As Plastics Machinery & Manufacturing marks its 10th anniversary, the staff is looking back on the events and issues that shaped our coverage over our first decade. Read more of our 10 Trends for 10 Years here.
By Bruce Geiselman
Lightweighting plastics is an ongoing trend that can save processors and product manufacturers money, reduce plastic consumption and carbon emissions, trim transportation costs and reduce waste.
This sustainability effort is employed in nearly every industry ranging from packaging to sporting goods to the automotive and aerospace industries. It involves reducing the weight of a product or material while maintaining its performance and functionality. Extrusion, injection molding and blow molding processors as well as additive manufacturers are employing lightweighting techniques.
For example, in packaging, processors are increasingly using thinner or more flexible materials, such as thinner plastic films to create flexible pouches or bags that are lighter than rigid containers but provide a barrier against moisture and air. Plastic pouches now use less plastic than rigid containers, but they also can be more protective. A flexible pack may be able to handle the rigors of e-commerce better than a rigid pack. If a rigid package gets dropped, it may crack, dent or break, whereas a flexible pouch may be able to handle those challenges better, Todd Bukowski, an industry consultant with PTIS, told PMM in a 2021 article.
As governments and corporations embrace sustainability initiatives, their efforts are helping fuel interest in thin-wall containers and thin-wall packaging, Michael Sansoucy, VP of business development and turnkey solutions at Arburg Inc., said last year. However, the ability to embrace thin-wall packaging can involve investment in new processing equipment.
Automobile manufacturers also are embracing lightweighting plastic parts as they attempt to increase mileage of internal combustion engines and ranges for electric vehicles.
Additive manufacturing is contributing to the lightweighting of products in part because of the ability to print geometrically complex shapes, like lattice structures, that can lightweight plastic products like orthotics, athletic shoe soles, and bicycle seats.
Bruce Geiselman
Senior Staff Reporter Bruce Geiselman covers extrusion, blow molding, additive manufacturing, automation and end markets including automotive and packaging. He also writes features, including In Other Words and Problem Solved, for Plastics Machinery & Manufacturing, Plastics Recycling and The Journal of Blow Molding. He has extensive experience in daily and magazine journalism.
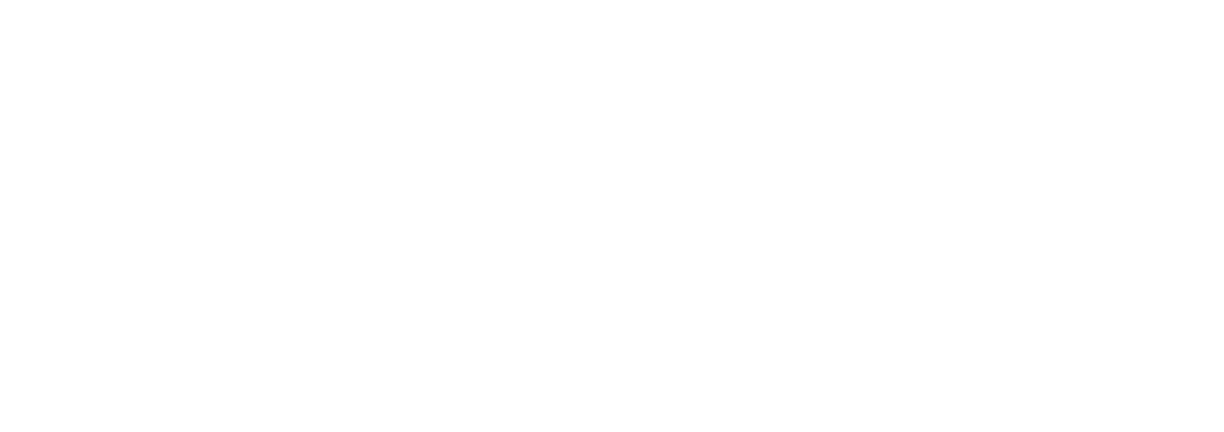