Sensors, AI, cloud computing boost efficiency and reduce energy consumption
By Bruce Geiselman
Sensors that detect melt conditions in real time can help processors reduce cycle times and waste, according to sensXpert, which provides the equipment — along with artificial intelligence (AI) and machine-learning technologies — to optimize plastics processing and reduce costs.
By optimizing cycle times, rather than overheating parts, processors can realize energy savings that percentagewise can run into the double digits. With real-time data about plastic melt conditions, the sensXpert technology, commercially available since 2021, predicts when parts are ready to be demolded.
The technology works with a variety of technologies including injection molding, thermoforming, compression molding and resin transfer molding. It can run on molding machines from any manufacturer.
In the future, sensXpert hopes to offer sensors to extrusion processors.
“We are working on the next generation of sensors — contactless sensors — where we are not in contact with the material anymore, so that we can in the future also support filament winding, extrusion and pultrusion processes,” sensXpert CEO Cornelia Beyer said. “This is coming in the future.”
SensXpert is a corporate venture of the Netzsch Group, an international technology company headquartered in Germany.
SensXpert’s sensors are in constant, direct contact with the raw material in the mold. They detect molecular movement through an alternating electric field. As the material cures, variations in movement help evaluate changing properties, according to the company. Paired with pressure transducers and thermocouples, they capture crucial information like resin viscosity, cure progression and crystallization.
The sensors connect directly to a sensXpert edge device, which the company calls its “blue box.” The edge device also can connect with auxiliary processing equipment.
“We connect via OPC-UA to the machine and gather information, but also via OPC-UA, we can connect to other peripheral equipment,” Beyer said. “It’s not only the molding machine, but dosage machines and many different kinds of machinery involved in the processing of a part.”
Each molding machine is equipped with its own edge device that stores and analyzes data and communicates with sensXpert’’s cloud-based network. Machine learning algorithms are trained in sensXpert’s cloud environment through artificial intelligence to recognize material characteristics and proper operating parameters. Information is then sent back to the edge device to predict cycle outcomes. SensXpert is able to automatically stop a cycle when a processor’s desired degree of cure is reached and open the mold, according to the company.
The edge device also sends information to sensXpert’s WebApp, an interface that allows machine operators to monitor their molds and manufacturing processes in real-time. The WebApp platform displays an array of process and material parameters including predictions on the trajectory of a material’s degree of cure or crystallization, glass transition temperature and other properties, according to the company.
“The information that we receive via our dielectric sensors is sent to our edge device, and it gets evaluated in real-time,” Beyer said. “How the material behaves in mold is what we receive at the edge, and the information there will be translated into crystallization behavior — degree of cure. So, we tell the processor in the end when his part is ready.”
SensXpert is not interested in a client’s intellectual property, such as recipes, instead working with its own data collected from dielectric sensors. To keep a client’s proprietary data secure, sensXpert transmits data via 5G technology rather than using a client’s internal computer network, Beyer said.
Knowing precisely when a part is ready to be demolded leads to energy savings, she said. The technology means that processors don’t need to rely on a simulation or a material data sheet to know when to expect a part to be ready. She compares the traditional method of calculating part molding time based on material data sheets to making a cheesecake with a recipe that calls for 60 minutes of baking time.
“After 60 minutes, you get it out, and you hope for the best,” she said. “This is why companies tend to overcook their part, just to make sure it’s ready and it’s not undercured or under-crystallized.”
Batch-to-batch variations in plastics resin can significantly impact the curing behavior of plastics. Factors including humidity, the age of the material being molded and mixing ratio variations can influence curing times.
“If you can analyze those, you know efficiently when the part is ready, and, of course, based on this, the energy consumption ultimately decreases because of being able to dynamically control your process,” Beyer said.
The amount of energy savings a plastics processor can achieve with sensXpert technology depends on a variety of factors including current cycle times and the ability to reduce those cycle times. As one example, Beyer said sensXpert optimized the vacuum-assisted resin transfer molding (VARTM) process for a global aviation OEM, where processing times traditionally reached 400 minutes, including autoclave curing. Through dynamic adjustments, sensXpert reduced VARTM cycle times by up to 30 percent, with energy savings as high as 23 percent, according to the company.
The energy savings and cycle time reduction benefits represent peak savings achieved over long-term use, demonstrating the potential for processors to continuously enhance efficiency with each cycle.
“If you have a process, for example, that is maybe a minute or two minutes, we can reduce maybe 10 percent. Of course, these energy savings are smaller,” Beyer said.
Processors also can see energy savings because their scrap rates are reduced due to more-accurate molding times and parameters.
“Because we are able to detect material parameters, we can avoid scrap,” she said.
Clients usually start with the sensors on one molding machine to prove feasibility, but after seeing positive results, they continue to roll out the technology. SensXpert technology, which is marketed as a service product, does not involve an expensive investment. The company provides a service contract to the client with the hardware included in the cost.
The technology is particularly beneficial when used on machinery producing high-end, expensive parts where quality and efficiency are critical. However, even when molding parts that cost only 15 cents, for example, a manufacturer can amortize the cost in less than three months, Beyer said.
As companies look to use more recycled materials, sensXpert anticipates greater demand for its technologies, which can help overcome process fluctuations caused by material variations
“We already are working with and evaluating recycled material behavior,” Beyer said. “We have a profound knowledge now, and we see that the dielectric measurement principle works. So, we can be very helpful. We are in what I would refer to as an alpha tester phase working with the first clients using recycled material in the process to build up this database, this knowledge, so that we can service on a larger scale our clients.”
Although based in Germany, sensXpert, has customers in the U.S., which Beyer called an important market. She said she was surprised at NPE2024 by the level of interest from plastics processors looking to reduce costs and boost process efficiency.
“Cost efficiency is so important for the U.S. market and process optimization,” she said. “Their hunger for innovation is so much bigger, and their willingness to look into new technologies is so much greater in the U.S. In Europe, it’s still very conservative.”
U.S. processors largely were interested in discussing sustainability initiatives and how sensXpert's technology could help with processing recycled materials, she said.
Contact:
SensXpert, Selb, Germany, 49-9287-750, www.sensxpert.com
Bruce Geiselman
Senior Staff Reporter Bruce Geiselman covers extrusion, blow molding, additive manufacturing, automation and end markets including automotive and packaging. He also writes features, including In Other Words and Problem Solved, for Plastics Machinery & Manufacturing, Plastics Recycling and The Journal of Blow Molding. He has extensive experience in daily and magazine journalism.
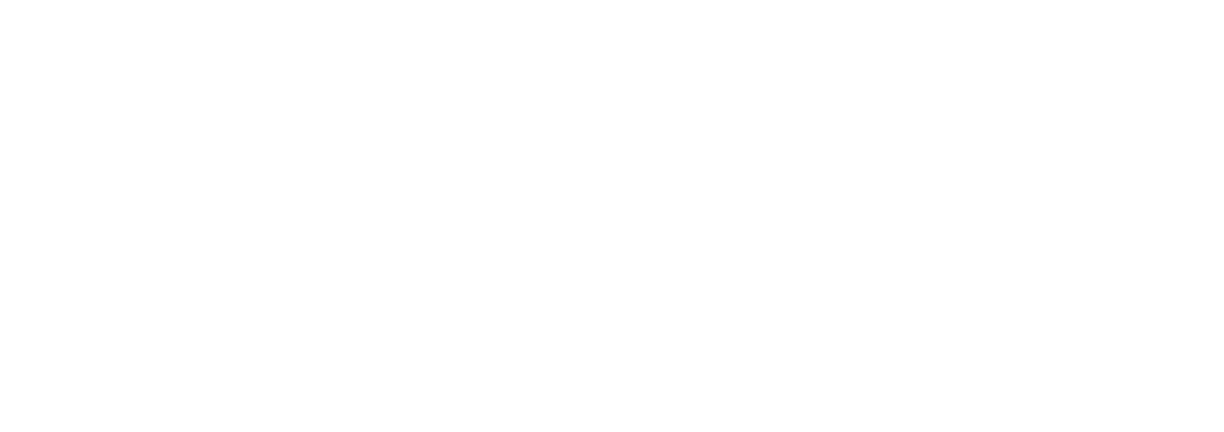