explaining to attendees that many thermoformers were using IR heating to reduce process heating energy by around 40 percent. There are several testimonials by thermoformers to that effect on the Ceramicx website.
"What's exciting about this work is that it shows how fast-cycling thermoformers can realize immediate savings on energy and its costs, in addition to improving product quality. Not only that, their packaging can legitimately claim to be 40 percent greener, with a de facto 40-percent reduced carbon footprint. It really is win-win for the thermoformer," said Brett Wehner, CEO of Weco International, speaking about the results of the comparison study.
The Weco/Ceramicx booth at NPE2015 will lay out all of its energy saving messages and benefits in full, he said.
"We will provide full production details on just how these numbers are achieved."
Rob Neilley, senior correspondent
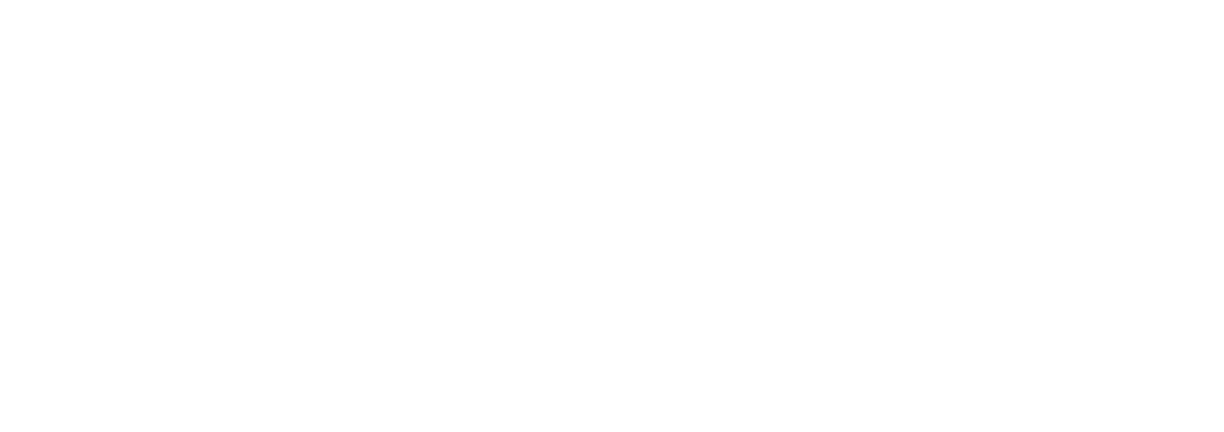