Plenty of injection molders are wondering whether the time is right to buy a 3-D printer, but an Ohio company that started with 3-D printers and later added injection molding machines shows how the two processes can complement each other and open doors for new business.
"We try to help our customers figure out what is best for their part," said Greg Cebular, VP of sales and project management at The Technology House in Streetsboro, Ohio.
"We are able to look at how their part is being used, the material and budget, and say, 'Here are the different options for processing.' We may decide injection molding is best, or we may decide 3-D printing is the best option. Our team is able to look at all the different options."
The Technology House has been 3-D printing production parts for about 15 years, an outgrowth of its original rapid prototyping business. Early prototype customers sometimes found that the prototype part worked well, so they just kept ordering more.
Today, The Technology House has 11 injection molding machines, with clamping forces ranging from 30 tons to 600 tons, plus six state-of-the-art Carbon CLIP printers, five stereolithography (SLA) printers, three lab printers and one industrial fused-deposition-modeling (FDM) unit. It also has substantial cast-urethane and CNC machining capabilities.
The injection molding and additive manu-facturing sides of the business are currently growing at about the same rate, said President Tracy Brent.
"The additive manufacturing side of the business is changing as more and more companies build out the additive manufacturing sides of their own businesses," she said. "Now, we do different things for them. On the injection molding side, we have added different machines. This is a big opportunity for us."
She said that some customers use The Technology House for multiple services while others may contract for just prototyping or injection molding or machining.
Chip Gear started The Technology House 22 years ago when he bought one SLA machine and associated equipment, as well as a Pro E modeling software license. He recognized the business opportunity in reducing tooling delivery times, which could be as long as 18 months. The new company created 3-D printed models for prototypes, which sped up design and validation checks before the metal tool was built.
That first SLA machine, from 3D Systems in Rock Hill, S.C., along with associated equipment and software, cost about $1 million. That machine is still running today.
"The company has grown by adapting to where our customer base is going," Cebular said. "Early on, we got into the health-care and medical fields and a couple of our customers were using SLA machines to make masters or patterns to build cast-urethane parts, so we started making cast-urethane production parts.
"You take an SLA master part, create a silicone mold around it and do a vacuum or gravity pour of a two-part polyurethane material to create the actual part," he said. "Then we finish, paint and ship the part."
Later, design and prototyping customers led The Technology House into manufacturing very complex parts in small-volume runs of a few thousand parts a year.
The first injection molding machine came in 2000, and the first Haas CNC center arrived a year later.
"We started getting into higher production volumes, and we kept running into opportunities," Cebular said. "We had a lot of interest from medical companies."
The company started going after more production work in 2008 but did not neglect the other parts of its business. It established a subsidiary, Sea Air Space Machining and Molding, and won certifications for medical and aerospace parts.
The Technology House is working toward becoming an around-the-clock manufacturer of 3-D printed parts.
"We have one technician with a pager each week. When it goes off, he comes in and changes out the machine and starts the next run," Brent said.
"We like to start print runs in the mornings so they can run all day. At the end of the 12-hour day, we like to put on long runs that can go all night. The idea is to get to a 24/7 schedule," she said.
The centerpiece of The Technology House's additive manufacturing business is six Carbon CLIP machines. The company was a beta test site for Carbon Inc., Redwood City, Calif., from October 2015 until March 2016, when Carbon started selling its M1 printer to non-beta companies. By the end of this year, The Technology House will have six Carbon M2 systems, the latest version.
The Technology House continues as a beta test site for Carbon's material mixer and Smart Part Washer. It is also a production partner, which means the two companies work together to improve production processes. They are currently working together to develop a way to 3-D print lattice structures.
The Carbon CLIP process was developed in 2013 by Joseph DeSimone, who made the printer only after creating a wide range of materials for it. The printer — its full name means continuous liquid-interface production — uses a process Carbon calls digital light synthesis, or DLS, to shape light-curable resins. Carbon's materials, mostly two-part resins that are mixed before going into the printer, provide better surface quality and mechanical properties than other resins used in additive manufacturing.
Mike Wright, director of product development and engineering at The Technology House, said traditional SLA printers are good for prototypes but the Carbon printer is far better at making production parts. "If you want to make a part to show that something fits together, SLA is good. But the Carbon is for 'the go.' You can go into production with these parts."
Brent said the Carbon machines offer growth for the business. "Having new technology like the Carbon machines that give customers different types of materials that are not offered in other technologies has been a big area of growth for us."
For the Carbon printer, the material is mixed according to a pre-determined recipe, then loaded into a cassette that is placed into the printer. From the time a model of a part is loaded into a connected computer, a typical print run can take anywhere from 15 minutes to six hours. A Carbon M2 printer has a build volume of 7.4 inches by 4.6 inches by 12.8 inches. The system can be automated with robots to perform functions such as parts removal.
After a part is printed, a technician puts it in an automated washer, where it undergoes a 10-minute wash cycle to remove excess resin. Parts are washed with the build platform and sometimes small supports still attached, but these are removed by hand before the parts go into an oven for curing. Depending on the material, parts stay in the oven for four to 12 hours.
The light in the Carbon printer shapes the part, but the baking process brings out its final properties.
Carbon provides its machines only on a subscription model. All are connected electronically to Carbon's technical center. "If they detect a problem, they can tell us and send a software patch," Cebular said. Carbon can monitor the printer but does not have access to information about what is being printed.
The Technology House's five SLA machines, all from 3D Systems, also stay busy. They currently run at about 65 percent capacity on a 24/7 basis.
Like the Carbon process, SLA produces parts that have to be washed. After that, they are then bead-blasted to achieve the final finish. About 5 percent of the SLA parts are for production, Brent said. The rest are prototypes.
The SLA machines can run five resins.
Some customers have been ordering production parts made by the SLA machines for several years. The Technology House charges one customer $4 to $10 per part for any of 10 variants of a small, complex nozzle. Because the customer orders only 100 to 1,000 of each nozzle variation per year, building 10 different injection molds would be impractical.
"They order it, we print it and, within a week, they have all the parts they need," Brent said. "And they are able to mix and match on the batches they order. If they need 100 of this one and 100 of that one, we can do that."
The injection molding side of the business has a 30-ton vertical Newbury, which was purchased used years ago. The Technology House uses it with a 1-plus-1 mold to overmold connectors on pre-cut lengths of cable.
Other injection molding machines are from Milacron and Van Dorn. The newest are Haitians with clamping forces of 190 tons, 315 tons, 360 tons and 600 tons. "We looked at several manufacturers, but ... the Haitians offered good value for what we needed the presses for," Wright said.
The plant has an overhead crane to facilitate mold changes, which occur as often as 30 times per week.
"We are very rarely running the same jobs at the end of the week that we started at the beginning of the week," Brent said. "We are geared up to have the flexibility for what we need for our current business." With its rapid prototyping background, the company has a culture of being flexible and quick, she said. "It does not faze us to change tools so frequently."
Because of the short runs, the plant does not currently use robots, but it expects to add them as its long-run production work increases.
While The Technology House does not release annual sales figures, Brent acknowledged that annual growth has been steady, in the 5 percent to 10 percent range. It moved into its current 50,000- square-foot plant in 2015 and kept its previous, 35,000-square-foot plant for its Sea Air Space subsidiary. The two operations employ 75 people.
The company is moving more into contract manufacturing, including assembly. "We have always made parts and done finishing work and painting," Cebular said. "For some customers, we are keeping finished goods in stock.
"When we get a release, we ship the finished part or assembly, then build more within the same week for our inventory."
He said one customer was shipping about 30 individual parts to The Technology House for assembling and finishing work. "They were having to manage inventory and we were having to manage inventory, so we started working with them to build the mechanical assembly, so all the customer has to worry about is the electronics," Cebular said.
"Our owner's philosophy is to be completely vertically integrated, so we can control quality. We want to be able to come in and manage everything for the customer. We can do the additive parts, molded parts, machined parts and purchased parts. Then put everything together into a final part, put a label onto it and ship a single, final part."
The Technology House uses the JobBoss ERP system to manage production, from quoting to purchase orders, plant floor activities and quality management.
Sea Air Space has a coordinate-measuring machine, and Cebular said The Technology House is looking at adding visual scanning equipment at the Streetsboro plant. "As we get into more production with critical parts, it will help our flow," he said.
What does the future look like? In addition to growing the injection molding business, Cebular said the company expects to add significantly more additive manufacturing machines. Consumer companies are showing great interest in additive manufacturing as mass customization becomes more important.
"We have been surprised at how many consumer companies are looking into additive manufacturing," Cebular said. "We were not thinking they were going to jump in, considering that most of their product lines are in the millions. But they see the technology expanding in five to 10 years, and they know they have to start working on it today."
Ron Shinn, editor
Contact:
The Technology House Streetsboro, Ohio, 440-248-3025,
Ron Shinn | Editor
Editor Ron Shinn is a co-founder of Plastics Machinery & Manufacturing and has been covering the plastics industry for more than 35 years. He leads the editorial team, directs coverage and sets the editorial calendar. He also writes features, including the Talking Points column and On the Factory Floor, and covers recycling and sustainability for PMM and Plastics Recycling.
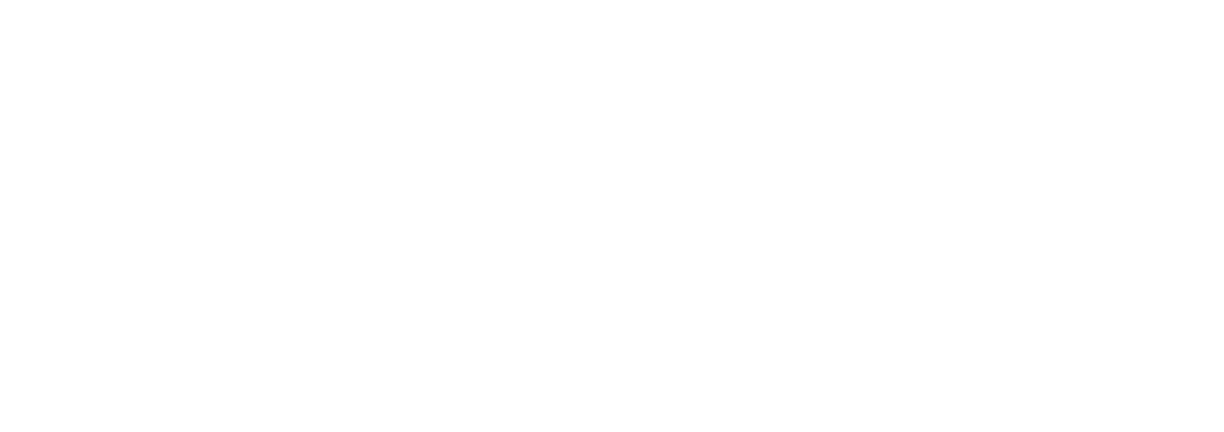