In-line thin gauge sheet production is an exacting process that requires highly engineered machinery and processing technology, especially at that critical point when the melt curtain exits the sheet die lips to begin its journey on the roll stand.
Processing Technologies International LLC (PTi), Aurora, Ill., has been working to achieve a master grip on multi-nip science and now is promoting its Super G Multi-Nip roll stand, a machine that officials unveiled in the fall.
Plastics Machinery Magazine participated in a tour at PTi on Oct. 7 where officials talked about the multi-patented system and process of perfecting it. Officials gave PMM insight into the inner workings of this equipment that stands 6.5 feet tall at its highest point with multiple access platforms. The platforms allow an operator to check roll gaps and clean rolls during maintenance periods. The operator can also cross the line and view the sheet as it is coming underneath the platform, therefore being able to view the final product. As this PMM issue went to press, PTi was performing demos and preparing to take commercial orders.
The Super G Multi-Nip is the evolution of PTi's Multi-Nip 7 system introduced in 2011, and the G-Series platform introduced in 2010, said Matt Banach, PTi's VP of sales and marketing. The Super G Multi-Nip borrows several features from the original series, including the J-stack configuration at a 45-degree angle to the die. That assures a better approach into the
primary nip and less chance for pre-skinning or pre-cooling.
Linear rail features, ratcheting nip height adjustment systems and the floor mounting support frame all were borrowed from the original G-Series. New features include digital servomotor gap adjustment, a thread-up leader system, and operator/maintenance accessibility elements such as internal energy chains, LED lighting and enhanced operator access platforms.
In total, there are five patents on systems that make up the Super G Multi-Nip that either are pending or have been awarded. The positioning system allows for multi-axis alignment and perfect seating. The roll skew mechanism, for example, is patent-pending.
There is a manual roll skew adjustment for the primary nip. The patented manual nip height adjustment is used to raise or lower the primary nip relative to the die and make adjustments on the fly for various sheet thicknesses. One operator can move the lever and make adjustments to change positions relative to the die.
Another patented technology is from the G-Series leveling base system. It features a heavy-duty frame structure to level the equipment at setup. On top of that is the integration of the machine tool-grade precision linear rails. It is all driven by an AC motor traction drive system with digital feedback. The primary nip position is displayed on a Titan PLC system. The optional Titan Plus control package also features more trending and data logging.
The ease of control is a key benefit of the machine. The complexity of a seven-roll system is simplified by the control package design. Because of this, one person can easily operate this system, Banach said.
"We have the ability to integrate everything into the control package, whether it is a single extruder system or a nine-layer barrier system," he said.
If, for example, an operator encounters a problem at the thermoformer and has to slow down the sheet extrusion line, he or she can put the machine into a crawl mode so that the machine is barely pushing material but is keeping it ready to go. Once the operator gets the problem solved, he can go back into run mode and the machine will automatically ramp up to the production rate.
A mechanical thread-up device also is a feature to assist in the safe and easy operation. That system consists of a hand-driven chain to pull a startup leader through the rolls.
"While this system is not recommended for all applications, it is ideal for high-quality sheet processes that demand tight tolerances and specific product metrics," said Tom Limbrunner, senior VP of applications and technology with PTi. A form-fill-seal application would be a great candidate. This particular roll stand will accommodate thicknesses up to 65 mils at 54 inches wide.
Seven high-precision, individually driven chrome rolls are the backbone of the system that has six nips. The roll stand has two 18-inch-diameter lead rolls and five 12-inch rolls. Rolls three and five are hydraulically actuated multi-nipping rolls which feature toggle action at the bearing housings. Another feature is 12 servo-controlled gapping devices and four zones of hydraulic power to control and vary the process roll loads. The benefits include high-clarity sheet with ultra-low orientation and residual stress. This is accomplished by maintaining uniform core temperature, which enables lay-flatness and dimensional stability.
In the four-zone temperature station, each zone consists of a pump, heater, heat exchanger and a modulating valve. The modulating valve is used for more precise temperature control.
Limbrunner said that ensuring efficient cooling of the sheet is key. With seven rolls and six nips in a J-stack configuration, good transfer of the sheet from one roll to another is paramount for advantages from a thermal stand point.
Angie DeRosa, managing editor
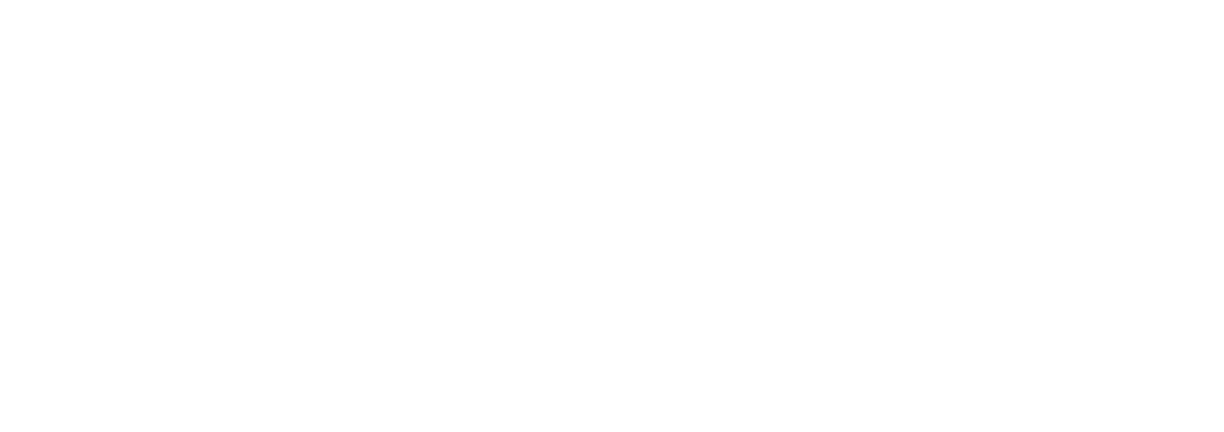