Within the walls of Makuta Technics Inc.'s 20,000-square-foot facility in Shellbyville, Ind., science is king. A sophisticated stable of Sumitomo Demag small-tonnage presses performs exacting work under the cover of night with no human interaction. The machines are micromolding components mainly for the medical device and pharmaceutical industries.
These components are so small that precise details, for example, a hole in a tip used in a device for the delicate transfer of embryonic cells, are barely visible to the human eye. The Embryo Cradle has a hole that is 80 microns in diameter. The tolerance is plus or minus 5 microns. The other way to think of the products Makuta produces is that the company only supplies parts whose geometric shapes are measured in microns.
In a part being molded for use in chemotherapy treatment, the process adroitly has to marry TPE and PP so there is no chance that medical professionals using the device will be exposed to the chemotherapy drug. Two 30-ton Sumitomo SE 30-DC S injection molding machines are being used to produce the valve. Each machine produces four parts per cycle.
At NPE 2006, a Sumitomo press was producing a Makuta part so minuscule that onlookers thought the machine was dry cycling. Some components, in fact, can be dispersed into a human hand through a saltshaker.
"Most of our parts nobody ever sees," says Makuta Technics President Stu Kaplan. "They're inside assembled devices."
Because the parts are so small and the demand for the products is high, there is another advantage that allows Makuta to run more efficiently.
"We don't hold inventory and we don't hold material," said Kaplan. "You make a part and you ship it."
If it so wanted, Makuta also has acreage to expand in the city of Shelbyville, which is located about 30 miles southeast of Indianapolis. Inside the walls of its building, 13 employees make it happen by day in this 24/7 lights-out operation. These are the Makutians.
Monday through Friday, Makutians monitor the equipment, clean and refurbish the molds, and conduct part inspections and quality control. Makutians also build and fine-tune camera systems and programmable logic controllers. That work alone saves the company untold time and money. One single-shot machine, specifically, an 18-ton Sumitomo SE18DU all-electric, has a Makuta-engineered and -manufactured PLC system using a Cognex camera. The mold produces a drug delivery device that is very complex, with a 200-micron pin meeting and mating with a 200-micron pocket to form the channels that deliver the drug and allow for airflow during the use of the device. A strobe/camera is attached to a Makuta-manufactured PLC that checks for the ejection of both parts from the mold.
Makuta Technics falls under the umbrella of the Sansyu Group of Takahama City, Japan. Its specialties include ultra-small precision injection molding, for example, an ultra-small bobbin with dimensions of 1.11 by 0.96 by 0.64 millimeters.
Makuta uses Sansyu's proprietary mold shuttling system. The two machines that mold the device for chemo treatment each employ the Sansyu shuttle system.
"We've not found anybody in this country that can do what Sansyu does," Kaplan said of the mold precision.
For Kaplan and officials from Sumitomo Demag, micromolding has required an educational process. Twenty years ago, the term "micromolding" didn't even exist.
"It's exciting because the technology keeps evolving," said Kaplan.
In the Makuta lab, a Stratasys uPrint 3-D printer is primed and ready to supply end-of-arm tooling. All of the tooling is made in-house.
Kaplan and company slowly are shifting to all-electric injection molding machines. It stands to reason with the requirements they need to meet for parts production, and Kaplan cites the "full package" to consider, including the consistency of each part from cycle to cycle. Sumitomo servo motors deliver that consistency. Sumitomo Heavy Industries Ltd. developed the advanced direct-drive servo motor technology specifically for the injection molding process.
"The ability of these motors to hold the pressure and position totally stable and the fast response of the motors are particularly important in micromolding," said Kaplan.
The control systems of Sumitomo's machines also have the firm's Flow Front Control capabilities, which take advantage of the viscoelasticity of the resin to fill out the part completely without overfilling.
"Flash is not an option in any of our micromolding processes and neither are short shots," Kaplan said. "A gear with micron-toleranced teeth is not going to operate correctly if the teeth are not fully filled."
The design of the clamp combining the five-point toggle with the center press platen design improves force distribution and platen parallelism, and protects the mold and the delicate mold components, he said.
Engineering manager Tyler Adams said the hydraulic machines will be used to supplement production.
"Electric machines are our bread and butter," he said.
The parts that are being molded cannot risk contamination, as all the parts that Makuta produces become part of a larger assembly. One component is being inserted into tubing that is used during colonoscopy procedures. The plant temperature is maintained at 72 degrees Fahrenheit and has Class 10,000 mobile clean rooms, and the factory maintains an atmosphere of 50,000, half-micron particulates (0.0005 micron per cubic foot). The carefully engineered process has achieved zero defects.
"We have to make sure every single part is right," said Kaplan. Components are being shipped all over the world from Shelbyville, for example hearing aid components to China, medical device components to Australia, and automotive components to Europe.
Technologies that Makuta Technics is focusing on include the SL screw assembly. Spiral Logic technology, marketed as the SL screw assembly, only is available in the United States on Sumitomo Demag machines.
"This is going to become the standard," predicted Kaplan of the plasticizing technology that eliminates shear heating. Since the manufacturing process has to be so exact, Kaplan and crew rely on technologies that eliminate the possibility for carbon contamination or other unwanted byproducts.
The SL screw design will be implemented on a two-shot machine in the next few months. Kaplan expects to install a 30-ton Sumitomo all-electric two-shot shuttle machine by the end of the year. The machine will be equipped with two SL screw and barrel systems. A Yushin dual-arm robot will be added to the cell along with cameras for inspection of all parts. The automation and inspection system will be designed and manufactured by Makuta, using Cognex cameras.
"With extremely small parts, there's a science to the mold and gating, to the material flow and nozzle shutoff, to the parts removal, to the inspection," said Kaplan. "Micromolding is far more complicated than people realize."
Angie DeRosa, managing editor
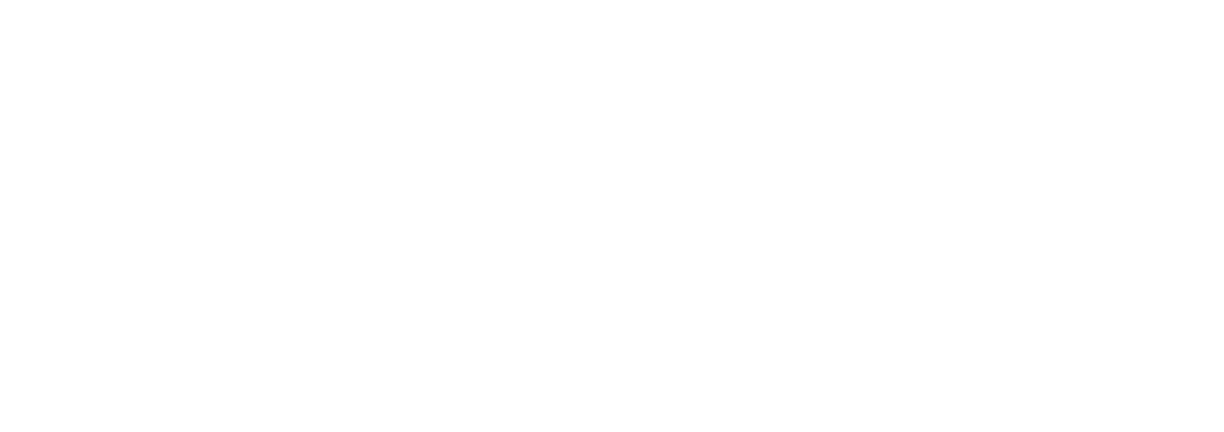