Problem: A North Carolina molder needed to squeeze in two big presses under a roof that was not high enough.
Solution: LS Mtron supplied presses with retractable tie bars that have freed up space and made moving molds easier and safer.
By Karen Hanna
Stanford Manufacturing puts a high ceiling on its outlook for the future — but to get there, it needed about 7 feet of additional vertical space to make room for bigger machines that could handle a new job involving parts for the materials-handling sector. Most injection molding machinery makers ducked the challenge.
Not LS Mtron.
It recently helped install two injection molding machines (IMMs) that fit the bill, bringing the Clemmons, N.C., injection molder’s total number of presses to 11. In all, from quote to delivery, LS Mtron needed just six months to guide its customer up through installation — a turnaround that was only that long because Stanford Manufacturing encountered some unrelated issues, said Jack Elliott, the molder’s business development director.
In sizing up the project, he identified three major challenges: “The first was the height. ... The second was the fact that most machine builders right now, they put all their hydraulic lines and everything right on the bottom of the machine. What most machine builders have gotten to is they want people to fully automate, have robots and overhead retraction of parts or side-loading robots, etc., which are a.) very expensive but b.) not always the case for every single product to project; some things do need to drop out of the bottom still. ... The other part was, since these parts are so large and they are dropping out the bottom, you needed 36 inches of clearance.”
Tooling for the parts is enormous.
Elliott laid out the numbers: “50 inches vertical by 44 inches wide, operator to non-operator side, and 41 inches on the stacked height. But we also have a 30-inch hydraulic unit that sits on top of the mold and 6 inches on the bottom of the mold that are not included in the above numbers. So we’re looking at 87 inches of needed height clearance, just for the tool.”
But big molds are nothing new for LS Mtron, said Peter Gardner, president of LS Injection Molding Machine USA.
“A lot of these molds that customers are running just have a lot of things hanging off of them, hydraulic cylinders or core pulls and hoses and all sorts of things, so it gets bigger and bigger,” he said.
Typically, molders would use a crane to move tooling of that size. But, for Stanford Manufacturing, that’s hardly ideal.
“I don’t think anybody wants something the weight of a Range Rover hanging over people’s heads,” Elliott said.
Of the OEMs Stanford Manufacturing approached with the challenges, LS Mtron truly stepped up and cleared the bar, according to Elliott.
Worker safety was one important consideration in spec’ing out machines, Gardner said.
With thousands of IMMs installed around the world at both its own plants and customer facilities, the LS Group has developed solutions to problems that cause its competitors difficulty, Gardner said. The group includes LS Mtron, along with makers of a huge portfolio of consumer goods, including razors, electronics and appliances.
One of LS Mtron’s solutions — the ability to retract IMM tie bars— frees up space and makes moving molds easier. Being able to remove one of the tie bars allows the mold to be inserted from a lower height.
While tie-bar retractability isn’t necessary for smaller machines, the option proved a perfect fit for Stanford Manufacturing’s IMMs.
“We can do it all the way down to a relatively small 550-ton machine. We can do tie-bar retraction, either on the operator side or the non-operator side,” Gardner said. “It’s obviously sometimes just a no-go to try to modify a building. ... One of the reasons we’ve kind of become good at this is we do a lot of molding ourselves within the LS Group. ... In Tennessee, we have a plant full of LS machines at LG Electronics, making washing machines and dryers, and having the tie-bar retraction on those machines really helps to actually, even if you could squeeze [the mold] up and over the tie bars, it just makes it a lot quicker and safer."
With that been-there, done-that approach to accommodating large IMMs, LS Mtron was able to supply a solution to a problem that was otherwise impossible — how to fit two presses into a building with a roof that’s nowhere near 30 feet tall.
“Having that tie-bar retraction was huge for being able to actually retract it and then load it from the side,” Elliott said.
At the push of a button, the tie bar safely retracts from the machine in about 60 seconds.
“I just think, inherently, the lower you have to lift something very heavy up, the more manageable it is, and it’s safer,” Gardner said. “You can help guide that mold into the machine where, if it’s up so high, nobody can really get ahold of it on either side to really guide it in.”
He said a chime sounds to warn operators when molds are in motion above their heads.
Another solution lies underneath the machines — a custom base that allows them to eject parts from the bottom.
Considering the tooling itself weighs about 10 tons, the bases have to be robust.
But, as Gardner observed, adding bases to machines that already present size challenges is a Catch-22. That’s another reason why being able to retract the tie bars, to free up space, was so critical.
“Customers, they have a particular mold or product they want to drop down onto a conveyor and run out underneath the machine, no problem,” Gardner said. “We build lots of high-base machines. So, we can build the high base and then they’re like, ‘Oh, [shoot], now we can’t get the mold in over the top of the tie bar because of the ceiling height.’ A lot of times you end up fighting those two battles. And, so, we were able to satisfy both of those.”
The machines have clamping forces of 1,200 tons and 770 tons, though because of the challenges Stanford Manufacturing faced, the 770-tonner is a bit of a unicorn — it includes aspects of a smaller machine.
“Stanford ordered a 660, but we built it with the mechanics of the 770 for space reasons,” explained Paul Caprio, president of sales for LS Mtron Injection Molding Machine USA. “After we installed it, they asked if we were able to convert it into a 770 with our software, so we did.”
Initially, Stanford Manufacturing projected that a 660-ton IMM would workl. But, as it worked with LS Mtron, it realized the benefits of greater flexibility.
For LS Mtron, neither the tight space nor the challenge of mixing and matching machine components presents an intractable problem.
Whether retracting the tie bars, building a new base or swapping out parts, Gardner said it’s all in a day’s work for a company that, like its customers, relies on the machines it makes.
“We’ve seen every kind of situation out there, from small machines to large machines, and the types of manufacturing challenges that our customers have, we’ve already had them, so we’ve gotten good at it,” Gardner said. “Some competitors either don’t offer [retractability], or they offer it so rarely that it’s very expensive and adds a lot to the lead time. ... Because of the economies of scale, the cost to add it really is not extravagant. Most customers are a little surprised that this is an easy solution for them because they were wringing their hands about how they’re going to run this big new mold.”
Having just opened a new facility to handle warehousing and order fulfillment, Stanford Manufacturing is gearing up for additional acquisitions. Elliott said it’s doubled in size since it opened for business in 2017, and its workforce now numbers just less than 100 employees.
All that success comes down to three factors, he said: quick lead times, great customer service and high quality. They’re the same reasons he said he’s so impressed with LS Mtron.
“I think what folks are starting to figure out is that you can actually manufacture stateside at similar cost, even regardless of the tariff situation,” he said. “We’ve been seeing a very high amount of RFQs coming in, and we’re getting to the point that as much as people are picking and choosing us, we're picking and choosing the right partners.”
When it’s ready again for new machines, Stanford Manufacturing already has identified at least one OEM that it knows can meet its high standards, according to Elliott.
“There's great partners out there like LS that will go above and beyond to create solutions for their clients," he said. “I knew that we would find the right partner, and we did.”
Contact
LS IMM USA, Battleboro, N.C., 252-984-0700, www.lsmtron.com
Karen Hanna | Senior Staff Reporter
Senior Staff Reporter Karen Hanna covers injection molding, molds and tooling, processors, workforce and other topics, and writes features including In Other Words and Problem Solved for Plastics Machinery & Manufacturing, Plastics Recycling and The Journal of Blow Molding. She has more than 15 years of experience in daily and magazine journalism.
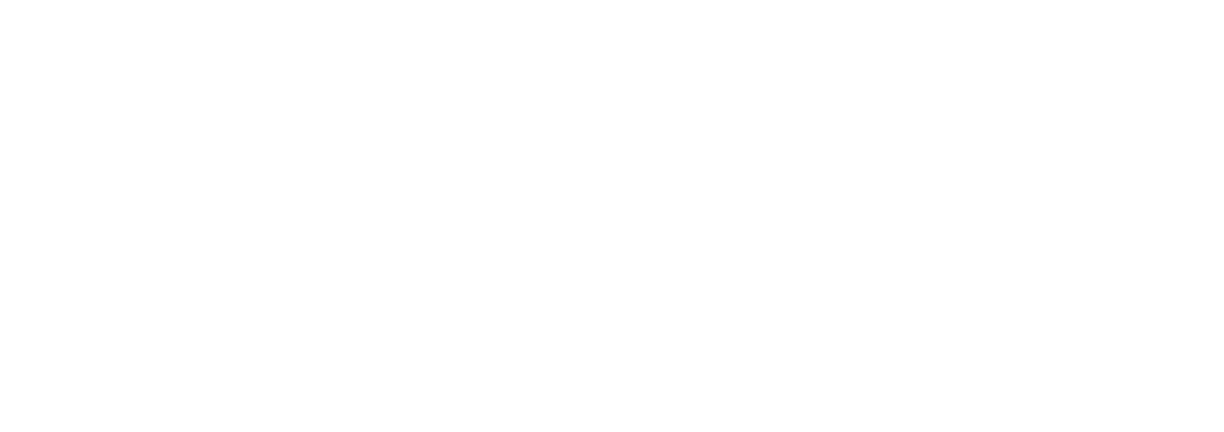